製造業におけるデータ活用は、ビジネスを加速化させるための重要な手段です。そして、DX(デジタルトランスフォーメーション)が進んでいる昨今では、データをうまく活用できなければ、業績の向上や業務効率化を果たせず、競争力が低下する恐れもあります。
しかし、一口にデータの活用と言っても、具体的なイメージを持つのは難しいかもしれません。そこで本記事では、データ活用による製造業のメリットやデータ活用の具体的な方法、進め方について紹介します。
製造業のデータ活用とは
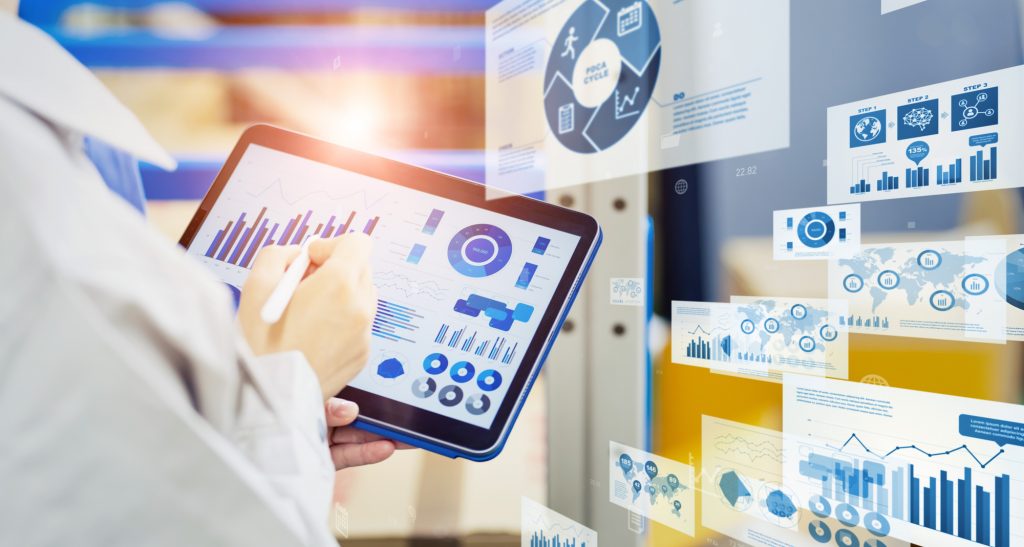
製造業におけるデータ活用とは、現場で生成される大量のデータを収集・解析し、生産性向上や品質改善などの具体的な施策に反映することです。具体的には、稼働中の装置から得られる情報や製造工程における各種データを分析し、現場の問題点を発見したり業務改善のために新たな視点を提供したりします。
データ活用のおもな目的は、IoT(Internet of Things)やAI技術を用いたスマートファクトリー化です。誰でも簡単にデータを活用できる環境を構築して、最小限の人数で効果を最大化することが期待されています。
また、多くのデータを収集することで、データドリブンな経営が可能です。データドリブンとは、企業がデータにもとづく意思決定をおこなうアプローチのことを指します。ただし、データの収集・解析・活用には専門知識が必要です。
製造業におけるデータ活用の課題
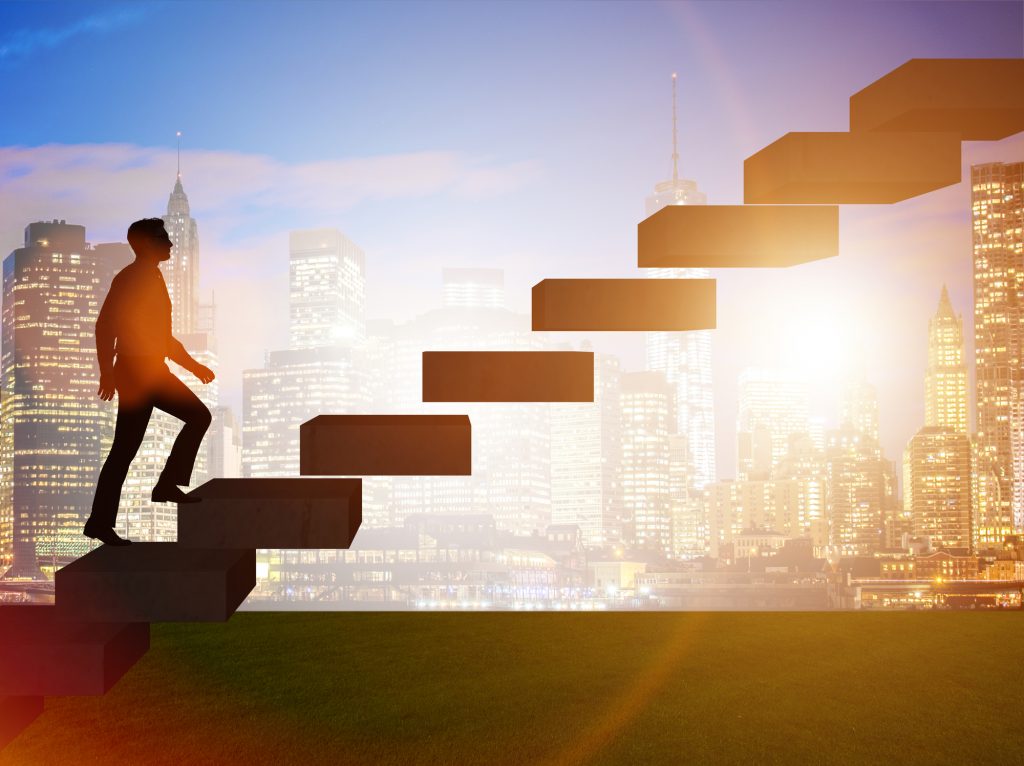
製造業におけるデータ活用の課題として、以下の4点があげられます。
- データ分析の知識・スキルを持つ人材が不足している
- 部署間で連携しづらい
- 装置が老朽化してデータの取得が困難
- 経営陣と現場で認識が異なる
製造業で使用する装置は、頻繁に買い換えるものではありません。そのため、古い装置が現役で稼働しているケースも多いでしょう。しかし、古い装置はWebやパソコンとの連携が難しく、簡単にデータの取得ができません。
装置そのものを買い換えられればベストですが、難しい場合はデジタル式の測定器を後付けしたりOCR(光学文字認識)を活用するといった方法でデータを取得する必要があります。
製造業でデータ活用をおこなう6つのメリット
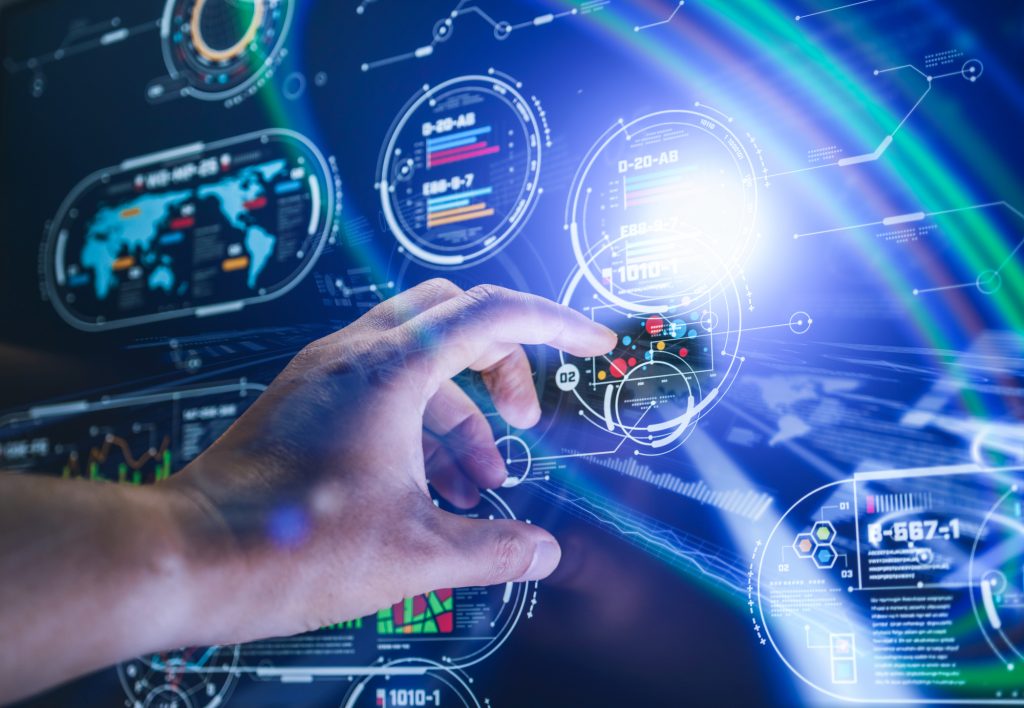
製造業でデータを活用することで、次のようなメリットがあります。
- 業務効率化による生産性の向上を図れる
- 品質改善によって顧客満足度向上につながる
- 意思決定が早くなり、業務が滞りづらい
- 製造プロセスを最適化でき、ムダなく装置を稼働できる
- 高精度な製造計画を立てて在庫の適正化を図れる
- ノウハウを共有し属人化を解消できる
メリット1:業務効率化による生産性の向上を図れる
製造業におけるデータ活用のメリットは、業務効率化による生産性の向上です。データを取得しない場合は、作業者の経験や勘で業務を進めなければなりません。その都度、悩む時間が発生するため、生産性は低くなりがちです。
しかし、データを活用すれば明確な基準を設けられるため、瞬時に正確な判断を下せます。すべての製造ラインをデータ化できれば、生産性を大きく向上することも夢ではありません。
メリット2:品質改善によって顧客満足度向上につながる
製造業におけるデータ活用のメリットとして、品質改善があげられます。製造中に発生したデータを活用することで、不良の原因や出現パターンを特定し、原因の解消が可能です。
たとえば、下記の表のように製造工程ごとの不良発生数とその原因を分析すると、対応すべきポイントが見えてきます。
工程 | 不良発生数 | おもな原因 |
A | 5 | 機械故障 |
B | 10 | 素材の不良 |
C | 3 | 作業員のミス |
品質の向上は、顧客満足度の向上につながります。製品の品質が保証されることで、顧客は安心してその製品を使用でき、結果としてリピート購入やブランドへの信頼性が高まります。
メリット3:意思決定が早くなり、業務が滞りづらい
製造業でのデータ活用は、迅速な意思決定につながります。製造現場で発生する各種データをリアルタイムで収集・分析することで、その場で最適な判断ができるのに加え、問題が発生した場合でも即座に対応できるため、業務の進行を防げません。
たとえば、特定の部品が頻繁に不良となる場合、部品自体の品質問題や組み立て工程の問題など、早期に改善点を見つけられます。
また、データにもとづく客観的な判断は人間の主観に左右されないため、一貫性のある意思決定が可能です。意思決定が早くなれば効率化や生産性向上に直結し、ビジネスの競争力を高める要素となります。
メリット4:製造プロセスを最適化でき、ムダなく装置を稼働できる
製造業におけるデータの活用は、ムダのない最適な製造プロセスに改善できます。製造ラインの各工程や装置の稼働状況をリアルタイムに把握、分析することでムダな動きや停滞時間を削減して効率化を図れるからです。
たとえば、下記のような装置の稼働率を考えてみましょう。
装置 | 稼働率 |
A | 95% |
B | 70% |
C | 90% |
このデータから装置Bが頻繁に待機状態になり、生産効率を下げる原因となっていることが読み取れます。データをもとに製造プロセスを見直すことで、全体の稼働率向上を見込めます。
メリット5:高精度な製造計画を立てて在庫の適正化を図れる
データ活用をおこなうことで、精度の高い製造計画の構築と在庫の適正化を図れます。過去のデータや需要データを分析すると、精度の高い製造計画を作成できます。
たとえば、需要予測を立てる際は、季節性や一過性のトレンドなどさまざまな要素を考慮しなければなりません。経験や勘のみで計画を立てるのではなく、データを活用することで信頼性の高い計画の立案が可能です。
その際は、AIや予測分析ツールを活用すると、より高精度な計画を設計できます。これにより、生産量と需要のバランスが取れ、生産過剰や生産不足の防止が可能です。
メリット6:ノウハウを共有し属人化を解消できる
製造業の現場では、特定の人にしか対応できない技術やノウハウが存在し、その人がいないと業務が進行しない「属人化」がしばしば発生します。しかし、データ活用によってノウハウを体系的に把握でき、共有することで属人化の解消が可能です。
たとえば、各作業工程や機器の操作履歴をデータ化し分析することで、誰でも再現できる作業手順や改善策を創出できます。
また、データ活用は、新人教育やスキルアップ教育にも有効です。データから明確な成功パターンや失敗パターンを示すことで効率的な学習ができ、全体の業務効率化を促進できます。
製造業における3つのデータ活用方法
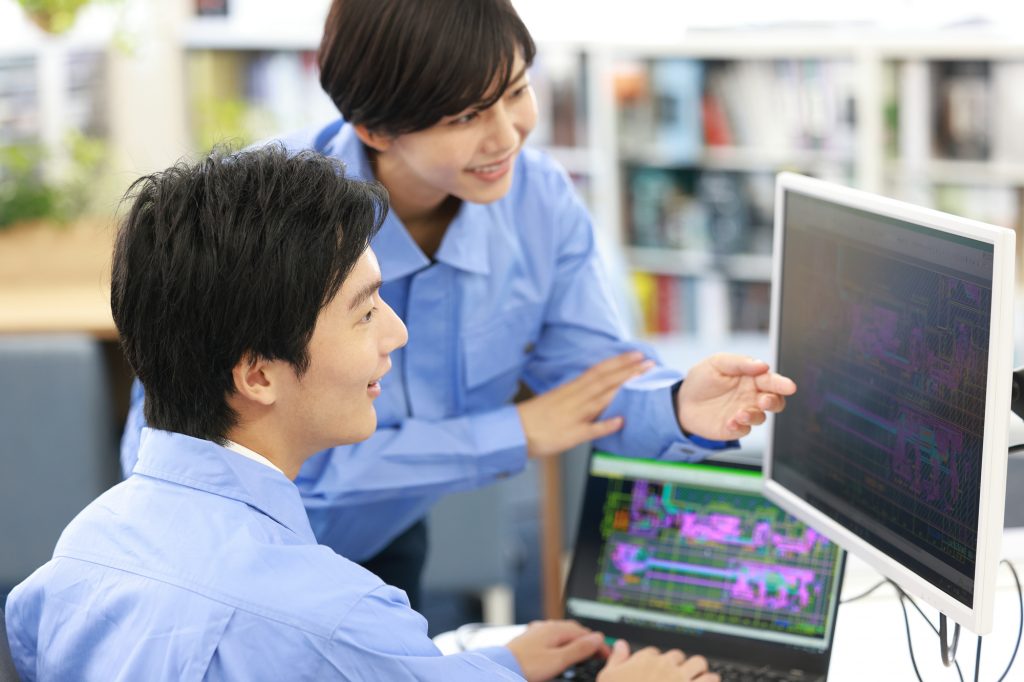
製造業におけるデータ活用方法として代表的なものが、次の3点です。
- 不良率の低減
- 装置保全
- 需要予測
特に需要予測に関しては、過去の販売データや市場動向データを活用し正確な予測を実現することで、生産計画の最適化や在庫コントロールにまでその効果が波及します。これら3つのメリットについて、順番に見ていきましょう。
方法1:不良率の低減
データ活用方法の1つに「不良率の低減」があります。製品に不良が発生している場合は、生産ラインのデータを活用して、不良の発生原因を特定しましょう。発生の原因を特定して対策すれば、不良率の低減につながります。
たとえば、特定の曜日に不良率が高い場合は、その曜日の共通点を洗い出すことがデータ活用の第一歩です。仮に、作業者が曜日で固定されているとすれば、その曜日を担当する作業者のやり方に問題があるかもしれません。その作業者にヒアリングすることで、解決の糸口をつかめる可能性があります。
方法2:装置保全
「装置保全」もデータ活用がもたらす恩恵の1つです。装置保全とは、装置の故障や性能低下を早期に発見・修復することで、長期的な生産性を保つための重要な取り組みです。具体的には、IoTを活用し、製造装置から得られる各種データをリアルタイムで収集します。
収集したデータを分析し、異常値の発生やパターンを早期に把握することで予防保全を行い、装置のダウンタイムを最小限にできます。このようにデータを装置保全に活用することで、製造ライン全体の生産効率改善が見込めるでしょう。
方法3:需要予測
需要予測とは、過去の売上データや市場動向、季節変動などのデータを分析して将来の商品需要を予測することです。売上の要因となるデータを分析し正確な需要予測をすることで、過剰在庫や在庫切れを防ぎ、効率的な生産を実現します。
近年では、AIを活用した需要予測が注目を浴びています。人による需要予測では気づけないポイントを発見することもあり、人よりも精度の高い予測が可能です。AIによる需要予測は下記の記事で紹介しているので、需要予測の精度を上げたいとお考えの方はぜひご覧ください。
関連記事:AIを活用した需要予測とは?メリット・デメリットや活用事例も紹介
製造業におけるデータ活用の進め方4ステップ
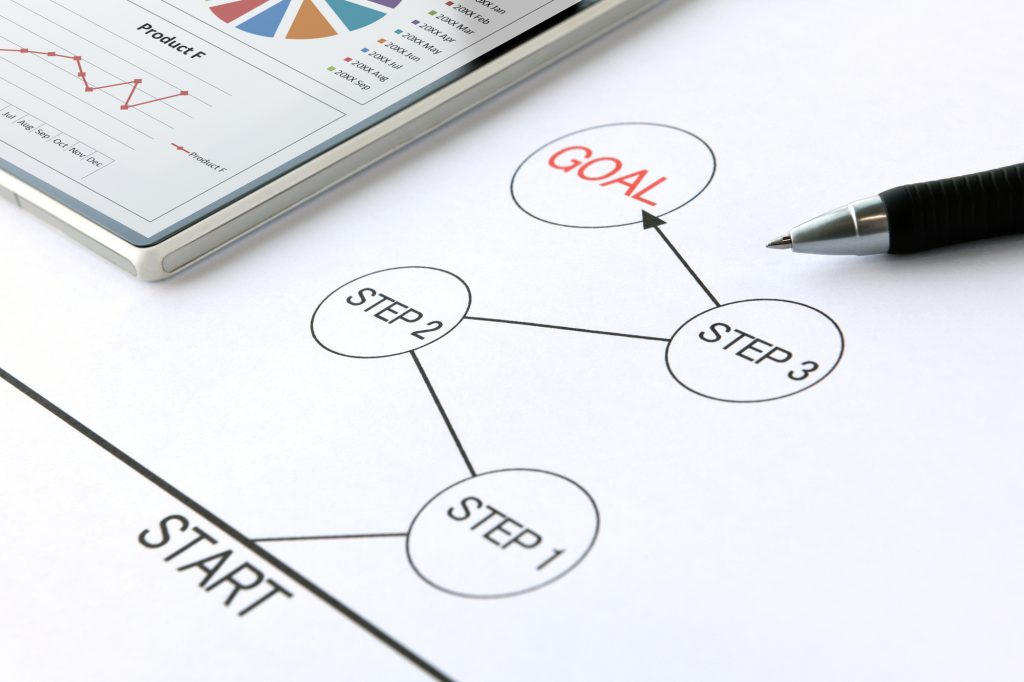
製造業におけるデータ活用の進め方は、下記の4ステップで進行できます。
- 現状を把握し、課題を洗い出す
- 必要なデータを取得する
- 取得したデータを分析する
- データをもとに施策を打ち出す
ステップ1:現状を把握し、課題を洗い出す
データ活用を進めるためには、現状の製造プロセスや業務フローを詳細に把握しなければなりません。正確に把握することで、問題点や改善の必要性が明確になります。
具体的に把握すべき内容としては、下記の例があげられます。
- 製造ラインの動線
- 各工程での生産量と時間
- 不良品発生率とその原因
- 生産設備の稼働率
- 人員配置と作業効率
これらの情報をもとに、製造現場の課題を具体的に洗い出しましょう。具体的には「生産設備のダウンタイムが長い」「特定工程の不良率が高い」「必要な部品が不足し生産が滞る」などが考えられます。
ステップ2:必要なデータを取得する
解決したい問題や改善したい点が明らかになれば、解決に必要なデータを取得します。いきなり多くのデータを取得するのは難しいため、必要な種類や範囲を定めることが重要です。
たとえば、製造ラインの効率化を目指すならば、
- 製品の生産量
- 生産時間
などを詳細に把握しなければなりません。また、不良率の削減を狙う場合は、不良品の発生頻度や原因、製品の詳細な仕様などが重要です。
データの取得方法には、自動化システムを使ってリアルタイムで収集する方法や、定期的に手動で集計する方法などがあります。従業員の負担軽減や品質向上を考慮して、RPAやAIを活用するのがおすすめです。
データの取得は、次のステップであるデータ分析の基盤となります。そのため、できる限り正確、かつリアルタイムな収集が重要です。
ステップ3:取得したデータを分析する
データを十分に取得できれば、集めたデータの質を確認します。データに抜けや誤りがないか、または意味をなさないデータが含まれていないかを確認することが重要です。もし、抜け漏れや意味のないデータが含まれていると分析結果に悪影響を与えかねません。
データを整理できれば、下記のような方法で分析します。
- クロス集計:異なるカテゴリ間の関係を表形式でまとめる分析
- ロジスティック回帰分析:二値の結果を予測するための統計手法
- クラスター分析:似た特徴を持つデータをグループに分ける手法
- 因子分析:相関が高い変数群を少数の因子で表現する手法
- 時系列分析:時間の経過とともに収集されるデータの分析
正しいデータを使い、目的に応じて適切な分析方法を選択することが課題解決のポイントです。
ステップ4:データをもとに施策を打ち出す
分析したデータをもとに、具体的な改善策を考えましょう。製品の品質向上や生産効率の改善など、具体的な目標に対するアクションプランとなります。
目標 | 施策 |
不良率の低減 | 原因となる工程を特定し改善作業を実施 |
装置の保全 | メンテナンス周期の見直しや、部品交換の最適化 |
需要予測の精度向上 | 予測モデルの改善やデータの見直し |
製造業におけるデータ活用はビジネスを加速させる

製造業におけるデータ活用は、ビジネスを加速化させる重要な戦略です。適切にデータを収集し分析することで、業務効率の向上や生産コスト削減、製品の品質向上につながります。
データ分析はAIやRPAなどを活用して自動化すると、さらに効果的です。ビジネスの競争力を維持し強化するための戦略として、データ活用とそれに伴うデジタル技術の導入をぜひ検討してみてください。