目次
業務の生産性や効率向上に取り組む企業にとって、人が作業を行う工程で発生するミス、すなわちヒューマンエラーの抑制は大きなテーマです。ダブルチェックや日々の事例の共有に取り組んではいるものの、なかなか作業者の意識が高まらず、「ただやるだけ」で効果が出ていない企業も少なくないのではないでしょうか。
ヒューマンエラーは、発生したエラーの原因がどこにあるのか、なぜ発生したのかを一つ一つ追求し、適切な対策を講じることによってのみ抑制することができます。本記事を通じて、ヒューマンエラーの分類、分類ごとの対策方法について知っておきましょう。
ヒューマンエラーの分類と要因
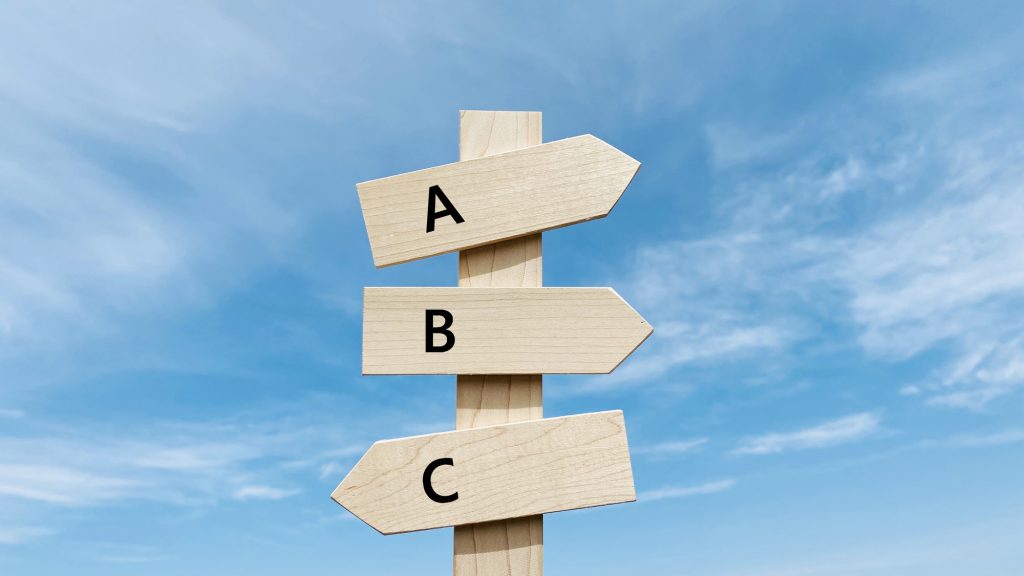
一口にヒューマンエラーといっても、その分類や要因はさまざまです。まず第一に、ミスが生じた際の作業者の意図によって、ヒューマンエラーを大きく2種類に分けることができます。
分類 | 説明 |
過失により発生したミス | 業務を正しく行おうとしたにもかかわらず発生したもの |
故意により発生したミス | 作業者が業務を正しく行う意識がなかったことによるもの |
このうち前者の「過失により発生したミス」がヒューマンエラーとして主に対策を求められるものとなります。後者の「故意により発生したミス」は、ヒューマンエラーに含まれるものもありますが、特に作業者の怠慢や悪意によって生じたものを「違反」として、ヒューマンエラーと分けて考えるのが一般的です。
そして過失によるミスは、その要因が作業の「計画」にあるのか、作業者が行う計画の「実行」にあるのかに応じてさらに3つに分類することができます。
分類 | 説明 | ミスの原因 | 対策例 |
計画通りの行動によって発生したミス | 計画通りの行動を実行したが、意図しない結果を生じたもの (ミステイク) | 作業計画自体に誤りがあった | 作業計画やマニュアルの見直し |
意図しない行動を行ってしまったことにより発生したミス | 行動中に計画を失念するなどして、意図した行動を遂行できなかったもの (ラプス) | 計画の管理や確認が適切でなかった | 作業マニュアルの整備やスケジュール・タスク管理の強化 |
何らかの要因で計画と異なる行動を行ってしまったもの (スリップ) | 作業者の行動に際して何らかの不都合があった | 生じた不都合に応じた対策 |
これらの分類により、「作業計画」や「マニュアル」から対策が必要となるのか、「作業者」へのヒューマンエラー防止対策が必要になるのかを明確にすることが、対策への第一歩と言えるでしょう。
ヒューマンエラーの12分類
ヒューマンエラーはさらに、その行動に至る要因によって12種類に分類できます。これらの分類によっても対策の方向性は異なるため、ヒューマンエラーが発生した場合には作業者に正確な聞き取りを行い、要因や状況を正確に把握しなければなりません。
分類 | 説明 | 具体例 |
知識や経験の不足 | 作業において注意すべき点に対する知識や経験が不足し生じたもの | ネジやボルトの締め付けはできているが、適正トルクを超えている |
慣れによる意識の欠如 | 慣れにより作業への注意が低下し生じたもの | 長年の対応から大丈夫だろうと思い込み、フォークリフトに過剰な積載を行う |
不注意 | ある作業に集中していたがゆえに、別の点への注意が疎かになり生じたもの | 部品の組み付け作業に集中するあまり工具が製品本体に接触、傷や不良を生じてしまう |
連絡・連携不足 | 作業に対する連絡や引き継ぎが不十分であったために生じたもの | 作業工程の変更が周知されておらず、従来通りの作業を行ってしまう |
組織・集団の欠陥 | 組織や集団において作業に影響する圧力がかかっており生じたもの | コスト削減や納期短縮が最優先になり、作業や検査を適当に行ってしまう |
業務の省略 | 面倒な手順を省略、効率化しようとする意識から生じたもの | ダブルチェックを非効率だと考え省略した結果、品質不良を見逃してしまう |
場面行動本能 (一つの物事に集中し、周りの状況を見ず行動してしまう) | トラブルの発生など、瞬間的に別のものに注意が集中してしまうことにより生じたもの | 作業中に部品を落とし、反射的に拾おうとした結果製品や設備に傷を付けてしまう |
パニック | 何らかの要因により作業者が冷静さを欠いたことで生じたもの | 作業途中に電動工具や設備が動かないことに焦り、不適切な操作をした結果やトラブルや設備故障が起こる |
錯覚(見間違え、聞き間違え、思い込み) | 作業指示やマニュアルの解釈を誤り、正しいと思い込んで行った結果生じたもの | 部品の保管場所が常に一定だと思い込み、誤った部品をピックアップする |
中高年の機能、体力の低下 | 身体能力が低下していることを自覚せず作業したことにより生じたもの | 数年前は1人で持てていた重い荷物が持てなくなっており、落としてしまう |
疲労や過度な負担 | 疲労により注意力が低下し発生したもの | 残業続きとなっていた作業員が日常では考えにくい単純なミスを起こす |
単調作業による意識低下 | 単純な反復作業の繰り返しにより注意力が低下し発生したもの | 同じ製品の検査を長時間続ける中で、チェックすべき項目を見落としてしまう |
作業者に起因する5つの内的要因
ここまでに述べた分類は作業環境や業務内容、作業者の技能に起因したものとなっており、理解することで全ての作業員に対して一律で対策を講じられるものです。しかし実際にはヒューマンエラーが作業員それぞれの「性格や考え方」に起因して発生する場合もあります。
具体的には、作業者の以下の特性によりヒューマンエラーの頻度や傾向、作業者それぞれに必要となる対策が異なるでしょう。
- 思い込みが強い、自分は正しいと考えがち
- 物忘れが激しく、失念が多い
- 慌てもので注意力が低い
- モチベーションの波が激しいなど、精神的に不安定
- 体調に不安を抱えている
これらの特性はヒューマンエラー以上に、業務や作業への適正にも大きく影響します。したがって、改善のための指導や働きかけは行いつつ、作業者の個性として捉え、無理なく作業ができる工程に配属するといった取り組みも検討すべきです。
ヒューマンエラー対策・防止のポイント
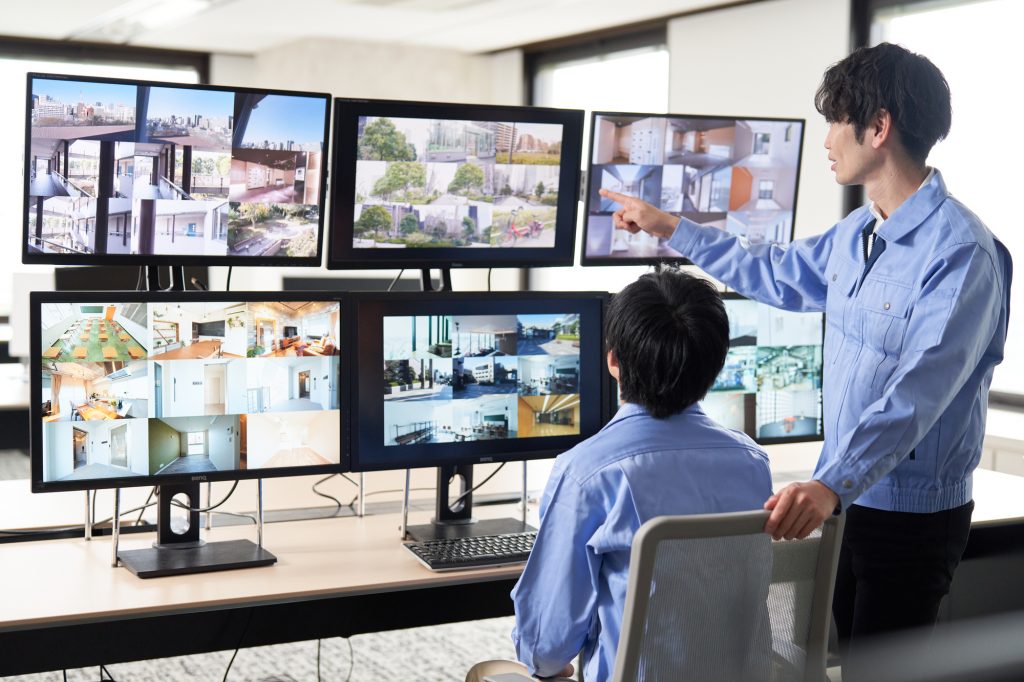
ヒューマンエラーの分類や要因について理解が深まれば、あとはそれらを踏まえた対策です。業務内容や発生しているエラーによって対策は異なるものの、作業内容や社内制度の変更、意識付けなどによって対策する「ソフト面」と、機械設備や工具、社内システムなどの整備により対策する「ハード面」の両面で考えなければなりません。
ソフト面での対策
ソフト面の対策は、組織体制や社内制度、業務内容の最適化といった「仕組み」の改善でヒューマンエラーを抑制することが基本的な考えとなります。
分類 | 対策例 |
知識や経験の不足 | 研修やトレーニング制度の充実 熟練作業者によるOJTやダブルチェック |
慣れによる意識の欠如 | エラーやヒヤリハット事例の共有 品質向上やスキルアップに対するインセンティブの設定 |
不注意 | 作業者への注意喚起や安全教育 余裕のある作業内容やタクトタイムの設定 |
連絡・連携不足 | 連絡フローの整備 (作業者同士での連絡は避け、管理者が直接各作業者に連絡するなど) |
組織・集団の欠陥 | 組織風土の見直し 無理のない生産計画の立案 |
業務の省略 | マニュアルの整備と遵守の意識付け 効率化提案に対するインセンティブの設定 (業務の効率化や省略を事前に把握することで、そのリスクを評価) |
場面行動本能 (一つの物事に集中し、周りの状況を見ず行動してしまう) | 作業体制の改善 (重量物を扱う、高所作業を行うといった場合は必ず複数人で対応するなど) |
パニック | 稼働の一時停止や作業者のサポートなどの適切な対応 作業者の特性や性格の把握と適切な配置 |
錯覚(見間違え、聞き間違え、思い込み) | 定期的な作業内容理解度のチェック 連絡フローの整備 (作業内容や作業環境の変更を周知する) |
中高年の機能、体力の低下 | 作業者の健康状態やパフォーマンスの把握 余裕を持った人員配置 |
疲労や過度な負担 | 適切な休憩や長時間労働の抑制 無理のない生産計画の立案 |
単調作業による意識低下 | 積雪な休憩や長時間労働の抑制 業務時間内の配置換えといった意識低下を防止する取り組み |
ハード面での対策
ハード面での対策は、新たな設備の導入や既存の設備の見直し、社内システムやデジタル技術の活用が主な取り組みです。導入時のコストや負担は生じるものの、適切に活用することでヒューマンエラーを大きく抑制する可能性を秘めています。
作業環境の改善
作業環境の改善は、ハード面の対策の中で最も取り組みやすい施策です。作業者が作業を行う際の周辺環境、具体的には作業場所の広さやレイアウト、設備や工具の配置変更によりヒューマンエラーを防止する対策です。
これらは不注意や場面行動本能、パニックによるヒューマンエラー防止に特に有効で、仮に不意な行動をしてしまった場合にも損害や怪我が生じないような作業環境を作っておくことでヒューマンエラーを予防する、あるいは被害を最小限に留めることができます。
▼具体例
- 重量物ほど低い場所に置くことで落下のリスクを軽減
- 作業場所にスペースを確保することで製品や他の作業員との接触を防止
- 作業場所の温度管理や防音により作業者の心理的負担を軽減
- 作業場所の整理整頓により、工具や部品の取り違えを防止
- 治具や工具の整備により作業のしやすさを向上
- 設備への後付け加工による作業性の向上
設備の新規導入や切り替え
油断や不注意を生みやすい作業については、設備やデジタル技術の新規導入により自動化することも検討の余地があります。作業効率の改善や省人化など、そのメリットはヒューマンエラー抑制に留まりません。
また、老朽化した設備はトラブルの可能性を高めるとともに、新たな製品の製造や既存製品の製造工程の変更に対応できない場合もあります。人の手で既存の設備を無理に活用するとなればヒューマンエラーのリスクも高まるため、設備の切り替えを検討すべきでしょう。
▼具体例
- 検査など長時間の集中が求められる工程を画像認識技術により自動化
- 高所や危険を伴う場所での保守点検をドローンにより自動化
- 物品の移動や搬送といった単純作業を搬送機(AGV等)により機械化
- 最新設備の導入による機械作業工程の拡大
- MES(製造実行システム)での管理に対応した設備への切り替え
- 迅速に状況報告ができる通信機器の導入
関連記事:製造業において画像解析/画像認識技術を活用している企業7社の事例
関連記事:製造実行システム・MESとは?導入のメリットや事例、ERPとの違い
ナレッジマネジメントシステムの整備
マニュアルの整備や教育・トレーニングの強化はソフト面の対策として取り組めるものですが、そのための時間を別途確保する必要があることから、通常の業務と並行して進めるのは容易ではありません。
このような場合、情報を迅速に共有・活用できるITシステムの整備により、ソフト面の対策をより速やかに進めることができます。また、整備したマニュアルやノウハウを活用するにあたっても、ナレッジマネジメントシステムが大きな力を発揮するでしょう。
▼具体例
- リアルタイムでの情報共有が可能なグループウェアの導入
- 業務マニュアルや社内文書を速やかに検索できるAI文書検索システムの導入
- 業務マニュアルや各種ノウハウをデータベース化したナレッジベースの構築
- 日報やヒヤリハット事例の分析をサポートするBIツールの活用
- トラブル対応におけるQ&Aを速やかに確認できるAIチャットボットの導入
- 製造工程や設備稼働を一元管理するシステムの導入(スマートファクトリー化)
関連記事:文書検索をAIシステムで効率化!メリットや導入のポイントを紹介
関連記事:AI活用がナレッジベース構築やナレッジマネジメントを加速させる理由
関連記事:日報の分析方法を徹底解説!正しく管理し、活用する方法とは?
要因を理解し、適切な手段をとるべきヒューマンエラー対策
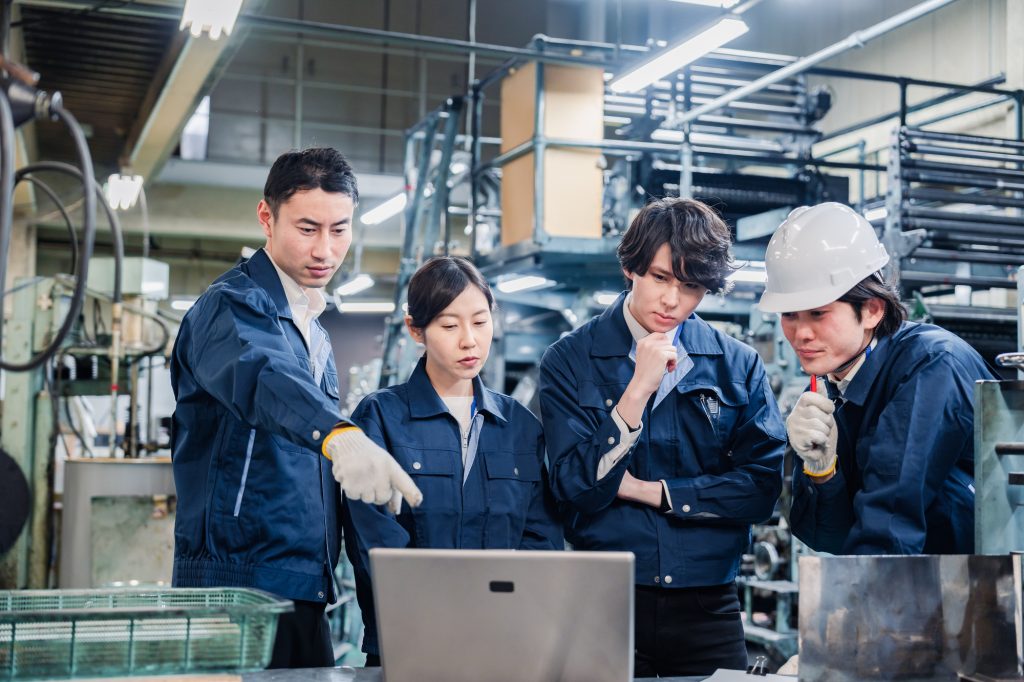
ヒューマンエラーの対策において重要なのは、発生の要因やヒューマンエラーの分類を正しく理解し、適切な手段を選んで講じることです。また、人の手を介する作業を減らす製造工程の自動化も、ヒューマンエラーの抑制防止、ひいては作業全体の効率化において効果を発揮することでしょう。
しかしながら、製造工程の全てを自動化することは難しく、それゆえに人の手による作業、そしてヒューマンエラーをゼロにすることはできません。だからこそ発生してしまったヒューマンエラーに対してその責任を追求し叱責するのではなく、原因を追求し、再発防止のための対策を講じることが求められます。
そして、全ての作業の根底にある作業計画や作業マニュアルも、これらの再発防止策を組み込み日々修正・改善しなければなりません。面倒に感じられるこれらの作業をいかにスムーズに進められるかどうか、鍵を握るのがナレッジマネジメントシステムだと言えるでしょう。