前回は、「KAIZEN for DX」のお話をしました。デジタル技術を利用した改善を積み重ねることで製造現場のDXを実現しようという考え方です。今回からはその具体的な方法をお話ししていきましょう。
(執筆:関伸一/関ものづくり研究所)
記事一覧:【連載】関伸一の「ものづくりDX研究所」
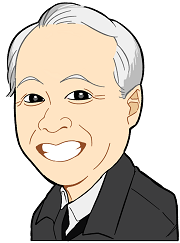
トヨタ生産方式とは
言わずと知れたトヨタ生産方式(以下TPS:TOYOTA Production System)ですが、読者の皆さんはその本質をご存じでしょうか? このコラムをお読みの方には失礼な問いかけかもしれませんが、図1を使って筆者なりの理解をお示ししましょう。
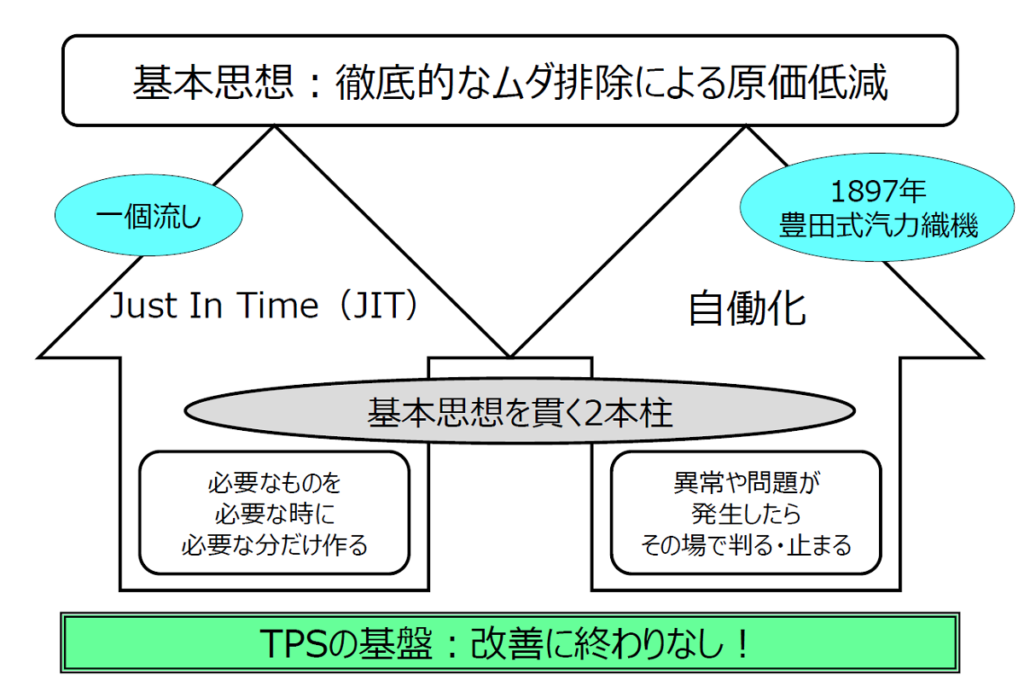
TPSの基本思想は徹底的なムダ排除による原価低減です。その基本思想を支える二本柱が「必要なものを必要な時に必要な分だけ作る(買う)=JIT : Just in Time」と「異常や問題が発生したらその場で判る・止まる=自働化(にんべんのついた自動化)」です。JITの究極の姿は1個流しです(これについては今後詳しく解説をします)。自働化はかの有名な豊田式汽力織機で、横糸が切れたら自動停止する仕組みになっています。130年前に「不良品を作り続けない」ことが実現されているのです。
皆さんの現場では「あれ? プレスの金型に異物が入って、不良品が数百個もできちゃった……」なんてことになっていませんか? 残念ながら、いまだにそんなことになっている現場を筆者はいくつも知っています。
時にTPSは次のような批判を浴びることがあります。「TOYOTAは在庫を持たないけれど、それはサプライヤーに持たせているだけだ」という論調ですがこれは違います。サプライヤーもJITをすればいいだけの話です。また、「原価低減」に対して「TOYOTAばかりがもうかって、サプライヤーは赤字だ」という論調ですが、もし本当にそうであればTOYOTAの仕事を続けていればそのサプライヤーは倒産します。確かにアイテムによっては逆ザヤのものもあるかもしれませんが、トータルで利益が出ているからこそTOYOTAの仕事をしているのでしょうし、それこそ自社での原価低減をすればよい話です。「批判する前に自らの襟を正せ!」ですね。
TPS「7つのムダ」
TPSの基本思想は「徹底的なムダ排除による原価低減」です。そして排除すべき「ムダ」についても明確に定義されています。図2をご覧ください。
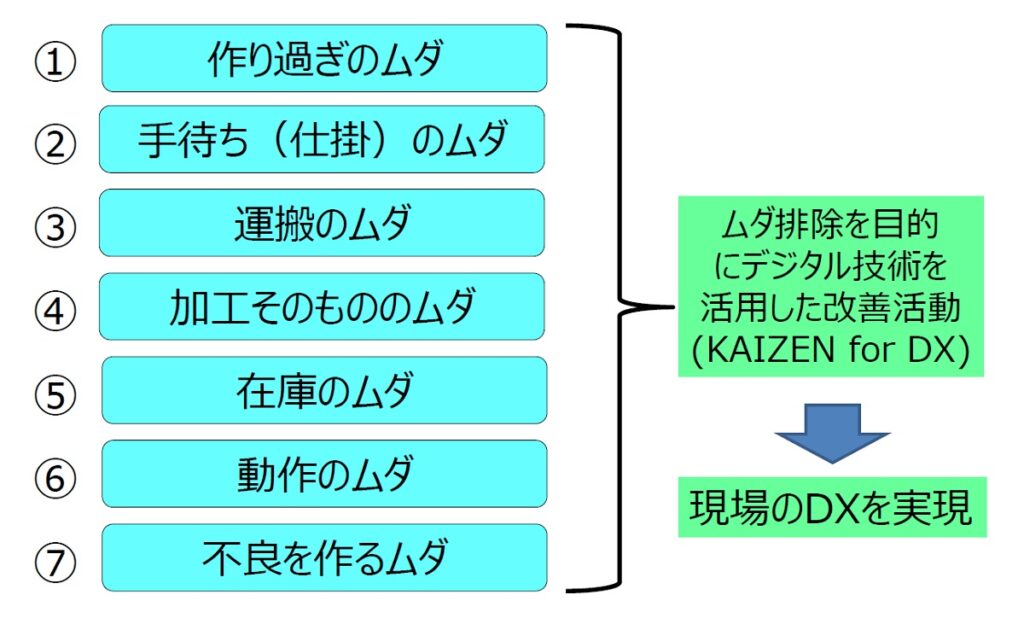
左側に並んでいるのが「TPS7つのムダ」です。これらのムダ排除を目的とした改善活動について、デジタル技術を活用して推進し、現場のDXを実現する。これが筆者の言うところの「KAIZEN for DX」なのです。
作り過ぎのムダへのアプローチ
では7つのムダへのアプローチを順に解説していきましょう。そのうちの「1」の「作り過ぎのムダ」は筆者がとても嫌いなムダです。このムダに対応できていない現場は数えきれません。いや、対応できている現場は少数派なのではないでしょうか。そもそもこれをムダとして認識していないと思われる現場も数多く見てきています。
例えば、順送型による金属連続プレス現場です。材料(圧延加工された薄板金属でロール状)が供給され、まずはレベラーという機械で板を平らにし、その後プレス機に装着された金型で打ち抜きや塑性変形をさせて徐々に製品に仕上げ、箱に落下させるという完全自動生産になります(図3)。
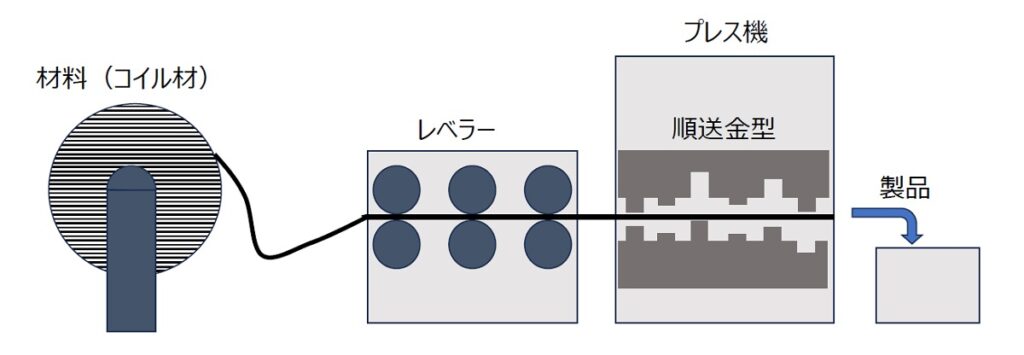
プレス機の動作回数は自動でカウントされるので、例えば750個の注文があれば750個で生産を止めればいいのですが、「材料がなくなるまで作っちゃおう」としてしまう現場が実に多いのです。
理由を尋ねると、以下のような言葉が返ってきます。括弧( )の中は、筆者の心の声です。
- 何個か不良が出た時に困るから(対策して不良が出ないようにしましょうよ)
- どうせまた注文が来るから(本当に来るのですか?来たとしても今回余った数より10個だけ多かったらどうしますか?半年後に注文が来たら製品在庫がすぐ見つかりますか?)
このような理由は、筆者には言い訳にしか聞こえないのです。
製品にしてしまったらその在庫管理が必要になります。自動車部品関連メーカーなら数十、いや数百種類の製品を製造していることでしょう。その在庫管理をするよりも余った材料(例:1.2mm SPCC=冷間圧延鋼板)の在庫管理の方が明らかに簡単です。
そんな言い訳をする経営者や工場長に、筆者はこう答えます。
「良かったですね、貴社が生鮮食品業じゃなくって。もしそうなら製品在庫全部腐りますからね」
それでは、どうすればよいのでしょうか? 答えは簡単です。
- 正しい材料をセットする(バーコードなどで間違い防止)
- 正しい金型をセットする(これもバーコード利用)
- 製品になったら自動検査(画像検査が理想的)
- NG品は自動的に不良品BOXへ
- 光電センサーなどでOK品のみをカウント
- 750個になったらプレス機を自動停止
これだけで作り過ぎのムダがなくなり、製品在庫管理のムダもなくなるのです。画像解析による自動検査には少々費用が掛かりそうですが、採用している企業は多くありコストダウンも進んでいます。プレス機に振動センサーや熱センサーを付けて正常に稼働していることを担保することで検査の代用とすることも可能です。
以上でお分かりのように「作り過ぎのムダ」はデジタル技術を活用することで簡単に改善することができるのです。次回は手作業の「作り過ぎのムダ」についてお話ししましょう。
記事一覧:【連載】関伸一の「ものづくりDX研究所」
執筆者プロフィール
関ものづくり研究所代表。株式会社Fiot代表取締役。株式会社エコム社外取締役、株式会社桜井製作所社外取締役、国立静岡大学大学院客員教授。
ローランド ディー. ジーにて製造部長として勤務していた時代には、完全一人完結セル生産「デジタル屋台生産システム」を開発。その成果が新聞・雑誌やテレビ番組などで報道されて話題に。ミスミグループ本社では、製造子会社の駿河精機 本社工場長、生産改革室長、環境・品質推進室長を兼務し、業務改善を推進した。
自身の専門である機械工学および統計学を基盤として、品質向上を切り口に現場の改善を中心とした業務に携わる。ISO9001/14001マネジメントシステムにも精通し、経営に寄与するマネジメントシステムの構築に精力的に取り組み、その延長線上として労働安全衛生を含むリスクマネジメントシステムの構築にもかかわる。
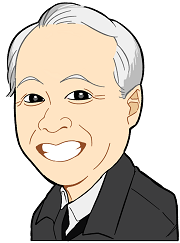