目次
製造業における品質検査の目的は、一定の品質基準に満たない製品を市場に流出させないことです。しかし製品の検査に時間をかけすぎると、工場全体の生産性を下げることにもつながりかねません。
そこで本記事では、生産性と検査精度を向上させつつ、品質検査の自動化を行う手法として注目されている画像検査のメリットやデメリット、実施のポイントについて解説します。
関連記事:品質検査とは?品質管理や品質保証との違い、効率化の方法について
画像検査とは
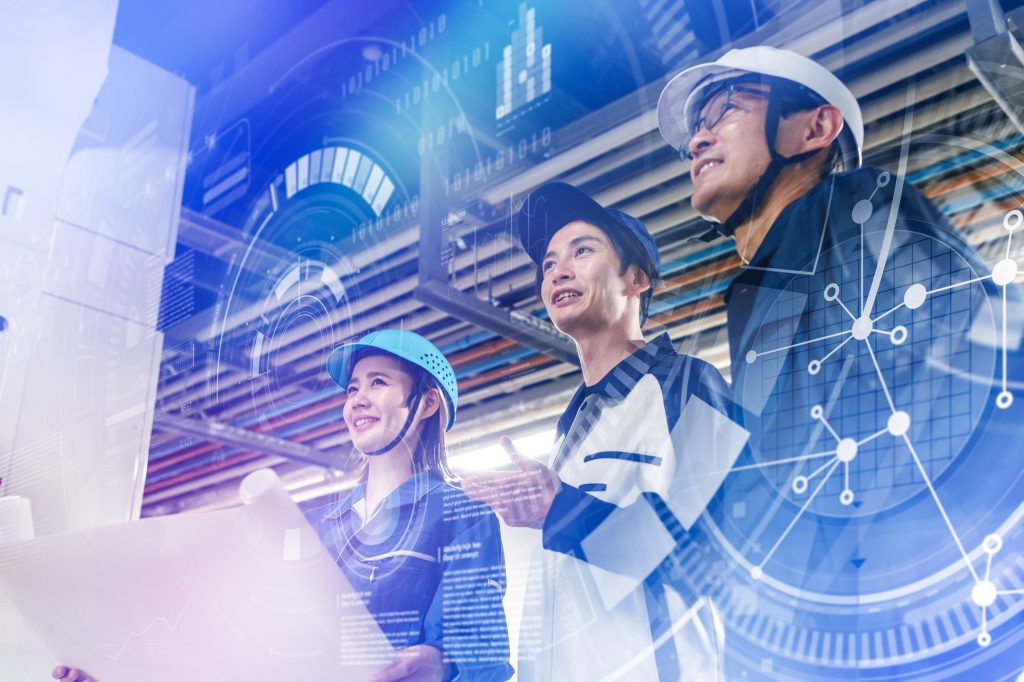
画像検査とは「製品本体を検査者の肉眼で目視する」従来の目視検査とは異なり、デジタル技術を用いて製品画像をデータ化し、自動的に対象物のキズなどを検知することで、良品と不良品を判断する検査手法です。検査を行う人物の主観が入らず、高い水準で安定した製品を検査でき、外観検査を自動化するための手法として注目されています。
画像検査の種類
画像検査の方法は、大きく2種類に分けられ、それぞれ特徴や得意とする領域が異なります。
2次元画像検査
2次元画像検査は、一方向から撮影された2次元的な画像をもとに検査を行う方法です。一般的な産業用カメラを使用できることから、コストを重視した画像検査の導入に向いています。また、比較的広い範囲の画像データが撮影できることから、検査対象が広範囲に及ぶ場合にも適しています。
しかし、検査のもととなる画像データが2次元であることから、高さや奥行きが関係する判断は苦手です。検査の判定基準を厳格にすることによって、2次元画像検査の弱点をある程度カバーできる場合もありますが、判定基準を厳格にしすぎると良品を不良品と判断するケースが増えてしまいます。
3D画像検査
3D画像検査とは、検査対象を平面的に捉えるのではなく、さまざまな角度から習得した3次元的な画像データをもとに検査を行う方法です。3次元データを取り込むことで、製品の形や大きさを正確に計測し、キズやへこみ、異物などをより正確に検出できます。
信頼性が高い3D画像検査ですが、2次元画像検査に比べると、システムが複雑になる点や、一度に検査できる範囲が限られるなどの弱点も存在します。そのため、どのような検査方法が最適なのか、製品の種類や求められる精度によって異なることを理解しておきましょう。
画像検査装置の仕組みと原理
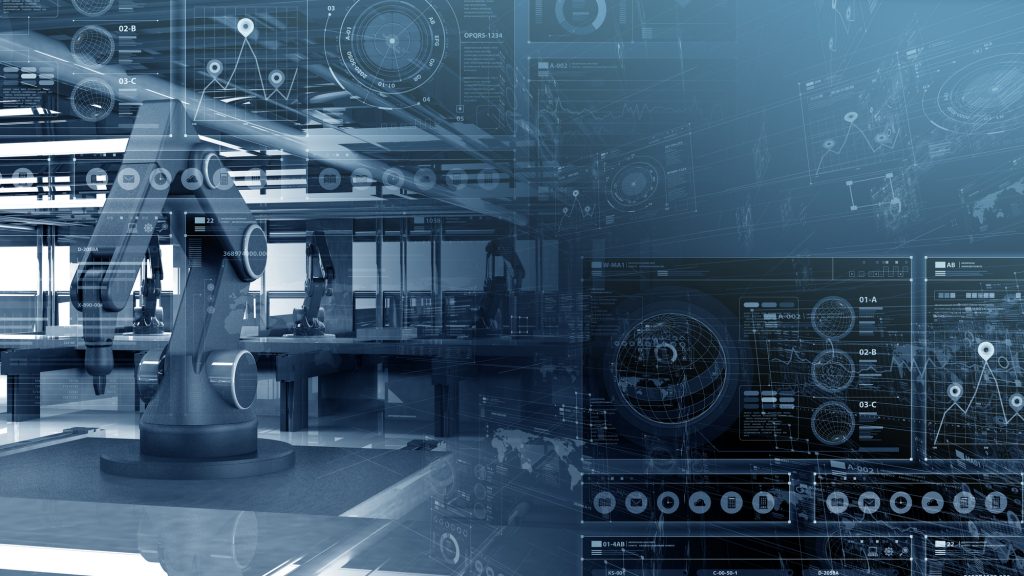
画像検査装置の仕組みは、カメラや照明などのハードウェアと、画像処理や解析を行うシステムによって実施されます。それぞれの工程で、どのような作業が行われているのか、順番に解説していきます。
画像データの取得
画像検査の最初に行われる工程が、カメラやイメージセンサーを用いた画像データの習得です。対象となる製品の形状や、検出したい異常の種類によって適した撮影方法が異なります。
たとえば、箱状のものと薄いシート状のものでは、画像検出に使用する方法が異なります。また、同じ箱状のものでも、検査対象が表面のキズなのか、はんだ付けや溶接の乱れなのか、印字の不良なのかによっても、画像検出の方法を使い分けなければなりません。
画像処理
カメラやイメージセンサーで習得した画像データを、システムが解析しやすい形へと変換します。たとえば、取り込んだ画像から背景の除去やノイズを取り除き、製品の輪郭を強調したものが、付着しているバリなどを検出しやすい画像です。
また、通常の画像から色の成分を除去し、グレースケールへ変換することで、陰影が強調され、製品のキズが発見しやすくなるなど、画像処理のパターンも製品や検出したい異常の種類によって異なります。
関連記事:画像解析/画像認識とは?仕組みやAIとの関係、活用事例を解説!
不良品の判別
適切な形に処理した画像から、不良品の判別に必要な情報を読み取ります。良品/不良品の分類は、キズや汚れなどの特徴を判別できるようなアルゴリズムを事前に設定したうえで行います。
アルゴリズムは画像検査を行ううえで極めて重要です。アルゴリズムの設定が甘ければ不良品が流出する可能性が高まる一方で、厳しくしすぎると歩留まりが多くなってしまうため、継続的な調整やチューニングが求められます。
不良品の除外
アルゴリズムにもとづいて不良品と判別された製品を人の手、あるいはコンベアやロボットなどによって自動で取り除きます。
人の手で除外を行う場合は、さまざまな製品や製造ラインにフレキシブルに対応できる一方で、判断ミスや生産性の低下が懸念されます。コンベアやロボットが自動で行う場合は、画像検査に連動して、自動的に不良品を除外できますが、設備の導入コストやシステム連携といった要素を加味しなければならない点は押さえておきましょう。
AIによる画像検査の進化
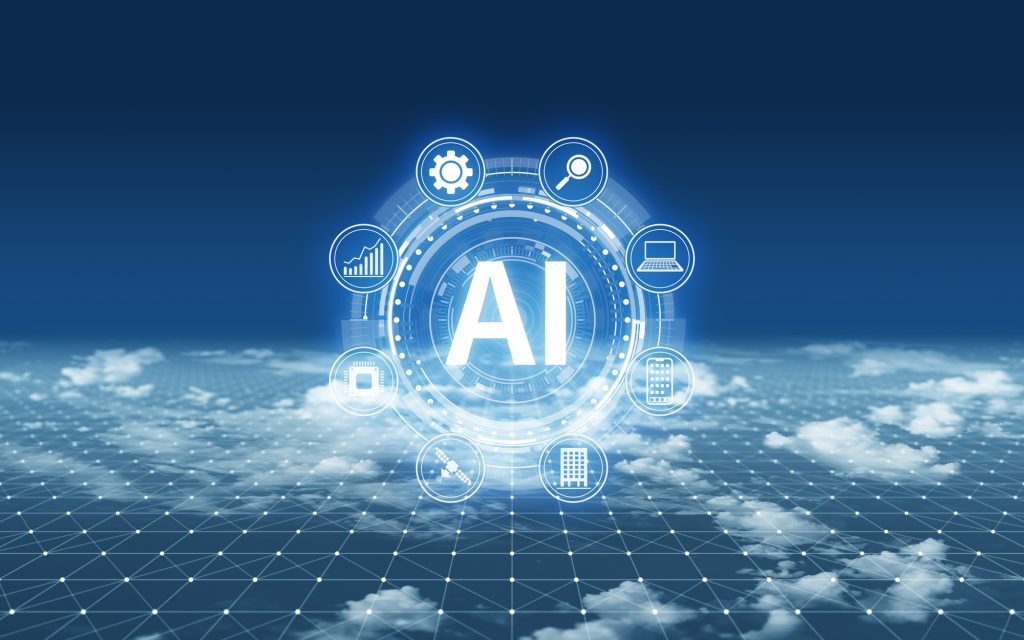
画像検査により正確かつ効率的な品質検査を実現できますが、近年では画像検査にAIを導入することで、飛躍的な速度の向上を目指す動きがあります。
画像検査とディープラーニングの関係
従来の画像検査は、事前に設定していた検査ルールにもとづいて良品や不良品の判断をシステムが行います。このようなルールベース型と呼ばれる画像検査モデルは、部分的な異常であれば非常に高い精度での検出が期待できる一方、人の手によるルールの調整や見直しを欠かすことはできません。
しかしAIに大量の製品画像を学習させることで、自ら不良品の判定基準を発見し、それにもとづいた判断とルールの自動的な最適化が可能となります。事前に指定されていたルールでは発見できなかった異常を検出できる可能性があり、従来の画像検査には必須となっている、アルゴリズムの設定が必要ありません。これはすなわち、人間が備えている「判断な柔軟さ」をシステムで再現できると言い換えられるでしょう。
画像検査による自動化のメリット・デメリット
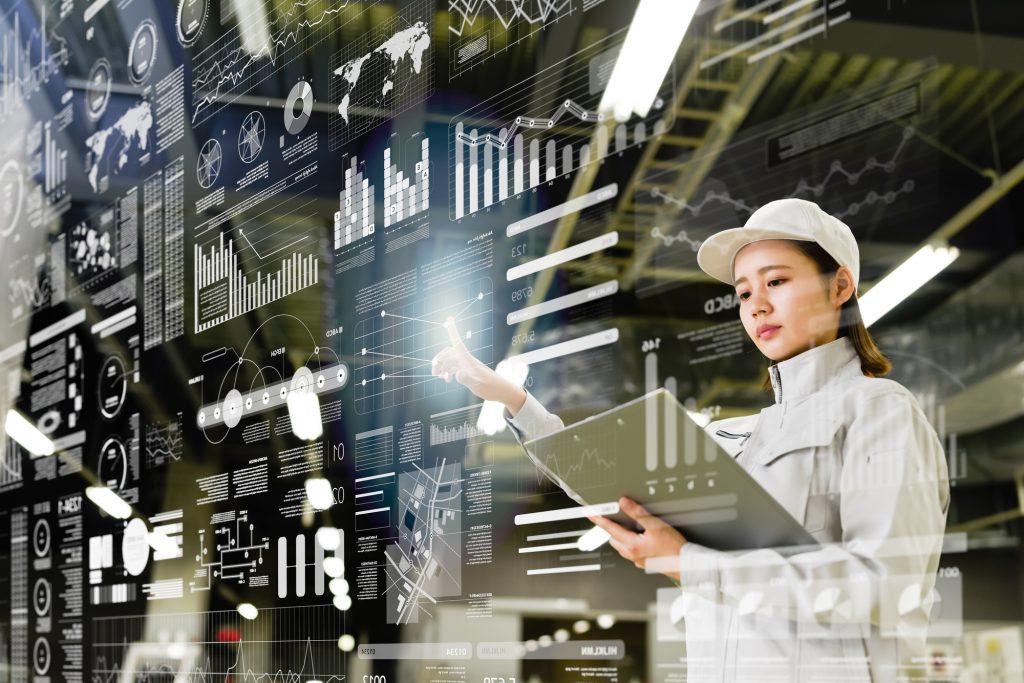
画像検査の導入によってさまざまなメリットが期待できる一方、デメリットも少なからず存在します。それぞれについて詳しく見ていきましょう。
メリット
検査工数の削減
肉体的・精神的に負荷の大きい目視検査を自動化することで、検査工数を減らし、人的負担を軽減できます。とりわけ、品質管理において重要でありながら大きな負担となる「全数検査」を自動化できる点は見逃せません。
また、生産量には余力があるものの、検査へのリソースが割けないために、出荷数量が頭打ちとなっているケースもあるでしょう。画像検査の導入によって、検査のスピードが大幅に向上すれば、頭打ちとなっていた生産量を増やすことも可能です。
検査精度の向上
一定の基準にもとづいて判断を行う画像検査では、検査精度の大幅な向上が期待できます。なぜなら、肉眼では見落としてしまうようなキズや異常でも、画像検査なら高い精度で検知できるためです。
また、肉眼による外観検査では人によって検査基準がぶれてしまう一方、画像検査であればそのような基準のばらつきを排除できる点もメリットです。
検査データの蓄積と活用
検査にて習得したデータの蓄積によって、さらなる検査精度の向上が見込める点も画像検査のメリットでしょう。過去の検査データを分析することで、どのような不良品が多かったのかのパターンがわかります。不良品が発生するパターンがわかれば、重点的に画像検査を行う箇所が絞れ、より高い精度で不良品が発見できますし、発生パターンからその原因となる作業工程を発見し、対策を行うといった形でもデータを活用できます。
デメリット
導入にコストが必要
画像検査の導入には、イニシャルコストが発生します。検査機器に加えソフトウェアなど、画像検査の導入に必要なものは少なくありません。また、インラインで画像検査を行いたいのであれば、製造ラインの設計から見直す必要が生じます。
とはいえ、イニシャルコストの発生はどのようなシステムにおいても同様です。画像検査の導入によって大幅に生産性が上がり、早期にコストを回収できる見込みがあれば、ぜひ導入を検討すべきでしょう。
検査の完全な自動化はできない
画像検査を用いたとしても、検査工程において完全に人の手を無くすことはできません。画像検査は高い検査精度を誇る一方で、ハードウェアやシステムの不具合によって、不良品を見逃す可能性があるためです。このような不具合を防ぐためにも、画像検査設備のメンテナンスといった工数が新たに発生します。
また、画像検査は熟練した検査者の触覚や聴覚を用いた官能検査の代替はできない点も注意が必要です。
画像検査のポイント
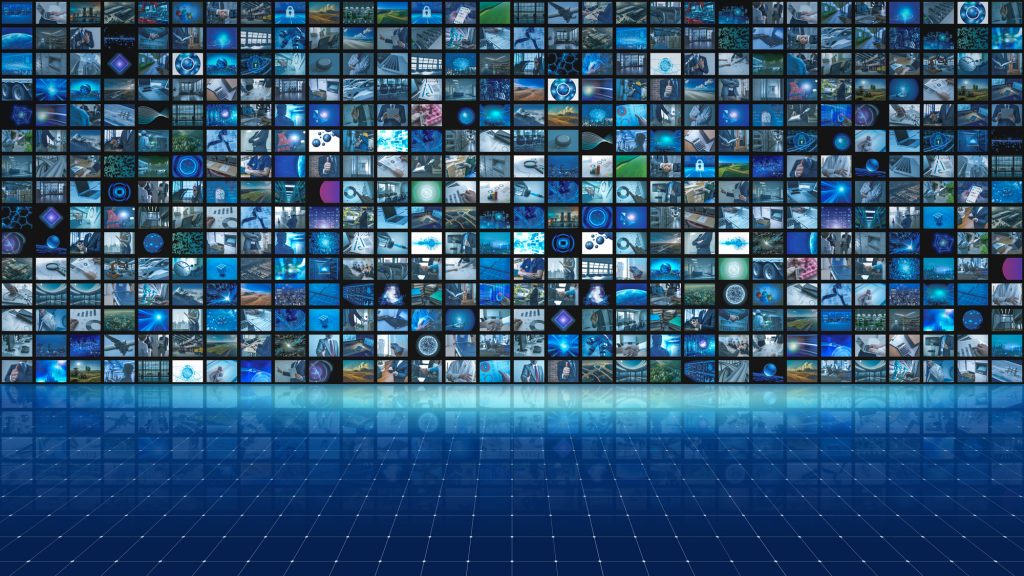
それでは最後に、画像検査の導入や実施におけるポイントについて解説します。これらのポイントは実際の事例から学べる部分もあるため、画像検査を含む画像解析の事例をまとめた下記の記事を併せてご覧ください。
関連記事:製造業において画像解析/画像認識技術を活用している企業7社の事例
自社製品に合った手法やシステムの選択
一口に画像検査と言ってもさまざまな手法やシステムが存在します。ハードウェア、ソフトウェアそれぞれの異なる特徴があるため、導入の際は自社の製品や製造設備に加え、検査の目的に応じたシステムを選択しましょう。
たとえば、金属製品のバリを検出したい場合と、パッケージの印字のかすれを検出したい場合では、画像検査の手法は大きく異なります。適切なシステムや手法を選択しないと、コストばかりが膨らんでしまい、不良品の検出精度も期待できません。
適切な照明の当て方・種類を選ぶ
画像検査を行ううえで、カメラ以上に重要となり得るのが照明です。照明の当て方によって取得できる画像の特性が変化するため、製品の形状や検査方法によって適切な証明の当て方が異なります。
また、照明の種類も重要です。対象物に対して、検査内容がしっかりと判別できる照明機器を選定する必要があるため、検査機器やシステムを提供するパートナーの知見を借りつつ検討を進めるのが良いでしょう。
基板など高度な検査に活用できるAOI(光学自動検査)
電子基板などの製造に際し、非常に複雑かつ高度な画像検査が必要なケースには、AOI(工学自動検査)の活用が有効です。AOIとは自動化された光学検査を指し、紫外線や赤外線などの異なる光源を持った高解像度のカメラシステムで対象物を連続して撮影し、画像処理を経て検査結果を示します。
基盤や実装基板の欠陥は、従来の目視による外観検査での発見が難しく、時間もかかっていました。しかし、AOIを適切に導入すれば検査精度の向上に加え、大幅なスピードアップが期待できます。
定期的なメンテナンス
画像検査において常に高い精度を維持するためには、検査機器の定期的なメンテナンスが必要です。対象の製品に異常がなくとも、カメラ側の汚れや傷に加え、製品を輸送するコンベアの振動による検査精度の低下が起こり得ます。
ハードウェアのメンテナンスの他、画像検査の判断が本当に適切なのかを検証することもメンテナンスに含まれるでしょう。サンプルを用いた検査精度の測定を定期的に実施し、検査制度が維持できているのかどうかを確認する必要があります。
大幅な検査の効率化を期待できる画像検査
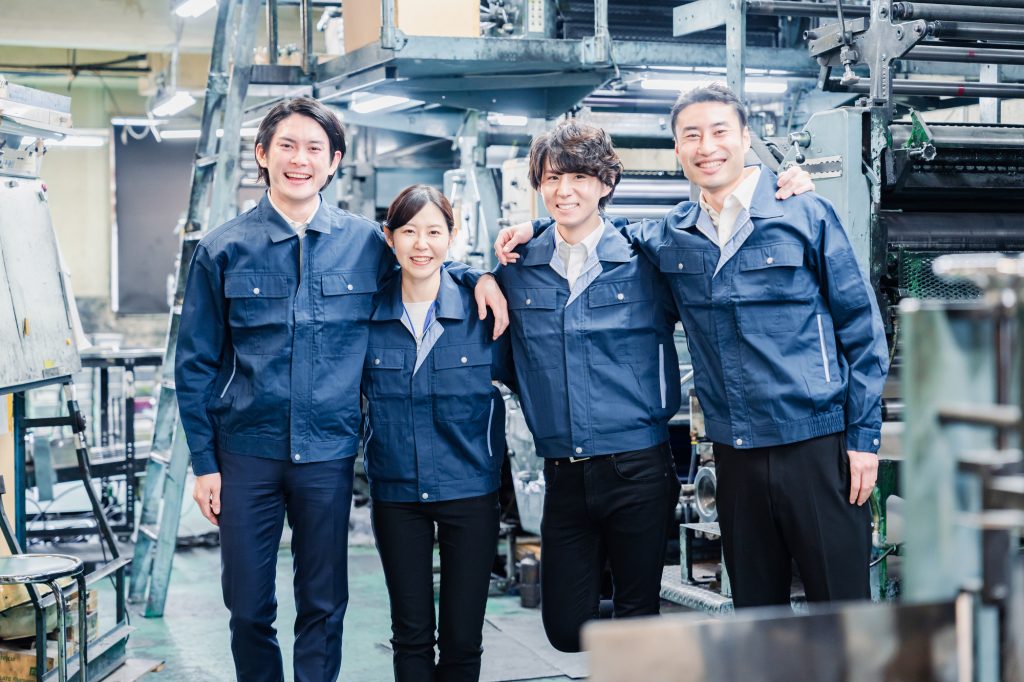
品質検査の効率化と精度向上を目指すうえで画像検査、とりわけAIを組み合わせ検査システムの導入によるメリットは計り知れません。しかしながら画像検査は、画像処理やアルゴリズムによる判断といった専門性の高い仕組みのもとで機能する以上、導入に際しては画像検査の知識と自社製品、そして製造工程に対する理解が不必要不可欠です。
これらを理解しないまま進めると、検査の精度が維持できないだけでなく、無用なコストを掛けることにもつながりかねません。本格的な画像検査の導入に際しては、専門の会社と連携しつつ進めるのが良いでしょう。