製造業においては、品質・コスト・納期をいかに管理し最適化するかが大きな課題となっており、実現手段として代表的なのがDXによる業務の可視化・効率化です。そしてDXの中でも、PLMの導入によって最適化を実現する動きが近年注目を集めています。
本記事では主に製造部門の管理者にとって重要となるPLMの概念やメリット、実際の事例について紹介します。
PLM(製品ライフサイクル管理)の意味と目的
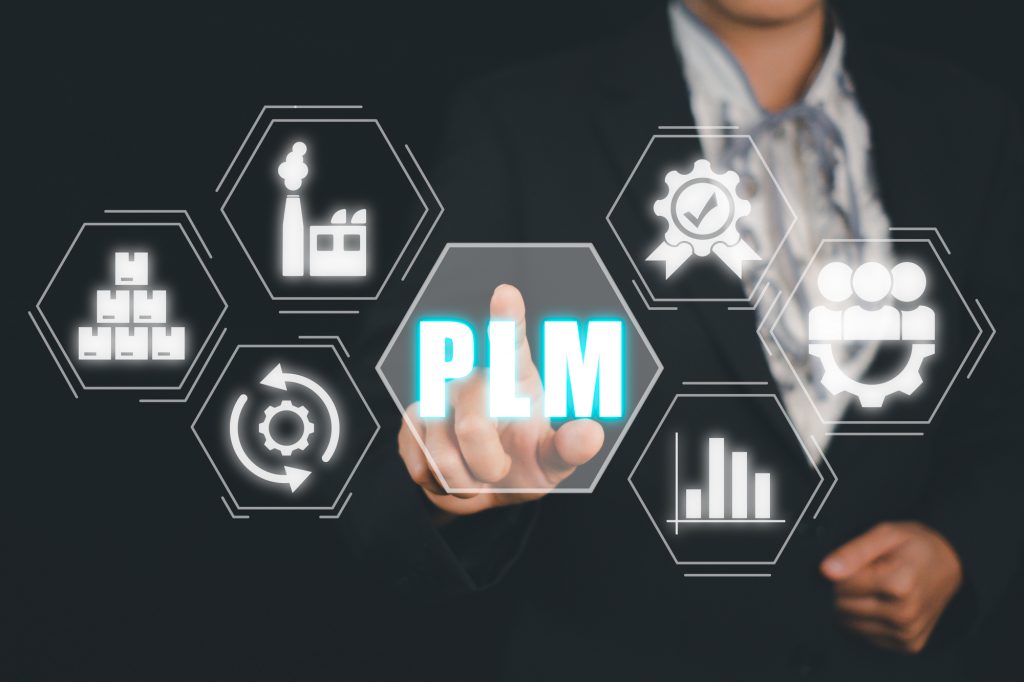
PLM(Product Lifecycle Management=製品ライフサイクル管理)とは、自社製品および関連サービスにおける「企画構想・設計・調達・生産・保守・終売・廃棄」など、一連の製品ライフサイクルに関わる情報やデータを一元管理するための活動です。
また、PLMを実現するための情報システム全般を指してPLMと呼称する場合もあります。
PLMシステムやパッケージでできること
PLMは、製造における一連のライフサイクルで以下の役割を果たします。
- プロジェクト・ポートフォリオ管理
- CAD(コンピュータ支援設計)の管理
- BOM(部品表)の管理
- 顧客からのフィードバックや不良品情報の管理
- 各工程に関連したドキュメントやデータの管理
PLMは上記の情報やデータを一元管理し、部門横断的に製造フローの全体像を可視化できるシステムです。たとえば企画部門/設計部門/生産部門といったように、工程ごとに担当部門が分かれている場合、前後工程の業務内容やデータが不明瞭となりがちですが、PLMによって一連の情報が管理・共有されることで部門間での、あるいは外部企業とのミスマッチや、それにより非効率となっている業務を明らかにできます。
類似する概念との違い
PLMはデータの一元管理を目的とした概念ですが、類似した意味を持つ用語がいくつか存在します。
代表的なものとして「PDM(製品情報管理)・MES(製造実行システム)ERP(企業資源計画)・ALM(アプリケーションライフサイクル管理)」この4つは意味が近似しているため、混同しないようにしましょう。
PDM(製品情報管理)とPLMの違い
PDMとは、設計工程に関わるデータの管理に特化したシステムです。設計図や部品、生産に関する管理機能を備えていますが、企画構想といった前工程、販売〜保守といった後工程まで管理するものではありません。
PLMはPDMの対象領域を含めた製造フロー全体を管理できる点が違いとしてあげられるでしょう。
PDM | PLM |
製品ライフサイクルの内、製品の設計仕様や製品データを管理 | 企画〜保守まで包括的に製品ライフサイクルを管理 |
CAD(コンピュータ支援設計)、BOM(部品表)など主に設計データが対象 | QCD(品質・コスト・納期)に関わる全てのワークフローが対象 |
MES(製造実行システム)とPLMの違い
MESは各種情報に基づく生産の実行や、設備稼働を司るシステムのことです。PLMは計画にフォーカスしたシステムに対し、MESは実行にフォーカスが当てられます。
製造業務をデジタル化・DX化するには、PLMに蓄積されたデータを適切な形でMESに渡し、またMESにおいて現場レベルで最適化されたデータをPLMにフィードバックするといった運用が必要です。
MES | PLM |
製造機械や従業員の作業状況や管理を実行するシステム | 製品ライフサイクルに関わるオペレーションを一元管理するシステム |
生産ライン上の連携や生産現場の最適化に用いられる | 企業競争力や生産体制の改善・強化に用いられる |
関連記事:製造実行システム・MESとは?導入のメリットや事例、ERPとの違い
ERP(企業資源計画)とPLMの違い
ERP(企業資源計画)とは、人・モノ・カネといった経営資源を統合管理するシステムです。PLMは生産視点で製造販売業務を管理するのに対し、ERPは経理財務的な視点で製造販売に伴う経営資源を管理するために活用されます。
目的が異なる概念ではありますが、製造業においては両者を連携した経営改善が重要となるでしょう。
ERP | PLM |
経営資源の統合管理システム | 製品製造に関わるフローを一元管理するシステム |
企業経営の資源要素を適切に分配・有効活用するために用いられる | 製造力の改善・強化に用いられる |
ALM(アプリケーションライフサイクル管理)とPLMの違い
ALMはアプリケーションの企画〜保守に関わる一連のライフサイクルを管理するもので、PLMに近い概念ですが、アプリ・ソフトウェア開発など「形のない製品・サービス」を管理する点が大きな違いです。
ALM | PLM |
アプリケーションの開発〜保守に関わるオペレーションを包括的に管理するシステム | 製品ライフサイクルに関わるオペレーションを包括的に管理するシステム |
PLM導入のメリットや効果
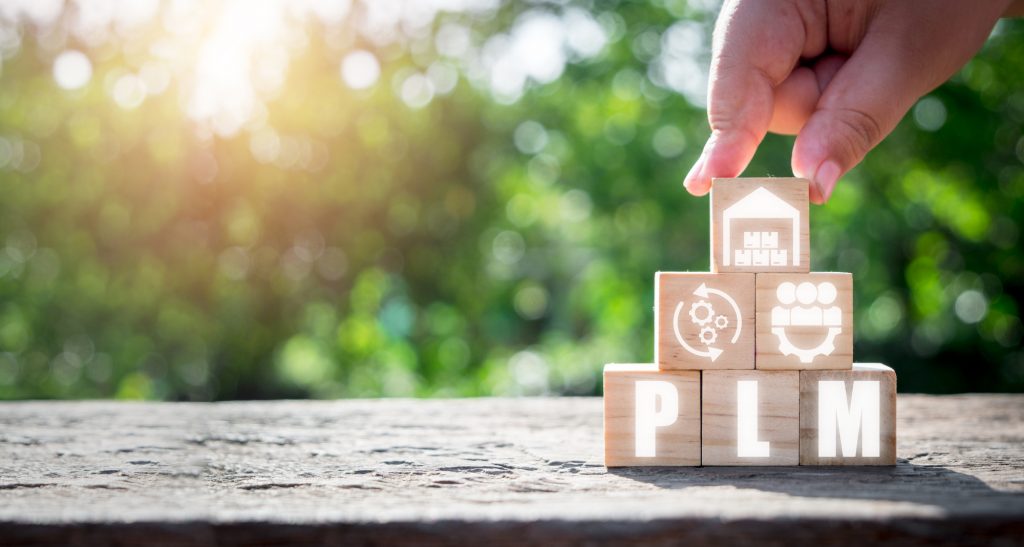
それでは、PLMによる製造工程の一元管理で得られるメリットはなんでしょうか。主なメリットとして次の3点があげられます。
開発・製造期間の短縮
製品ライフサイクルにおけるデータをPLMで把握できれば、より効率的なプランニングや業務改善が可能です。業務や工程の改善は本来、各部門間での綿密なすり合わせが必要なものですが、統合管理されたデータを活用することでその期間を短縮し、より素早く実行、結果として開発・製造期間の短縮につながります。
また、製造工程全体のデータからより早期かつ正確に生産スケジュールを策定できるため、原料調達のタイミングを最適化する、出荷のタイムラグを解消するといった形でリードタイムの短縮に寄与します。
品質・コスト管理の強化
PLMは商品・サービスのQCD(品質・コスト・納期)を高める手法として効果的です。各工程における不具合やフィードバック、対応策などを社内横断的に共有することで、早期の原因究明や迅速な品質改善アクションにつなげられます。
材料費や労務費、諸経費を可視化できることから、削減案の策定や成果の確認も容易なうえ、納期の短縮にも貢献する点は前述した通りです。
サプライチェーンの強靭化
PLMにより製造データが一元管理されることで、サプライチェーンになんらかの変化があった場合でも、トラブルやリスクを速やかに把握し対応できます。
一例として、設計部門と製造部門の情報共有が不十分な場合、仕入れ先や部品規格の変更による作業トラブルや生産停止・遅延のリスクが否めません。しかしPLMなら、サプライチェーンの変化だけでなく、部門の再編成やM&A等の事業拡大で組織の形が変わった場合でも、引き継ぎや製造体制の再構築を容易にしてくれます。
PLMの課題・失敗例
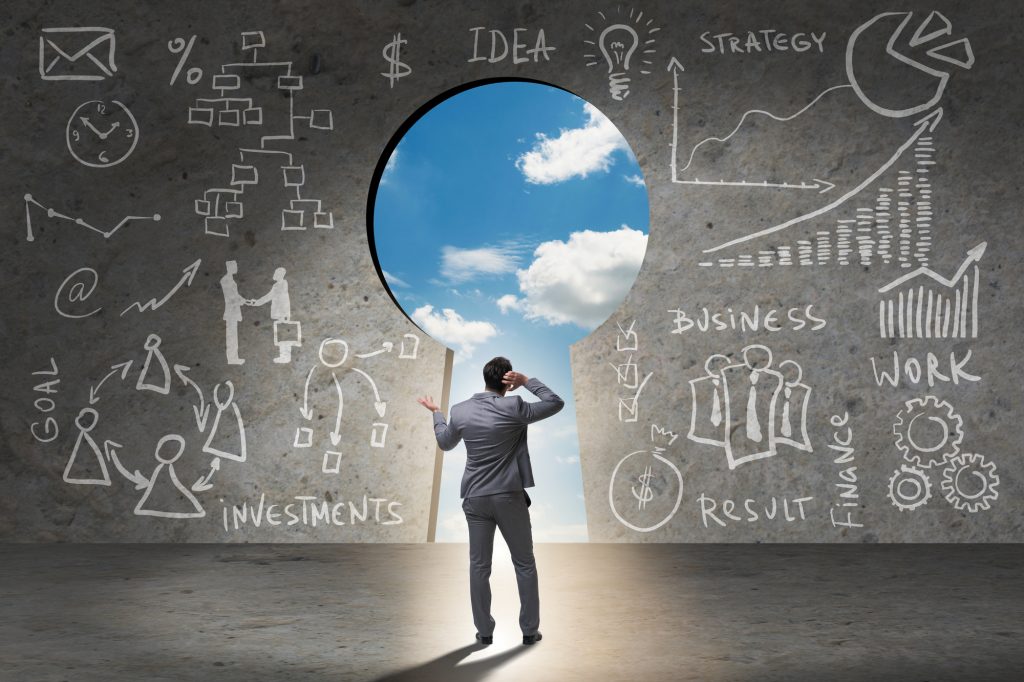
しかしながら、PLMは導入するだけで効果が見込める万能なものではありません。導入や運用にあたって抱えやすい課題や失敗例、またその理由についても知っておきましょう。
導入前に業務フローの見直しが必要
PLMは製造〜販売の工程を横断的に管理するため、導入企業にもそれに適した組織体制が求められます。PLMの管理運用や、製品ライフサイクル全体の連携を推進する部門を設置するといった形で、組織体制や業務フローの見直しを図る必要があるでしょう。
具体的には、以下の施策があげられます。
- 製造フローを全体を管理する監査部門の設立
- 各部門及び従業員に対するPLM導入の周知・マニュアルの配布・研修の実施
仮に、各部門が独自の方針でPLMを使用すると、部門によって活用が進まない、入力が滞るといった問題が生じます。これではPLMのメリットを十分に活かすことができません。
システムやツールの特徴が見えづらい
PLMシステムはさまざまなベンダーが提供していますが、組織体制や業務内容とそれぞれのシステム・ツールの使いやすさには相性があります。とはいえ、表面からはどのシステムも豊富な機能を備え、できることに大きな差がないように感じられるもの。コスト重視でのシステム選定になりがちなのがPLMの実情です。
PLMシステムの導入においては、コストや開発期間はもちろん、ベンダーの業務理解とそこから生まれる要件定義力が重要となります。業界・業務に精通しているベンダーであれば、スムーズな導入支援はもちろん、業務内容や導入目的に対してツールの相性はどうか、追加・削減すべき機能は何か、事前のアセスメントにも期待ができるでしょう。導入事例が豊富かどうかも、判断基準となります。
仮に自社業務と相性の悪いシステムを導入してしまった場合、うまく運用できずにコストだけが増加してしまう…といったことになりかねません。
企業間の連携やコラボレーション機能が不十分
PLMはあくまで社内を統合管理するシステム。パートナー企業との情報共有やコミュニケーション機能までを包括したシステムは多くありません。そのため、関連企業同士のアライアンスなど協力体制の構築・維持には変わらず人手を要すると考えておきましょう。
特に、資材の調達や製造の一部を外部のパートナー企業に委託している場合、PLMの導入で自社の業務スピードが向上しても、パートナー企業がそのビジネススピードに追いつけない可能性があります。この際、生産計画の調整をはじめとした対策を用意しておかなければ、生産が停滞し、リードタイムが変わらない…といった問題が生じかねません。
製造業におけるPLM導入事例
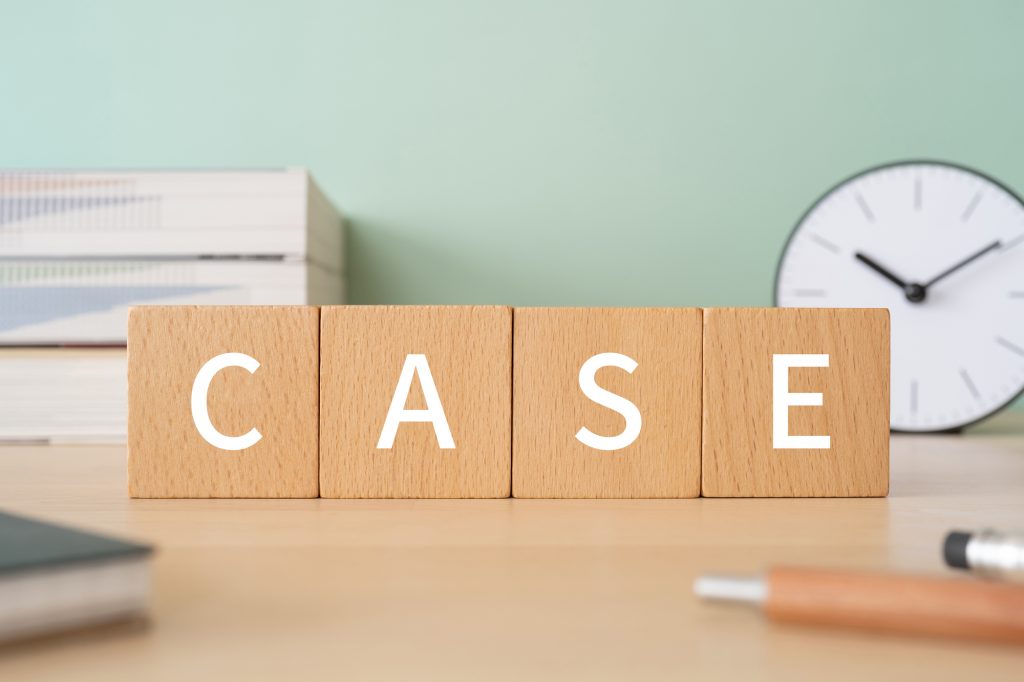
製造業において、製造フローの一元管理化によって体制の最適化や生産性の向上を図るには、製造拠点のPLM導入はもちろん、サプライチェーン上に存在するパートナー・関連企業との連携が必要不可欠です。
このことを踏まえ、製造業におけるPLM導入の成功事例を紹介します。
川崎重工株式会社
総合機械メーカーである川崎重工株式会社は、全社的なPLMシステムの構築・運用組織の立ち上げを行い、市場調査からアフターサービスに至るまで一連業務のスループットの最適化を図っています。
本事例から学ぶべきポイントは以下の通りです。
導入に至る背景・問題点 | ・各事業部門(社内カンパニー・関連会社)で最適化されたPLMシステムを導入していたが、個別運用であるために企業全体での連携が困難になっていた ・個別運用していた既存PLMシステムのコストが足かせになり、ビジネススピードに弊害が生じる事態に |
取り組み内容・工夫点 | ・組織の最適化を目的として、全社共通のPLMプラットフォーム「社内PaaS」を構築 ・システム内容は機能の追加や修正などある程度自由度を持たせ、各事業部門毎の多様な要件に応えられるようにした |
導入後に得られた成果 | ・製品ライフサイクルの基盤が最適化されたことで、事業の横展開が容易になった ・既存のPLM管理にかかるコストを80%削減 ・自社IT部門にかかる業務負担の軽減に成功 |
今後の課題点 | ・既存業務プロセスを見直し、経営資源の配分を最適化する ・市場と直接接点を持つマーケティングやアフターサービスの部門と連携し、ニーズに沿った製品企画を効率よく製造する仕組みを構築する |
同事例は、事業部門毎のPLMシステムをさらに統合管理するという一段階進んだケースですが、PLM管理をコーポレート側が担う、事業部門毎に業務に即したカスタマイズを行うなど、前述した「導入の課題」を乗り越え、結果的に大幅なコスト削減・業務効率化を実現しています。
PLMの導入は専門家へ相談を
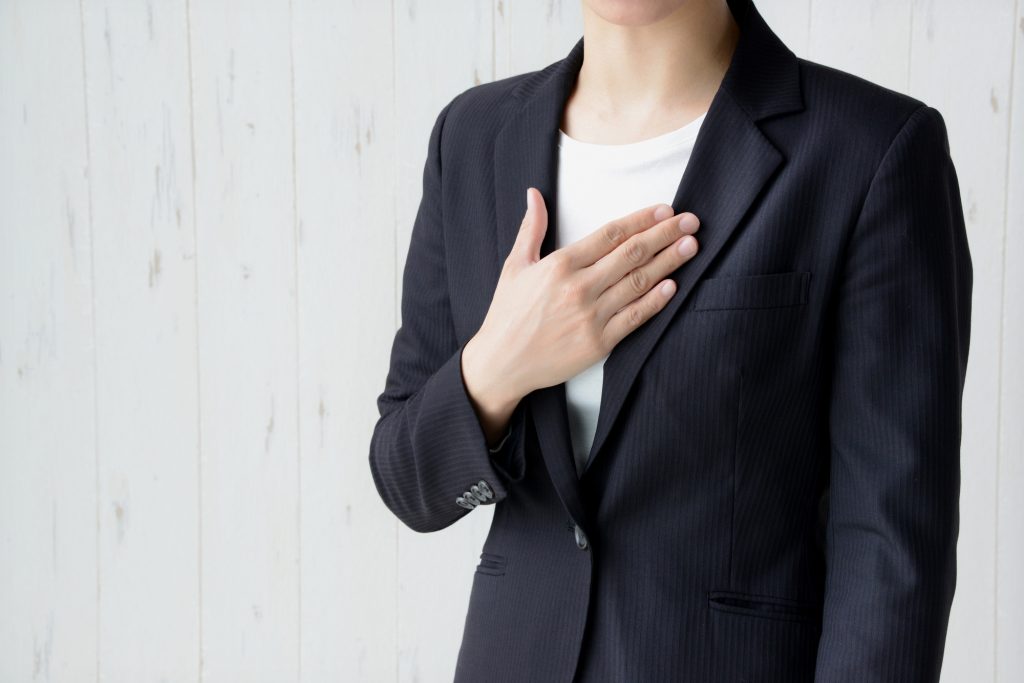
PLMは自社の製造フローを包括的に管理する概念です。製造フローにおける企画〜廃棄まで全てのプロセスが対象なため、導入にあたっては全社的な連携やシステムの要件定義など、大規模な作業が予想されます。
システム導入を前提とした業務改革には、デジタルテクノロジーの専門知識が欠かせません。したがって、PLM導入を検討する際は、まず専門のベンターへの相談をおすすめします。コストや作業期間だけでなく、「システムの仕様と業務フローをいつまでに、どのように合わせていくか」「そのうえで必要な機能は何か」といった点を相談しつつ開発を進めることで、失敗しないPLM導入が実現できるでしょう