前回ではDXが「デジタル技術を利用して様々な変革を起こし、企業の競争力を向上させる」という概念であることを解説しました。では具体的に製造現場にDXの概念を取り入れていくにはどうすればよいのでしょうか。今回からお話をしていきましょう。
(執筆:関伸一/関ものづくり研究所)
関連記事:【第1回】ものづくりDXを机上の空論にしない
関連記事:【第3回】トヨタ生産方式とDXは相性抜群! ― 作り過ぎのムダはデジタル技術で簡単解決
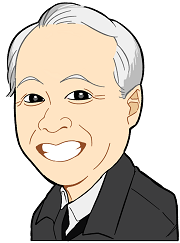
DXへの2つのアプローチ
私は次の2つのアプローチを推奨しています。
・イノベーション by DX
・KAIZEN for DX
前者はDXでイノベーションを起こそうという視点です。イノベーションとは「今までにない新たなものを創造し変革を起こすことで経済や社会に価値を生み出すこと」なので、DXとは相性がぴったりですが、イノベーションを起こすことはそう簡単なことではありません。ましてやメーカーであればまだしも、中小・中堅のサプライヤー企業にはかなり高いハードルとなりますが、まずはこちらの視点を簡単に解説します。
イノベーションという概念が生まれたのは古く、オーストリア・ハンガリー帝国(当時)出身の経済学者であるヨーゼフ・シュンペーターの5つの理論に由来します。その1つ目が「新しい財貨の生産:プロダクト・イノベーション」です。
プロダクト・イノベーションは長い歴史の中で数多存在します。最も身近な例を図1に示します。
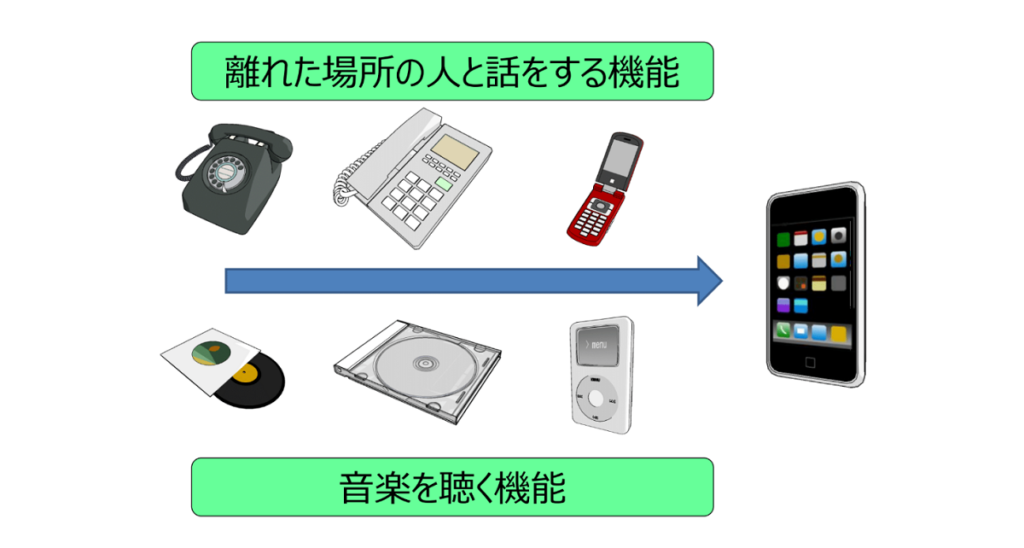
遠隔通話を目的とした電話は、アナログ式からプッシュホンを経て携帯電話、そしてスマートフォンに進化していきました。音楽を聴くための蓄音機は、レコードプレイヤーに変化し、CD、MDを経て、今では「コンテンツ」だけが残り、携帯デジタルプレイヤーからスマートフォンと合体しました。電話機の発明者アレクサンダー・グラハム・ベル氏、蓄音機の発明者トーマス・エジソン氏はその2つがスマートフォンなるものに統合されるとは夢にも思わなかったでしょう。
では、私たちはこれからどんなイノベーションを生み出していくのか? それにはDXの概念を利用することはもちろんですが、アナログ感性が最も重要なのです。
ヨーゼフ・シュンペーターの5つの理論の残り4つは「新しい生産方法の導入:プロセス・イノベーション」「新しい販売先の開拓:マーケット・イノベーション」「新しい供給源の獲得:サプライチェーン・イノベーション」「新しい組織の実現:オーガニゼーション・イノベーション」ですが、これらは改めて紹介することにしましょう。
KAIZEN for DX
さて、2つ目の「KAIZEN for DX」についてお話していきましょう。「KAIZEN」は、もちろん「改善」のことです。1980年代に日本の製造業の競争力が急激に向上した時に欧米をはじめ多くの国にその手法が伝わり、「KAIZEN」という英語の単語になったのです。柔道の用語が「IPPON!(一本!)」や「HAJIME!(はじめ!)」などそのまま外国語になったのと同じですね。
そもそも「改善」とは何でしょう。現状(As is)に対して、「こうありたい」「こうあるべし」(To be)という理想を描き、そのギャップを埋めるための活動をすることが改善です。ここで、図2をご覧ください。
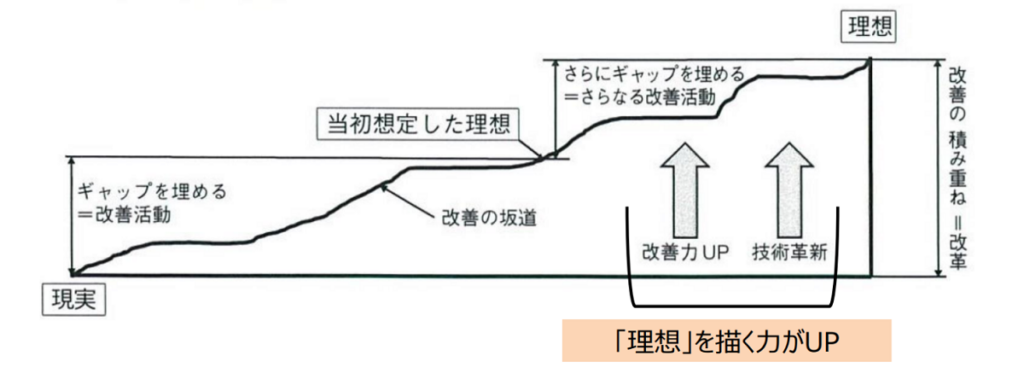
横軸の一番左が「現状」です。理想(改善目標)を描き、そこに向かって一歩一歩坂道を登っていくような地道な活動が改善なのです。活動開始時にはメンバーのモチベーションが高く、斜度の高い坂道を登り始めるのですが、途中で一息つき活動停滞、また力を振り絞って坂道を登り始めます。図の中央の「当初想定した理想」に3年かけて到達したとしましょう。さて、改善活動はそこで終わるのでしょうか? ……いや、終わらないのです。
国語辞典で調べてみてください。「理想」の反意語は「現実」ですよね。すなわち理想と現実は一緒になることは、日本語の意味からしてもあり得ないのです。「当初想定した理想」に到達した時点で何が起こっているのでしょうか? 世の中の技術は進化しています。そして3年間の活動を通じて皆さんの改善能力が向上している、すなわち「もっと先にあるべき姿があるよね」ということに気づく、つまり理想を描く能力が向上しているのです。現実と理想が一致しない限り改善活動には到達点はありません。トヨタの言うところの「改善に終わりなし」は日本語の意味からしても当然のことであるというわけです。
さて、図2の右端の「理想」に5年かけて到達したとしましょう。この高さが5年間で積み重ねた改善の成果です。私はこれこそが製造現場の「改革」だと考えています。製造現場において飛躍的改革が一気に起こることはまずありません。
しかし5年前に比較して、「ずいぶんきつい坂道を登ってきたけれども、現場が見違えるように変わったな!」と思ったならば――そう、それが改革なのです。
DXで改善をするのではなく、DXを実現するためにデジタル技術を使った改善をする。ですから私は「KAIZEN for DX」という言葉を使っているのです。
小さなお子様をお持ちの方はお分かりだと思いますが、毎日毎日見違えるほど大きくはなりません。「立った!」「喋った!」というイベントはあるでしょうが、日々の成長は大きくはない。ところが5年ぶりに会った親戚の子供はいきなり大きくなっています。お名前を失念してしまいましたが、何年か前に自動車メーカーのマツダの相談役が講演で「マツダは芋虫改革でいい。芋虫はちょっと見には動いているようには見えないが、10分も目を離していると着実に移動している。マツダの改革はそれでいいんだ。」とお話しされていました。まさに「KAIZEN for DX」と同じ考え方だと思います。
図2右端の高さを高くする、つまり改革のインパクトを大きくするには当然の坂道の平均斜度を上げるしかありません。もし平均斜度がゼロだったら5年たっても現状維持、そんな悲しい改善活動はあり得ませんよね。 次回からは、「KAIZEN for DX」の活動方法について、具体的に紹介してまいりましょう。
関連記事:【第1回】ものづくりDXを机上の空論にしない
関連記事:【第3回】トヨタ生産方式とDXは相性抜群! ― 作り過ぎのムダはデジタル技術で簡単解決
執筆者プロフィール
関ものづくり研究所代表。株式会社Fiot代表取締役。株式会社エコム社外取締役、株式会社桜井製作所社外取締役、国立静岡大学大学院客員教授。
ローランド ディー. ジーにて製造部長として勤務していた時代には、完全一人完結セル生産「デジタル屋台生産システム」を開発。その成果が新聞・雑誌やテレビ番組などで報道されて話題に。ミスミグループ本社では、製造子会社の駿河精機 本社工場長、生産改革室長、環境・品質推進室長を兼務し、業務改善を推進した。
自身の専門である機械工学および統計学を基盤として、品質向上を切り口に現場の改善を中心とした業務に携わる。ISO9001/14001マネジメントシステムにも精通し、経営に寄与するマネジメントシステムの構築に精力的に取り組み、その延長線上として労働安全衛生を含むリスクマネジメントシステムの構築にもかかわる。
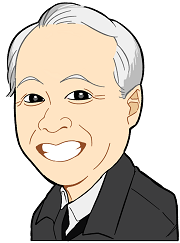