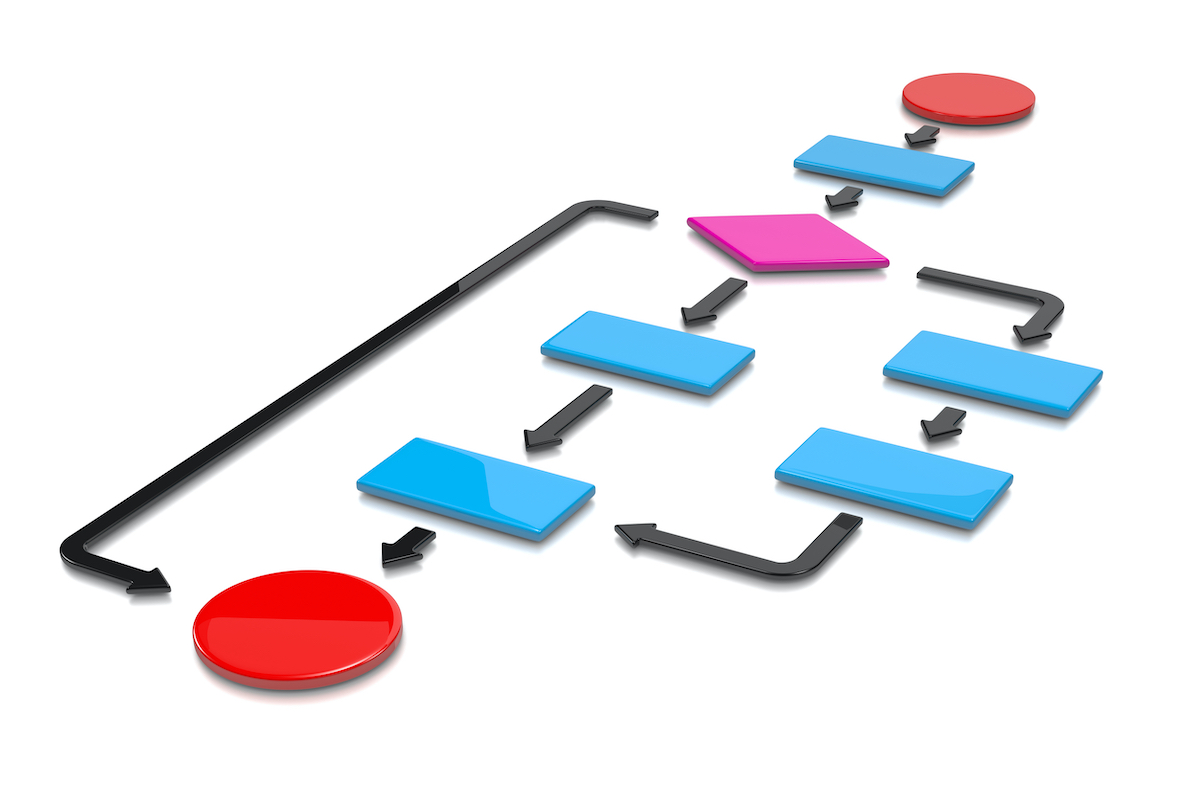
製造業は「製品完成」という目標の達成と、「納期」という期限の遵守が求められる場面が多く、進捗管理が重要な業種と言えるでしょう。
プロジェクトには数多の作業工程が含まれ、これらを整理して進捗管理まで行うのは困難です。
そこで、方法論として作業設計から進捗管理を一挙に担える「アローダイアグラム」という図を使うのがおすすめです。
今回は、新QC7つ道具のひとつとして数えられるアローダイアグラムについて、概要や類似手法との違い、作成時のルールから図から読み取れる情報まで解説します。
アローダイアグラム(PERT図)とは?
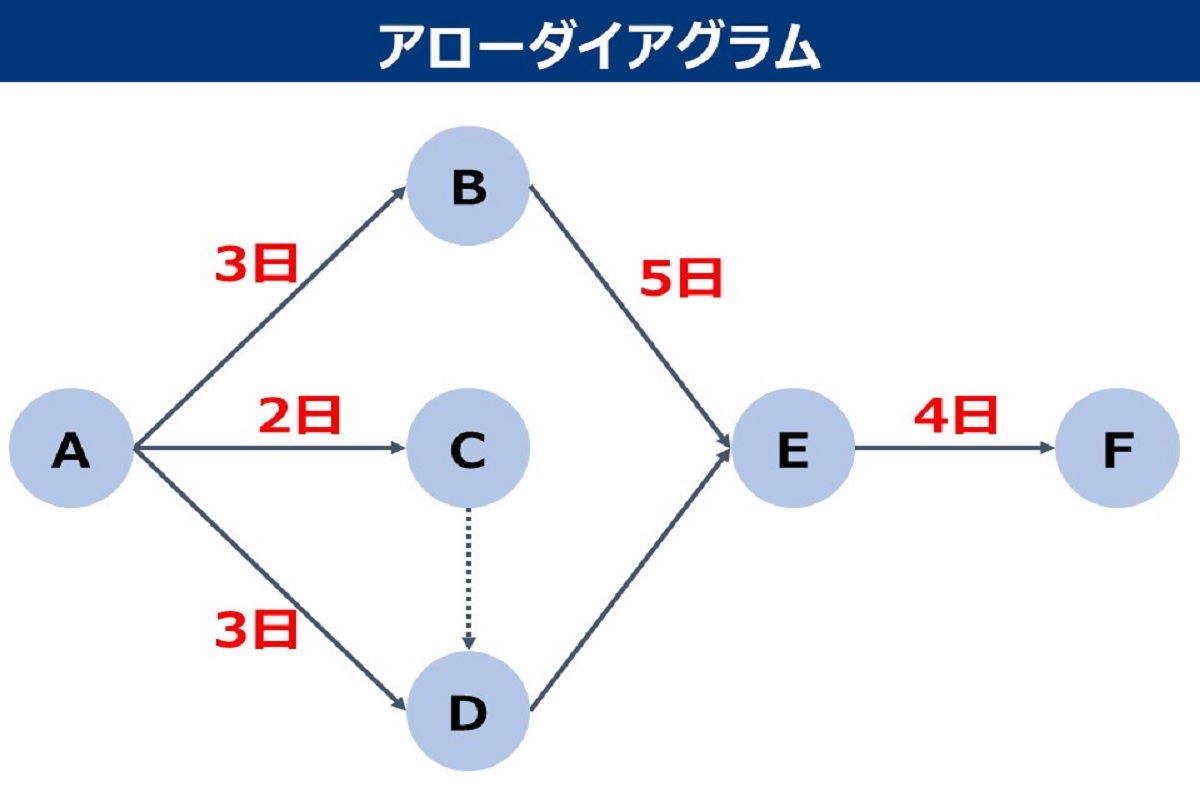
アローダイアグラムとは、複数の独立した作業や工程が連続して実施される際に、作業の日程計画を図形と数字で表現するためのフローチャート図です。海外では一般的に「PERT(Program Evaluation and Review Technique)図」と呼ばれます。
主な図の構成要素は、作業の数だけ存在する丸印「結合点」と、丸印から丸印へと伸びる矢印「作業」そして矢印の上部に付記する「作業日数」の3点です。
例えば、「A」という工程を3日経て「B」という次の工程に進めるとすると、結合点Aから結合点Bへ矢印を伸ばし、その矢印の上部に「3日」と記載する書き方となります。
必要な作業の順序をルートとして表現できるため、各作業の関連や日程上の前後関係を明確にできるメリットがあります。
すなわち、調達から納品までに膨大な作業が発生する製造業では、アローダイアグラムは大いに役立つでしょう。
ガントチャートとの違い
アローダイアグラムは、図の整理によって問題を改善する方法「新QC7つ道具」のひとつです。
作業と時間の関係を表すという意味でアローダイアグラムと混同しやすいのが、同じく新QC7つ道具のひとつである「ガントチャート」です。
ガントチャートは、横軸に時間、縦軸にメンバーや作業内容を並べ、工程や作業ごとに開始日から完了日の情報を帯状グラフで表す図です。
プロジェクトの全体像を可視化し、一覧として共有できるメリットがあります。
アローダイアグラムと異なり、作業同士の関連を表現するのは苦手なため、小規模な工程のマネジメントとして活用するのが一般的です。
関連記事:新QC7つ道具とは?従来の7つ道具との違いや各道具を解説
アローダイアグラムの書き方
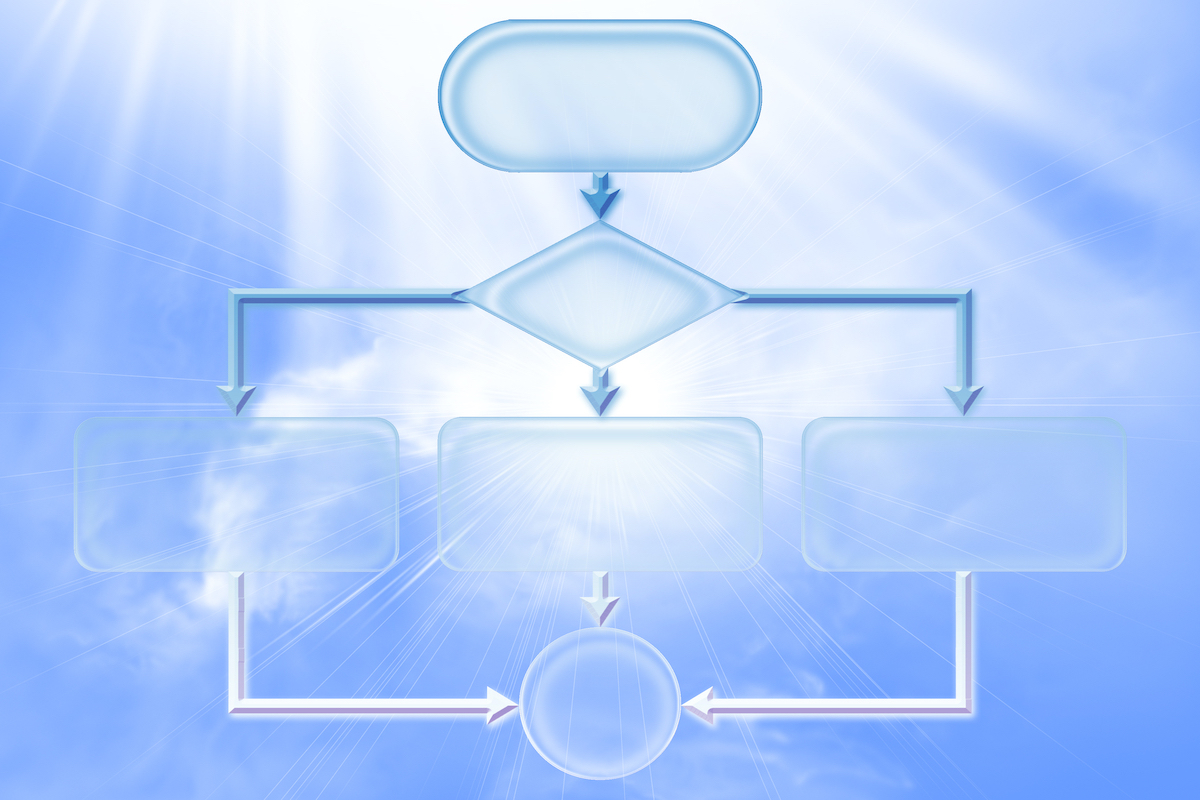
アローダイアグラムは、基本的に前工程の結合点から後工程の結合点に向けて矢印を引いていく単純な構造ですが、実際に作成する上で押さえておくべきルールがあります。
- 各作業の矢印は、必ず前後で結合点と繋がっている
- スタートとゴールの結合点を除いて、結合点は必ず作業の矢印と繋がっている
- 結合点に付与する番号もしくはアルファベットは、作業の方向なりに大きくなる
- 結合点は、そこから出て再びその結合点に戻る作業経路を持ってはならない
- ある結合点から伸びる作業は、その結合点へ向かう事前作業がすべて終わっていないと取り掛かれない
- 並行作業がある場合は結合点を増設し、点線矢印によってダミー作業を設ける
以下のように、みそ汁を作る際のアローグラムを作成する場合、以上のルールを守っていることがわかります。また、ルール6の通り、並列作業は点線矢印でダミー作業を表しています。
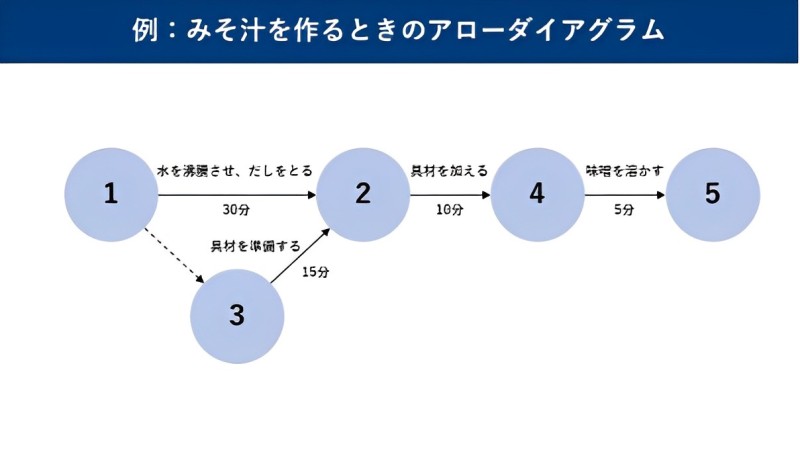
前半3点のルールは比較的理解しやすいですが、後半3点については少しわかりづらいため、以下に補足を加えます。
ルール4.作業の戻し経路は禁止
結合点から出ていった作業がもう一度同じ結合点に戻るのは、時間が巻き戻っているか、手戻りが起きているのと同じです。
いずれも日程計画に織り込む情報としては不適切であるため、戻り経路は禁止されています。
ルール5.事前の作業が終わってから次の作業に取り掛かる
ルール5が適用される状況例としては、ふたつの結合点A・Bから後続のCへ向かってそれぞれ作業が伸びており、Cからもその先へ作業が伸びるという構図が挙げられます。
ここでAからの作業に2日、Bからの作業に5日要する場合、少なくとも5日待たなければCから始まる作業には取り掛かれません。
ルール6.並行作業がある場合は結合点を増やす
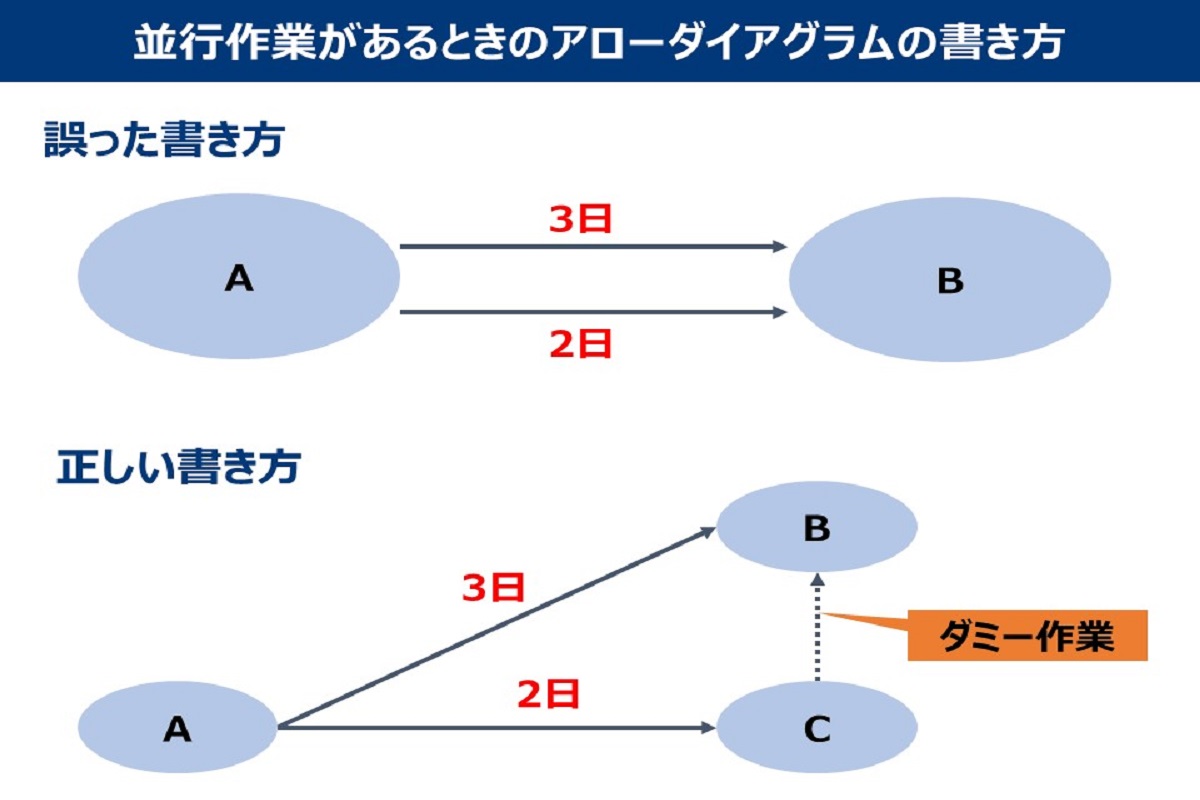
ルール6で想定されるのは、例えば結合点Aから結合点Bにかけ、それぞれ所要時間の異なる作業が2本並行して伸びるような状況です。
このままだと各作業の順序が不明瞭となるため、アローダイアグラムとして適切ではありません。結合点と結合点の間にかかる作業は1本に整理する必要があります。
並行して作業がある場合は、「ダミー作業」という点線を用います。なお、ダミー作業は実際の作業ではないので、所要時間は0です。
まず、並行する作業の中で所要時間が長い方を結合点Bとつなげ、もう一方の作業は一旦取り外してください。
次に、結合点Bの真下に結合点Cを新設し、先ほど取り外した作業を結合点AからCへとつなげましょう。
最後に、結合点Cから真上の結合点Bへ向かって点線矢印を伸ばし、これをダミー作業として表現したら完了です。
アローダイアグラムの読み方
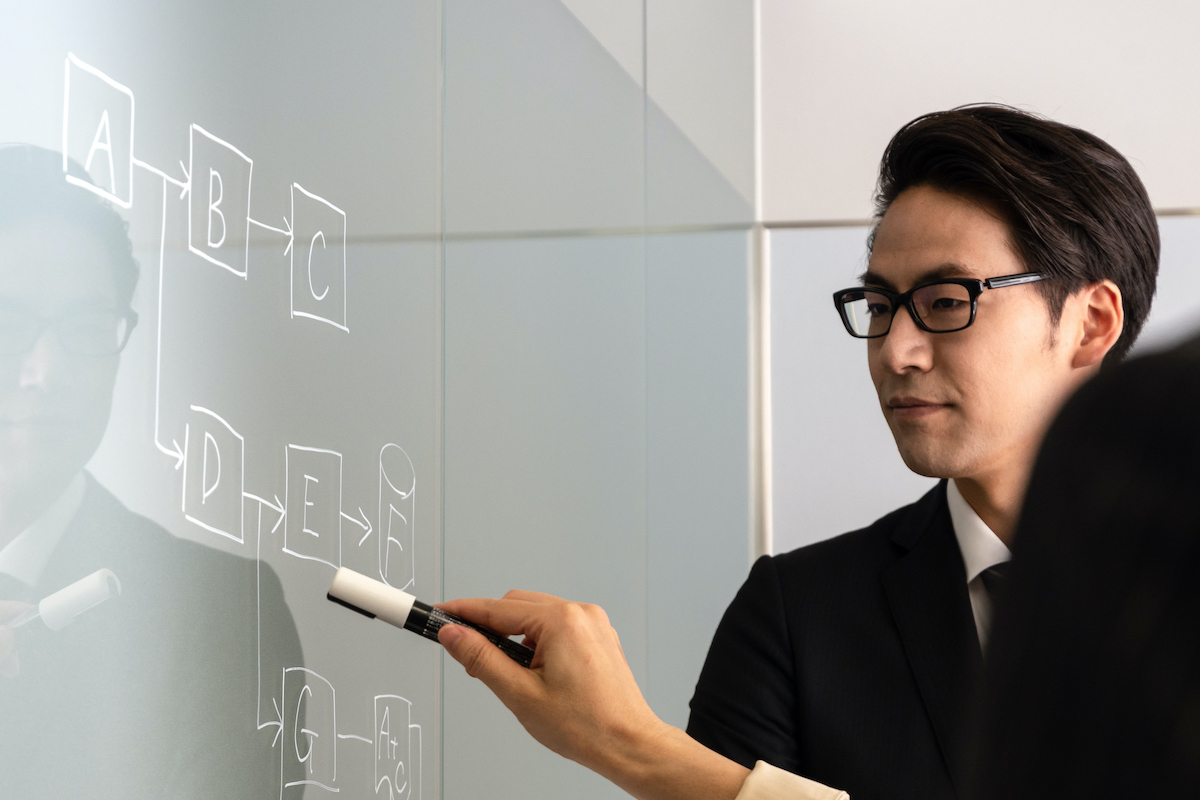
アローダイアグラムを描画するのは比較的容易ですが、重要なのはアローダイアグラムから読み取れる情報の正確な理解です。そこで、アローダイアグラムで読み解ける内容を解説します。
最早結合点時刻
最早結合点時刻とは、ある作業について計画上最も早く開始できる時点です。最早結合点時刻は、まずプロジェクトの開始日をスタート地点に設定し、それ以降の全結合点について以下の式で求められます。
最早結合点時刻=ひとつ前の結合点における最早結合点時刻 + 作業の所要時間
例えば、結合点の最早結合点時刻が4月1日として、次の結合部までの作業に3日を要する場合、結合点Bの最早結合点時刻は4月4日となります。
最遅結合点時刻
最遅結合点時刻とは、計画上最も遅い作業開始時点であり、この時点より作業開始が遅れてはならない最後のタイミング(デッドライン)でもあります。
最早結合点時刻は、プロジェクトの納期をゴール地点に設定し、それ以前の全結合点について以下の式で求められます。
最遅結合点時刻=ひとつ先の結合点における最遅結合点時刻 – 作業の所要時間
例えば、結合点Zの最遅結合点時刻が3月31日として、前の結合点からの作業に5日を要する場合、結合点Yの最遅結合点時刻は3月25日となります。
つまり、最早結合点時刻と異なり、デッドラインから逆算するような計算です。
余裕日数
余裕日数とは、各結合点において作業開始までに与えられる時間的余裕です。つまり、「ある作業の締め切りまでに何日残っているか」という指標になります。
余裕日数の計算式は以下の通りです。
余裕日数=最遅結合点時刻 – 最早結合点時刻
例えば、結合点Xの最遅結合点時刻が7月10日で、最早結合点時刻が7月5日の場合、余裕日数は5日です。
余裕日数が大きいほどプロジェクト進捗全体に余裕があり、逆に余裕日数が小さいとタイトなスケジュールであることがわかります。
クリティカルパス
クリティカルパスとは、アローダイアグラム全体を見渡したとき、スタート地点からゴール地点まで最も長く所要時間がかかる作業経路です。
クリティカルパスに含まれる工程に遅れが生じると、プロジェクト全体が遅れてしまうため、事前にクリティカルパスを特定し、早期の対策を講じておく必要があります。
クリティカルパスを特定するためには、各結合点までに必要な作業日数の最大値をスタートから順に記録していきます。
特に作業経路が分岐する場合、各分岐先で最も所要時間の長い作業を見つけてマーキングするとスムーズです。
アローダイアグラムでプロジェクトを効率よく達成
アローダイアグラムは、プロジェクトにおける作業工程の設計図であり、作業順序を明確化するフローチャート図でもあります。
製造業の供給プロセス(サプライチェーン)には納期を遵守しなければならない工程が多いため、進捗管理におけるアローダイアグラムの採用は非常に効果的です。
事前の作業設計にはじまり、プロジェクト開始後もアローダイアグラムから得られる情報をもとにした軌道修正を行うなど、効率よく最短で目標を達成できるようなマネジメントを心がけましょう。
関連記事:新QC7つ道具とは?従来の7つ道具との違いや各道具を解説
関連記事:サプライチェーンマネジメント(SCM)とは?メリットや課題点を解説
補足:他の新QC7つ道具もチェック
今回はアローダイアグラムについて解説しました。新QC7つ道具には目的達成のために最適な手段や方法をツリー状に並べる「系統図法」、原因と結果、目的と手段などが複雑に絡み合った問題の因果関係を論理的につなぐ「連関図法」、問題となる要因を親和性の高いグループに分けて整理する「親和図法」など他の手法もあります。ぜひ全ての新QC7つ道具を覚えて課題解決に役立てましょう。
関連記事:新QC7つ道具のひとつ、連関図法とは?活用して現場改善を徹底