製造業において必要不可欠といえる品質検査は、製品の不良率や生産性に大きく影響する一方で検査員の肉体的・精神的な負担が大きく、業界内でも効率化が必要と考えられている業務のひとつです。
その一方で、効率を追求するあまり製品の品質が落ちてしまえば、顧客満足度が大幅に低下するリスクが考えられるため、そのバランスに頭を悩ませている企業も多いでしょう。
本記事では品質検査にかかる時間やコストに悩んでいる方、品質検査の効率化を考えている方に向けて、品質管理の一端を担う品質検査におけるポイントと、効率化の方法について具体的に解説します。
製造業における品質検査とは

品質検査とは、その言葉通り製品や部品の品質を検査することを指し、大きく分けて「外観検査」と「機能検査」の2種類があります。
外観検査は、製品や部品におけるキズや汚れ、へこみ、欠けなど外見上の欠陥の有無を確認する作業です。検査員が肉眼で確認する目視検査が主流ですが、近年はカメラや画像センサー、画像処理システムなどを利用した自動検査を導入する会社も増えています。
機能検査は、製品や部品が仕様に沿って動作するかどうかを確認する作業です。製品や部品の使用が想定される環境下だけでなく、気温や湿度、気圧などさまざまな条件を変更したうえでどこまで正常に動作するかをチェックする負荷検査なども併せて行われます。
品質検査を行う目的の中で最も重要なのが不良品の削減と品質の保証です。不良品をできる限り減らすことで顧客満足度を高めるだけでなく、不良品を検出し、その原因を追求することで、原因が生じた工程に対し適切なフィードバックや対策を実施することができます。
品質検査と品質保証・品質管理との違い
品質検査と似た言葉に「品質保証」と「品質管理」があります。これらはそれぞれ対象となる業務範囲や責任範囲が異なるため、詳しく説明しておきましょう。
品質保証は、商品や部品の品質を維持・保証するために行われる品質検査に対して、納品後も納品先やエンドユーザーの満足を保証する「買い手視点の活動」を指して使われています。製品企画から原材料の選定、製造、販売、カスタマーサービスまでほぼ全ての部門がその対象となることが特徴で、品質検査で不備があった場合に担当部署へフィードバックを行うことで、原因究明、問題解決に努め、顧客満足度の向上を実現します。
一方で品質管理は、あくまでも製造工程において品質を維持向上するための「売り手視点の活動」です。原材料や製品、部品の品質検査も品質管理作業のひとつであり、商品が完成するまでに不具合が生じた場合は品質管理部門が責任を負うことになります。品質管理を徹底することが品質保証につながりますが、品質管理には材料や製品の管理だけでなく、カスタマーサポートや返品交換などの対応まで含まれることを理解しておきましょう。
製造工程における品質検査の種類
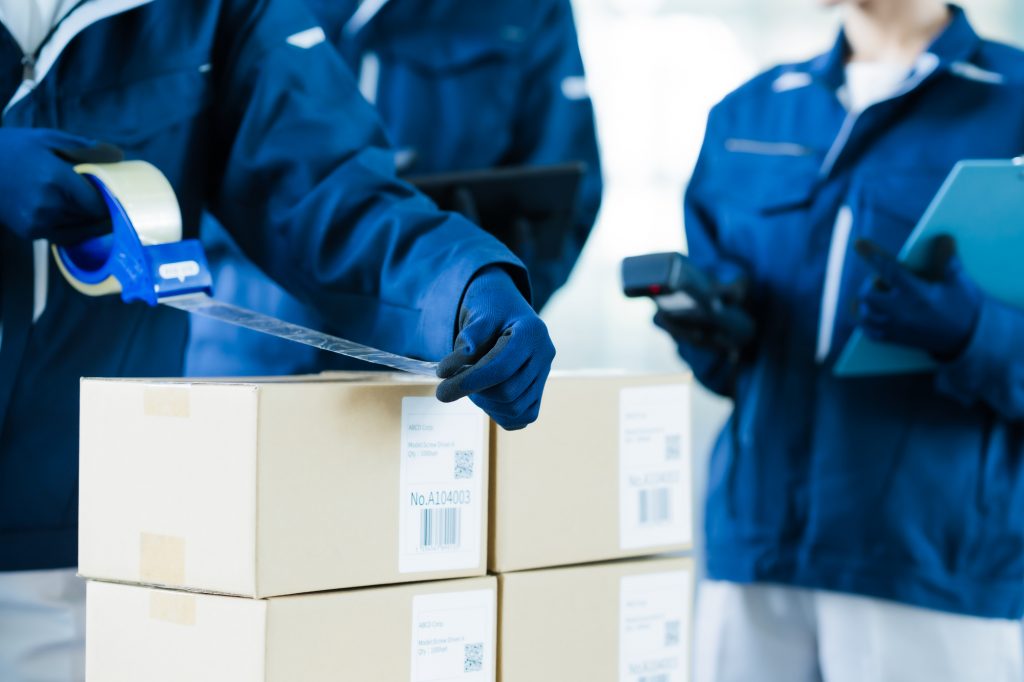
製造工程のなかで行われる品質検査には、主に「受入検査」「工程検査」「最終検査」の3つの検査があります。
受入検査
製品を製造するための原材料や資材が届いた際、はじめに行われるのが受入検査です。いくら製造準備が整っていても、原材料や資材に不具合があっては、製造物にも問題が生じます。そのため受入検査では、仕入れた材料が事前に定めておいた品質基準に達しているかを確認します。
受入検査は、すべての材料を確認する「全数検査」か、納入された材料の一部をランダムに選び出して確認する「抜き取り検査」のいずれかを目視で行うのが一般的です。品質を第一に考えると、確実に不良品を取り除くことができる全数検査を実施するのが理想ですが、実際は時間とコスト面の問題から抜き取り検査が主流となっています。
この段階でできる限り不良品を排除しておかないと、後工程で大きなトラブルが発生する可能性があります。裏を返せば、適切な受入検査の実施が生産ラインの効率的な稼働や製品の品質向上に直結するため、受入検査は品質管理において非常に重要な役割を担っているといえるでしょう。
工程検査
実際に製品を生産する段階になって行われるのが工程検査です。生産ラインをいくつかの段階に分け、完成していない状態の製品を段階ごとに抜き出してチェックします。「工程内検査」や「中間検査」とも呼ばれ、不良品の完成を事前に防止することで材料や部品の無駄を減らすことに加えて、不具合が発生した工程を早期に特定し、適切な対策がとれるといったメリットもあります。
工程検査では検査のタイミングに応じて、外観検査や機能検査をより細分化した検査を行います。具体的には、異物混入の有無を調べる「異物検査」、内容量を調べる「充填量検査」、ラベルの印刷ミスや不具合を調べる「印刷表示検査」などがあげられ、特に化粧品や医薬部外品を扱う場合には、これらに加え「バルク検査」が行われます。
バルク(bulk)とは、本来大きさや容量のことを指す英単語ですが、化粧品や医薬部外品の製造過程においては「個別容器に充填する前の中身」のことを指します。バルク検査では、外観の確認だけでなく、pHや粘度、比重など物理的な性質を計測する「物性試験」、微生物による汚染の有無を調べる「微生物試験」など、さまざまな角度からバルクが品質基準を満たしているかどうかを検査され、合格したバルクのみが充填工程に進む仕組みです。
最終検査
工程検査を無事に通過し、完成した製品のチェックを行うのが最終検査です。納品先やエンドユーザーに不良品が届いてしまうトラブルを防ぐことが目的で、顧客の手元に届く前の最終チェックであることから「出荷検査」とも呼ばれています。
生産数が少ない限定商品などの場合は全数検査をすることもありますが、基本的にはランダムに選出して抜き取り検査を行います。方法としては、目視による外観検査が中心で、あらかじめ用意した標準見本や、良品・不良品を見極めるために用意した限度見本などと比較して完成品の出荷可否を判断します。見落としがあったり、検査精度にばらつきが出たりしないよう、最低でも2〜3人の検査員で行うのが一般的です。
品質検査を効率化する方法
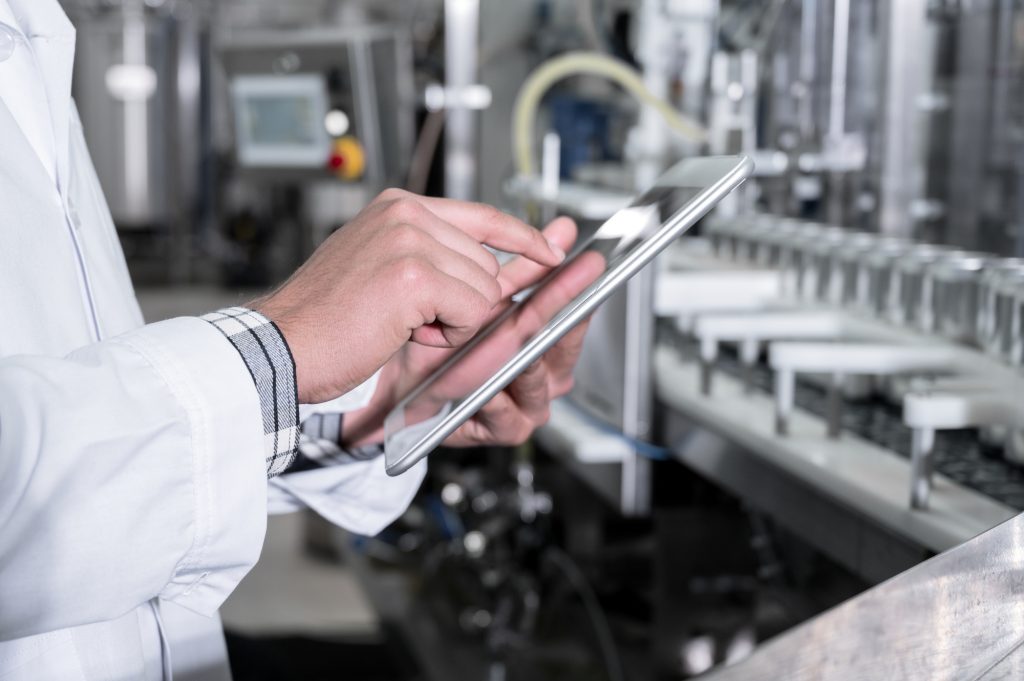
複数のタイミングで、何種類にもわたって実施される品質検査ですが、それゆえに効率化のニーズも高く、そのための技術や手法に注目が集まっています。品質検査の効率化自体は、コンピューターをはじめとしたデジタル技術の黎明期から課題とされていましたが、従来のカメラやセンサー検知では検出しきれない細かいキズや汚れが残り、結局は人間の目視に頼るしかないという状況が続いていました。
しかし近年、高性能カメラやセンサー、AI技術の普及が進み、外観検査の自動化が実現できるまでにデジタル技術が進化したことで、導入に踏み出す企業が増えているのです。
検査装置による自動化
高精度のカメラやセンサーを搭載した検査装置により、目視による品質検査を自動化することで、検査に要する時間を大幅に短縮し、昼夜問わず検査し続けることが可能となります。
人間は長時間働き続けると、疲労で集中力が低下しミスが起こりやすくなりますが、細かな違いを見分け続ける検査工程ではなおさらです。また、検査員により検査基準が微妙に異なり、不良品を見逃してしまうといった属人的な問題もありますが、機械であればヒューマンエラーが一切発生せず、常に一定の検査精度を保つことができます。
2022年5月に厚生労働省が公表した「2022年版 ものづくり白書」によると、製造業における若年就業者数は約20年間で121万人減少しており、今後も少子高齢化の影響を受けて十分な人材を確保するのがさらに難しくなることが予想されています。
システムの導入に伴い初期費用はかかりますが、長期的な検査コストや人件費、人材確保のための手間やコストを考えると、品質検査の自動化はコストパフォーマンスに優れた施策だと言えるでしょう。
関連記事:検査の自動化で現場改善!課題と解決策とは
AIによる検査精度の向上
検査機器にAIの技術を取り入れることで、目視で判断できる箇所だけなく、人間の触感や音感を使って行っていた複雑な検査も自動化することが可能となります。
たとえば製品の強度や密度の検査においては、打撃音やその際の感触が検査のポイントとなりますが、このような感覚は数値化や客観的な検査基準の設定が困難であり、ベテラン作業員の知識と経験によってのみ検査されている状況でした。
しかしながら、検査機器にAIを組み合わせることで、これらの感覚をデータ化と処理が可能となり、過去の検査結果を学習することで良・不良、異常、誤差などの判定基準を自ら学習し、判断できます。検査データが増えるほど検査精度が向上するという特性があるため、数ヶ月で熟練検査員をもしのぐ精度が期待できるのもAIの大きな特徴でしょう。
品質検査の効率化が生産性を向上させる
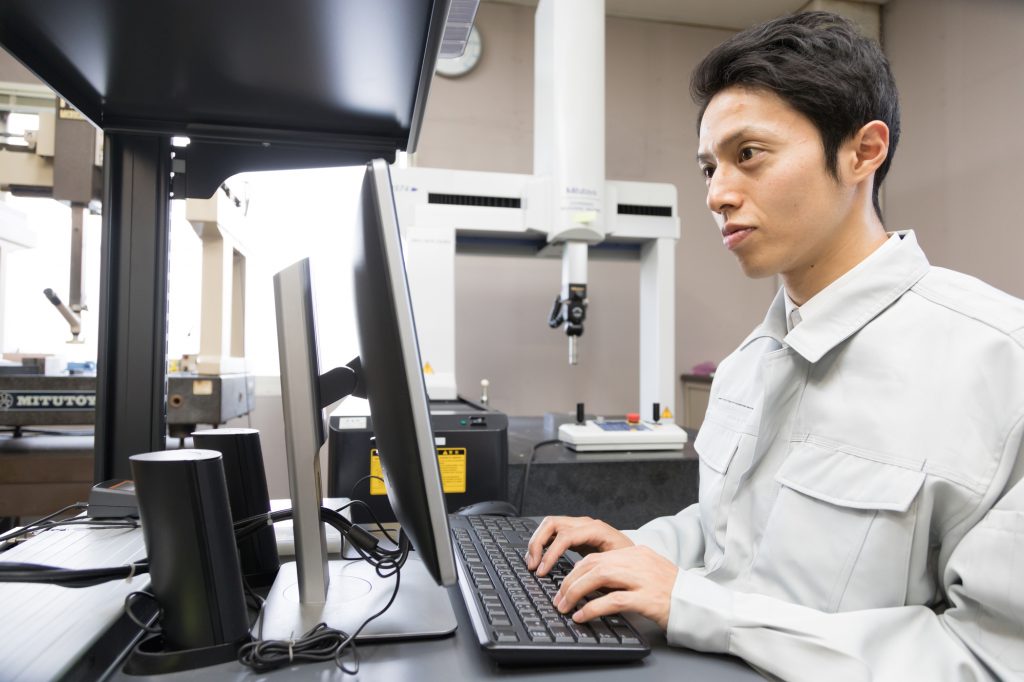
品質検査においては製造工程を細分化し、工程に応じた方法や基準で製品や部品の品質をチェックすることが求められます。適切な品質管理により顧客満足度を向上するうえで欠かせない。一方で、作業工程が多いにもかかわらず、未だ品質検査を人間の目視に頼っているという企業も多いのが現状です。 今後人員確保が難しくなることが予想される中、高品質を求める消費者のニーズに応えるためには、さらなる品質向上やコストカット、ヒューマンエラーの軽減などが必要不可欠となるでしょう。製造業のDXを検討するうえでも非常に優先度の高い業務ですので、検査装置やAI技術の導入を検討して損はありません。