目次
前回は、順送プレスを例にした「作り過ぎのムダ」へのアプローチを紹介しました。今回は手作業を例に解説を進め、「手待ち(仕掛)のムダ」へと続けます。
(執筆:関伸一/関ものづくり研究所)
記事一覧:【連載】関伸一の「ものづくりDX研究所」
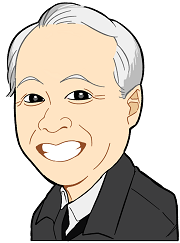
付加価値作業からのデータ取得がカギ
手作業の場合を考えてみましょう。単純化するために部品にボール盤で穴開けをするだけの製品を例とします(図1)。
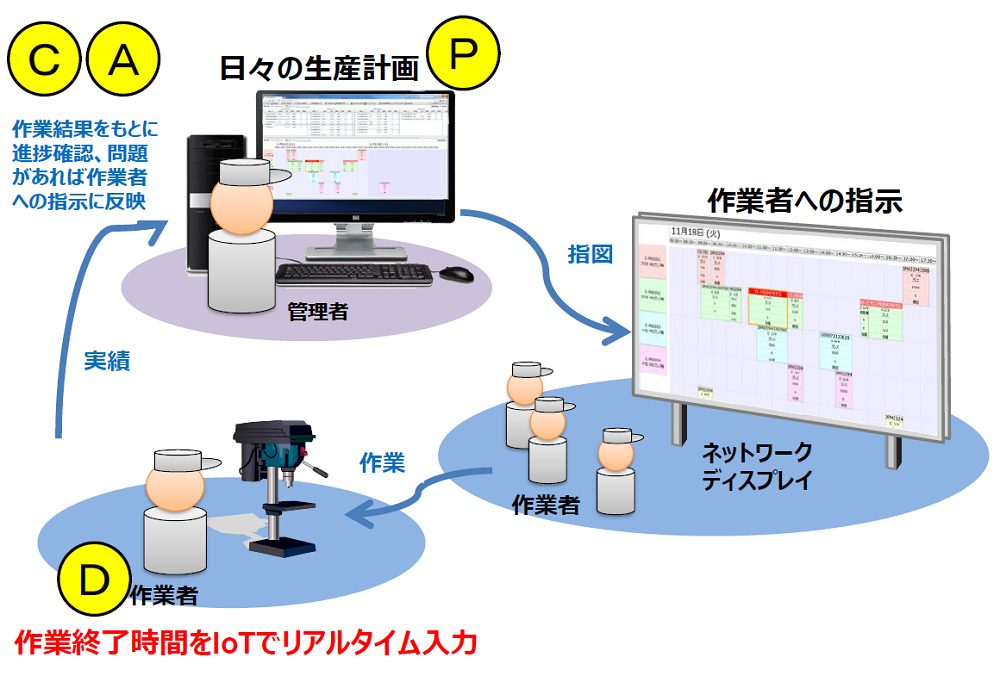
今や生産計画立案はソフトウェアが充実していて、製品、生産数、作業者のスキル、設備の数や状態などの情報を入力すれば無駄の少ない生産計画を自動的に算出してくれます。それを個々の作業者に日々振り分けて(生産指図)、生産に着手します(生産指図)。ここまではソフトウェアでデジタル化されているのですが、問題は実作業です。生産の着手時間と生産予定数完了後の時間のみ紙に記録(いわゆるバッチ処理)している現場がまだまだ多いのが現実です。
ボール盤に安価なセンサーを付けてカウントする手もありますが、それでは不良品を作ってしまった場合もカウントされてしまいます。筆者のお勧めは製品を箱に入れるためのシューター(滑り台)を設け、光電スイッチ(数千円で入手できる)と無線デバイス(これも数万円)を組み合わせ、製品が1個できるごとにカウントとタイムスタンプの情報を取ることです。
バッチ処理の欠点は、1個当たりの正しい工数が把握できないことに尽きます。作業総時間を生産総個数で割るのですから1個当たりの平均時間が出るだけで、真の問題点は見えません。センサーを使ったカウント方法に変えると次のような効果が出ます。
➀ 正確な生産数のカウント(人間が数えれば必ず間違う)
➁ 1個ごとの工数の把握(タイムスタンプを引き算するだけ)
➀は、まさに作りすぎのムダへ直接リーチできます。さらに②は次のような二次効果が期待できるのです。
直近100個の平均時間が60秒だったとします。1つの製品ができてから、120秒以上たってもセンサーから次の製品ができたという信号が来なかったら何らかのトラブルが起きている可能性があるので、工程管理者の携帯端末にアラートを飛ばす仕組みにすれば「デジタルあんどん」のできあがりです(「あんどん」とは生産工程の状態報告システムでTPSの要素の1つで、見える化の手法として有名)。そして生産の遅れ検知もスピーディにできるため、残業有無の判断など対応が迅速にできます。
図1をPDCAサイクルに当てはめると、「生産計画~生産指図」はPLAN、作業はDO、そして生産進捗の把握はCHECKになりますが、これをバッチ処理で行ってしまうと把握の頻度とスピードが遅くなり、結果ACTION、すなわち生産計画へのフィードバックが遅くなるのです。慢性的に残業が多い現場はこのPDCAサイクルを回すスピードが遅いことが大きな要因です。「あんどん」という優れた「見える化」の手法をデジタル化することで「知らせる化」に進化させることができます。IoTデバイスが目新しいものではなくなった今の時代、これくらいのことはローコストで可能です。KAIZEN for DXに着手するには良いテーマなのではないでしょうか。
手待ちや仕掛のムダへアプローチする
このムダの話をするのにはやはり制約条件理論(以下TOC:Theory Of Constraints)を解説しなければなりません。TOCはイスラエル の物理学者エリヤフ・ゴールドラット氏(1947~2011年)が提唱したもので、「その工程の生産性はボトルネック工程以上にはならない」という実にシンプルなものです。
図2を用いて解説すると、このようになります。
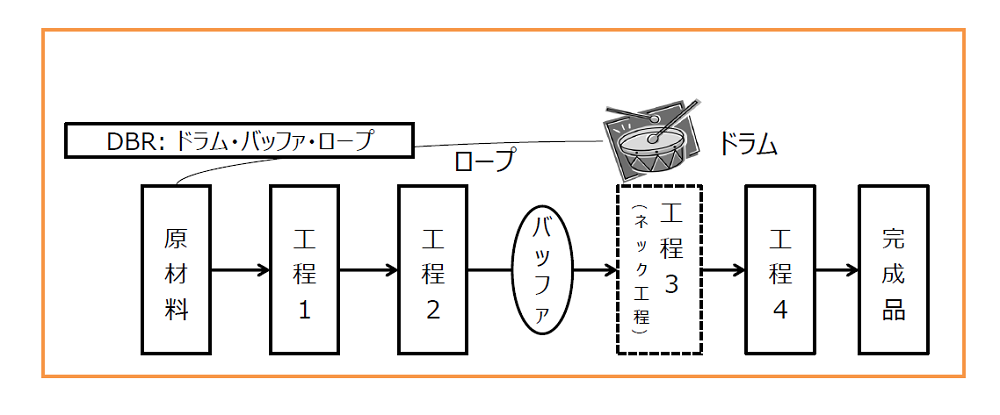
- 原材料が4つの工程を経て完成品になる。
- 工程1、2、4は時間当たり10個の生産能力を持つ
- 工程3は時間当たり5個しか生産できない(ボトルネック工程)
- 当然この工程の生産能力は時間当たり5個
- ボトルネック工程の前には仕掛品(バッファ)をある程度持つ
- そうすれば工程1、2が何らかのトラブルで止まっても、その間は仕掛品を使って工程3は止まらず、完成品の遅れを防止できる
- この状態にしておいて、工程3で1つ加工が終わったら、先頭工程(材料出し)にその情報を送る(工程3でドラムを鳴らし、その振動がロープを伝って先頭工程に伝わるという意味でドラムバッファロープと呼ばれます)
- そして工程3を改善し、生産能力を上げて行けば工程全体の生産性が上がる
- 工程3の設備をもう1台導入して時間当たり生産数を一気に10個にするという手もある
TOCは1984年に「ザ・ゴール」という小説仕立ての書籍で分かりやすく解説されました。多くの言語に訳され、「全世界で1000万人が読んだ」とされていて、2001年には日本語版も発行され当時のベストセラーとなりました。しかしながらいまだに全ての工程の前に仕掛品を置く現場が多く見られるのはなぜなのでしょう?
「1つの設備が止まって、みんなの手が空くと困るから」
「そもそも、どの設備がボトルネックになるかなんて分からないよ」
そんなご託を並べる経営者の机の上には「ザ・ゴール」が置いてあったりするので笑ってしまいます。
ゴールドラット氏は「生産のロット数は小さくした方が良い」と説いています。その究極が1個流しであり、TPSの考え方と共通しています。「どの設備がボトルネックになるかなんて分からないよ」という経営者には「試しに一個流しをしてみてください。しばらくするとどこかの工程の前に仕掛品が溜まります。1つ目のボトルネック工程はそこですよ。簡単じゃないですか」と筆者はアドバイスしています。TOCを実践すれば間違いなく現場の生産性は向上します。
TOCが適用しやすいのは、マンタイム(人間が何らかの作業を行う時間)よりもマシンタイム(機械設備で生産する時間)の占める割合が大きい場合です。マンタイムが長い場合、例えば人手による組立作業ではTOCは適用しにくい――いや、「できない」と言うのが筆者の考えです。人間の作業というのは様々な要因で時間がばらつきます。
担当作業が短ければ、絶対値としては短い時間ですが、それでは全くの単純作業になってしまいます。
ルネ・クレール監督の1931年のフランス映画「自由を我等に」、そしてあまりにも有名な1936年のチャーリー・チャプリンによる「モダン・タイムス」で皮肉られた辛く悲しいコンベヤーライン作業になってしまいます。
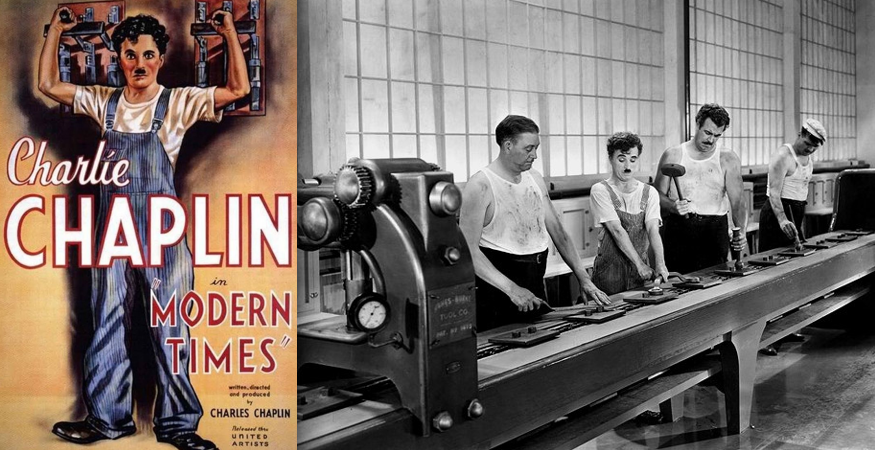
(映画「モダン・タイムス」より)
ここへのアプローチについては筆者が約25年前に当時の勤務先、ローランド ディー. ジー社で仲間と共に作り上げた完全一人完結セル生産、「デジタル屋台」が好例なのですが、この件について書き始めるとそれだけでコラムが十数回になってしまうので、「デジタル屋台」でネット検索していただければ様々な情報が得られるはずです。
関連リンク:「デジタル屋台」による一人一台生産 (日本機械学会誌/J-STAGE)
手待ちや仕掛は、全く付加価値を生まないムダの巣窟です。ここへのアプローチはハードルが若干高くなりますが効果は相当に高いので、ぜひチャレンジしてみてはいかがでしょうか。
記事一覧:【連載】関伸一の「ものづくりDX研究所」
執筆者プロフィール
関ものづくり研究所代表。株式会社Fiot代表取締役。株式会社エコム社外取締役、株式会社桜井製作所社外取締役、国立静岡大学大学院客員教授。
ローランド ディー. ジーにて製造部長として勤務していた時代には、完全一人完結セル生産「デジタル屋台生産システム」を開発。その成果が新聞・雑誌やテレビ番組などで報道されて話題に。ミスミグループ本社では、製造子会社の駿河精機 本社工場長、生産改革室長、環境・品質推進室長を兼務し、業務改善を推進した。
自身の専門である機械工学および統計学を基盤として、品質向上を切り口に現場の改善を中心とした業務に携わる。ISO9001/14001マネジメントシステムにも精通し、経営に寄与するマネジメントシステムの構築に精力的に取り組み、その延長線上として労働安全衛生を含むリスクマネジメントシステムの構築にもかかわる。
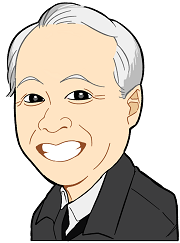