目次
製造業での品質管理を中心としたいろいろな業務の問題解決で使える「製造業新QC/QC7つ道具」について基本から解説します。いまさら聞けない人や、誰かに教えないといけない人も、ぜひご活用ください。
(執筆:小林由美 / facetライター、編集者)
記事一覧:【連載】「新QC&QC7つ道具」基本のキ
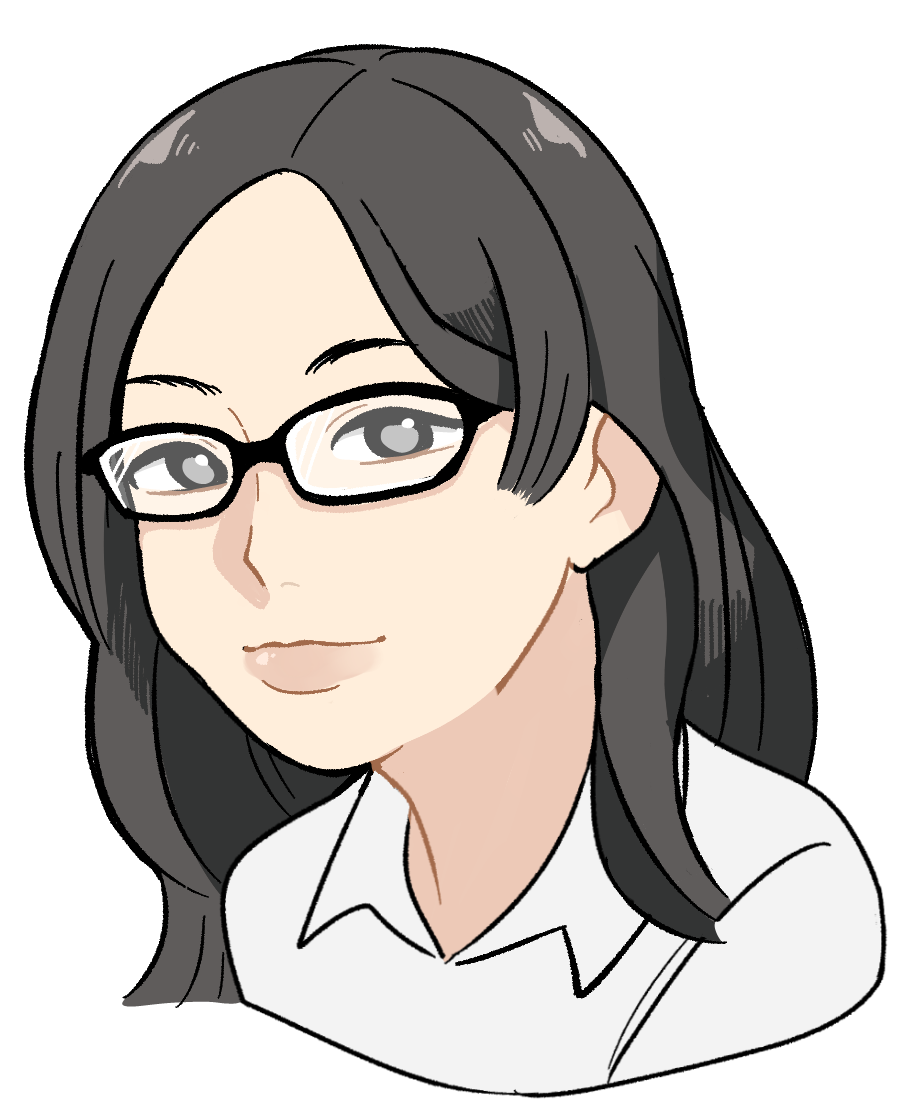
連関図法とは?
連関図法とは、「原因と結果」や「目的と手段」などの相関について、それぞれの因果関係、すなわち「因果同士の連関(互いにかかわり合っていること)」の構造について連関図として表現して整理する手法です。
連関図(図1)を構成する要素は、以下です。ここで取り扱うのは、簡潔に原因を表現した「言語データ」(言葉)です。
- 中核となる課題(問題)
- 課題と関係しうる全ての要因(一次要因)
- 一次要因のさらなる要因(二次要因以降)
- 上記要素の因果関係を表現する矢印
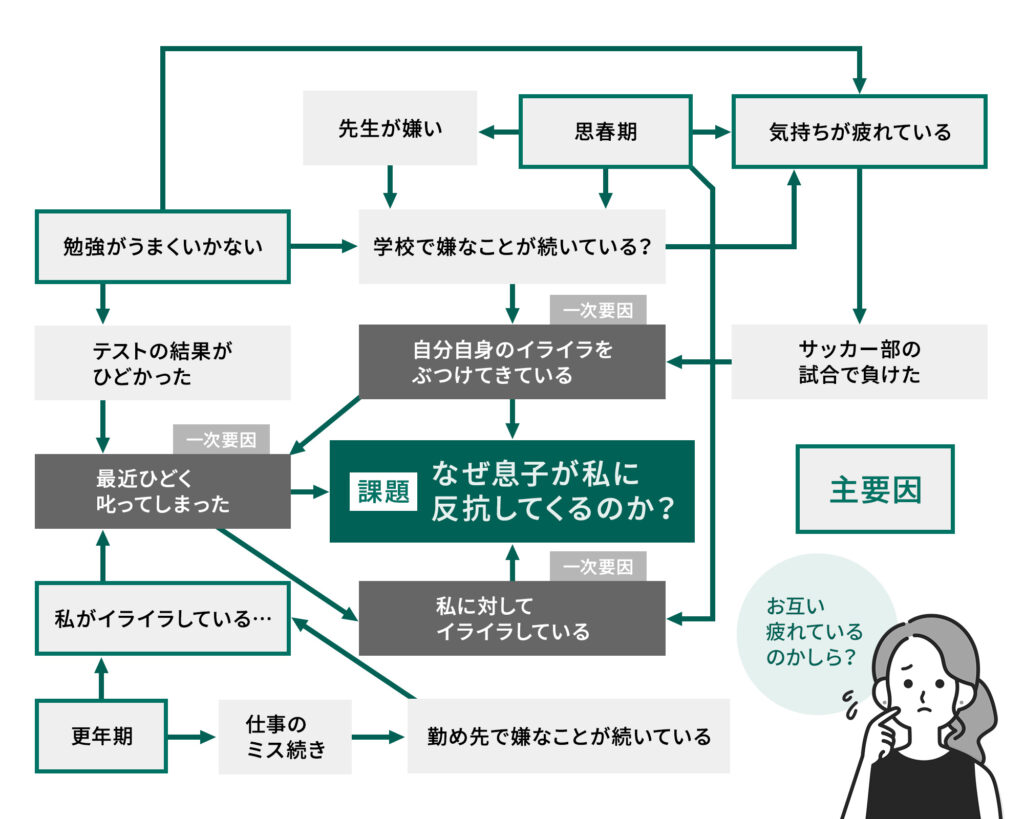
連関図を作図する手順は、大まかには下記のとおりです。
- 取り上げる問題の設定
- 一次要因の抽出
- 上で挙げた要因の掘り下げ
- 連関図のチェックと修正
- 主要因の抽出
課題や問題に関する要因について「なぜなぜ問答」をしながら自由にいくつも挙げていき、「原因」となることから「結果」になることへ向かって矢印を引きます。整理をしていきながら、「主要因」(重視すべき原因)はどれか検討していきます。こうして作り上げる連関図では、「現状抱える課題の全体像」と「因果関係の詳細」を同時に見ることができます。
製造業の業務の中では、例えば「ある生産現場での作業効率が悪い」「品質問題がなぜ再発するのか」、あるいは「DX推進を積極的に進めたい」といった問題について詳しく要因を特定する、あるいは顧客満足度と企業活動の評価との関連性を分析するといったケースで活用できます。
連関図は、PowerPointやExcelの図形(シェイプ)、ホワイトボードや模造紙、付箋紙など、各々でやりやすい方法で作図します。
特性要因図と連関図の使い分け
「結果と原因の関係を整理する」といえば、「QC7つ道具」の1つ「特性要因図」のことが思い浮かぶ方もいるかもしれません。
関連記事:起こった問題の原因を効率よく探る「特性要因図」とは
特性要因図も連関図も、起源が同じであり、経営工学者の千住鎮雄氏らが1960~70年代にかけて開発した手法です。いずれも、製造現場のさまざまな問題における業務の問題の連関を分析するために生まれました。
特性要因図はそれぞれの要因が結果に向かって一直線に伸びる構造をしています(図2)。このような構造な故、要因同士の因果関係は表現できません。
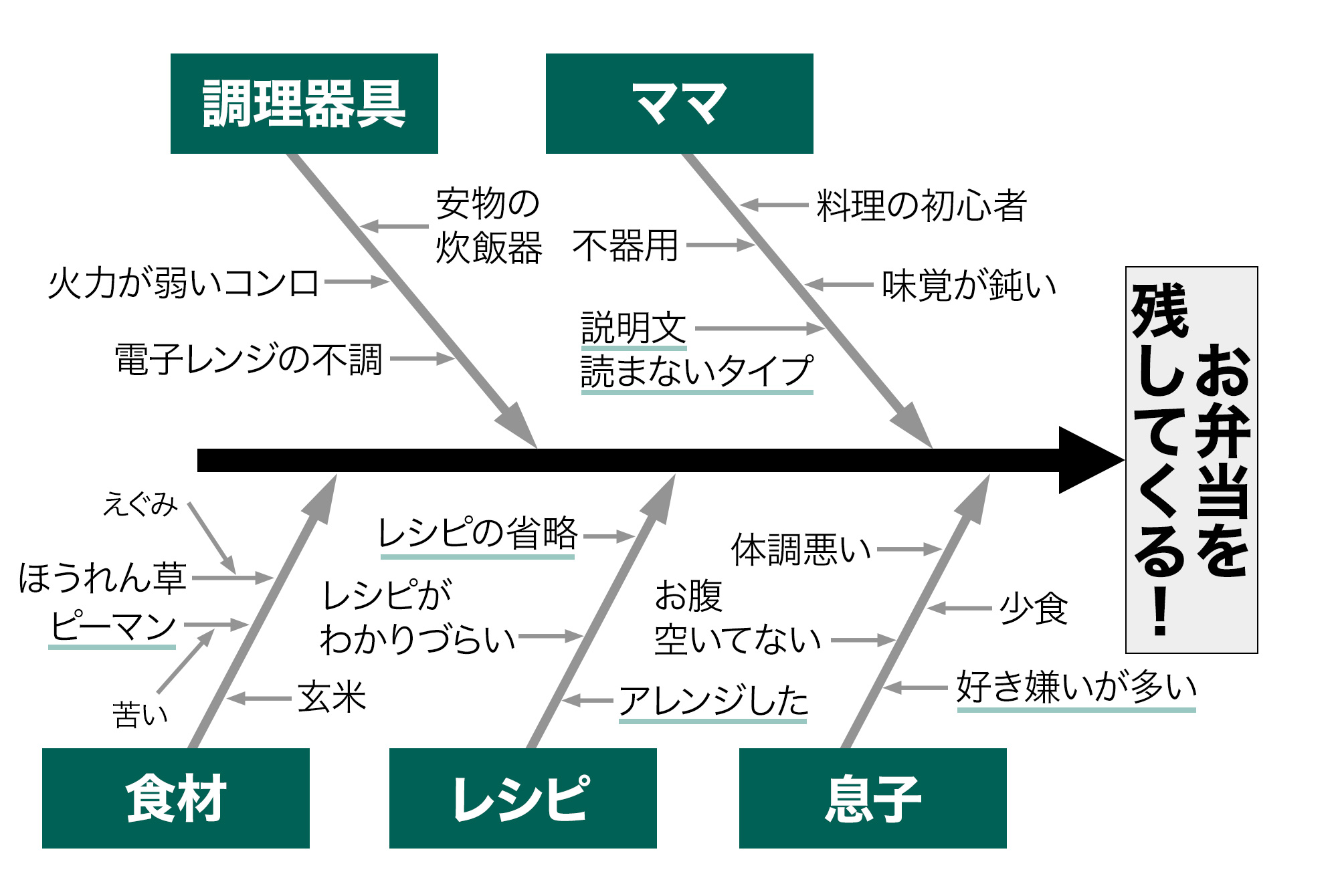
図1では、忘れ物の頻度と、忘れたら困る度数を10段階評価して数字にしたデータを、パレート図にまとめています。
解決したい問題がかなり漠然としていたり、原因が混とんとしていたりする場合は、連関図が適しています。連関図は、洗い出した要因全てに対して因果関係が表現できるからです。
実際には、「連関図で漠然とした問題を整理して具体化してから、特性要因図で根本原因を突き止める」といった運用が良く行われます。さらに、親和図法で情報整理をした上で連関図を作ることもよくあります。
連関図法は何回も練り直せ
連関図法の活用は現状分析に特化しているため、分析が精密なほど真の原因に近づくことができます。「連関図を1回書いてみて終わり」ではなく、複数回に分けて、納得いくまで内容をブラッシュアップしていく必要があります。
例えば、以下のようなステップが推奨されています(巻末の参考書籍)。
- 自分で、もしくは身近にいる上司や部下と一緒に机上で連関図を書く
- 現場に連関図を持っていって、そこで気づいたことを内容に盛り込む
- 関係者と議論をしながら連関図を仕上げる
机上で一度作った連関図を、少し時間をおいてから見返して新たな気づきを得るという方法もあります。
産業用ロボット導入検討で連関図を活用する
ここでは、産業用ロボットを導入する際の問題抽出を例に連関図を作図します。ロボット発注者側の企業が現場課題を連関図でまとめておけば、ロボットSIerとの要件定義の段階の説明資料として役立ちます。
部品メーカーのプロトリュード社は、ロボットを導入することで、現場の作業を効率化して、利益率を高めていきたいと考えました。
メインテーマの決定
プロトリュード社では、C部品の製造について、面倒な手作業が多いA工程がボトルネックになって、納品が遅れがちであることが判明しました。製品の引き合いが増えてきていることもあって、何とかしなければなりません。情報システム部に所属する若手で、DX推進担当を任されたDさんは、C部品の生産現場の人たちと話をすることにしました。
A工程にロボットを導入して自動化すれば、納期短縮をして生産キャパも増やせるかもしれませんし、原価をさらに下げられるかもしれません。現場の担当者の能力も、もっと最適な業務に割り当てることも可能です。それに、現場の人たちのストレスもかなり減るでしょう。
そういうわけで、ここでは「工程Aの作業に時間がかかりすぎる」としました。付箋紙に太字で書き起こして、模造紙の中央に配置しましょう(図3)。
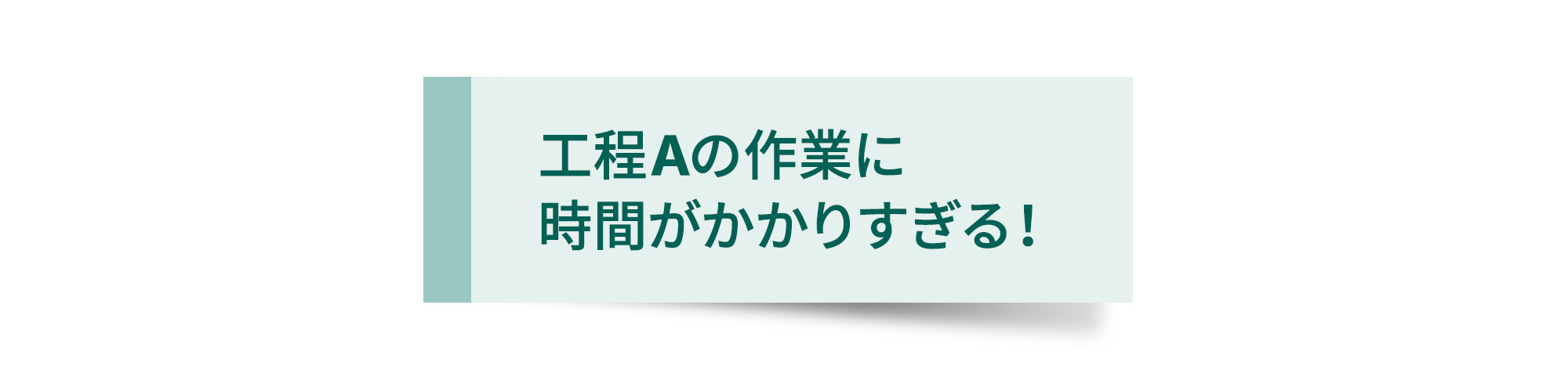
一次要因の探索
C部品にかかわる現場メンバーと一緒に、一次要因を黒字で付箋紙に書き起こしていきます。それぞれ5つほど提出してもらった上で、最終的に以下の4つに絞り込んでいきます。
- 複雑で面倒な作業
- 30年前の設備を使っている
- 治具が使いづらい
- ほぼ担当者のワンオペ
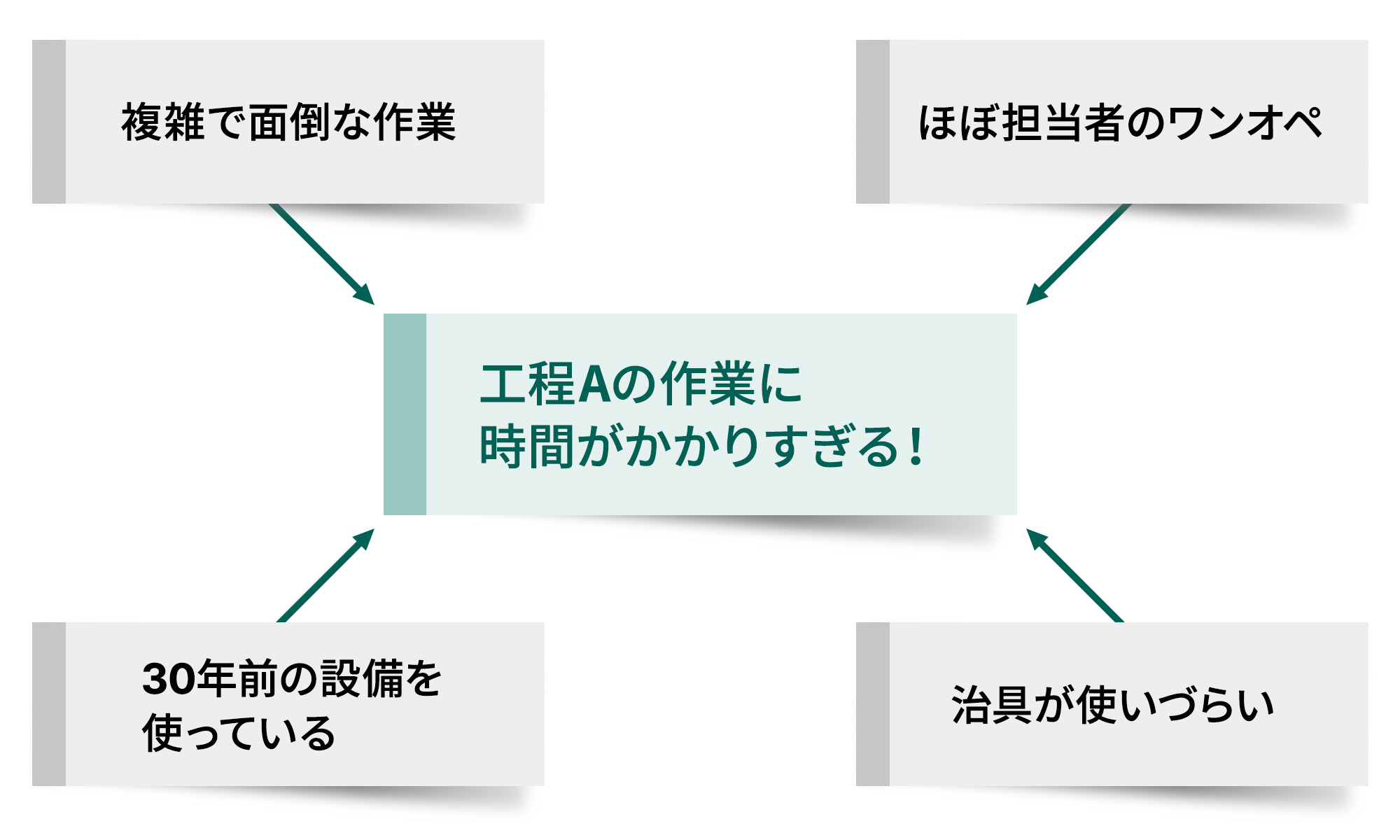
A工程が、熟練技術者の担当者Bさんの依存度が高いことが明確になります。地方の生産拠点とはいえ、DX担当Dさんは「今どき、こんなことが」と驚きます。
二次要因以降の探索
一次要因が十分に絞り込めたら、続いて各要因のさらなる要因となる二次要因、三次要因を「なぜなぜ問答」で探索していきます。案の定、高難易度の作業の存在が明らかになります(図5)。
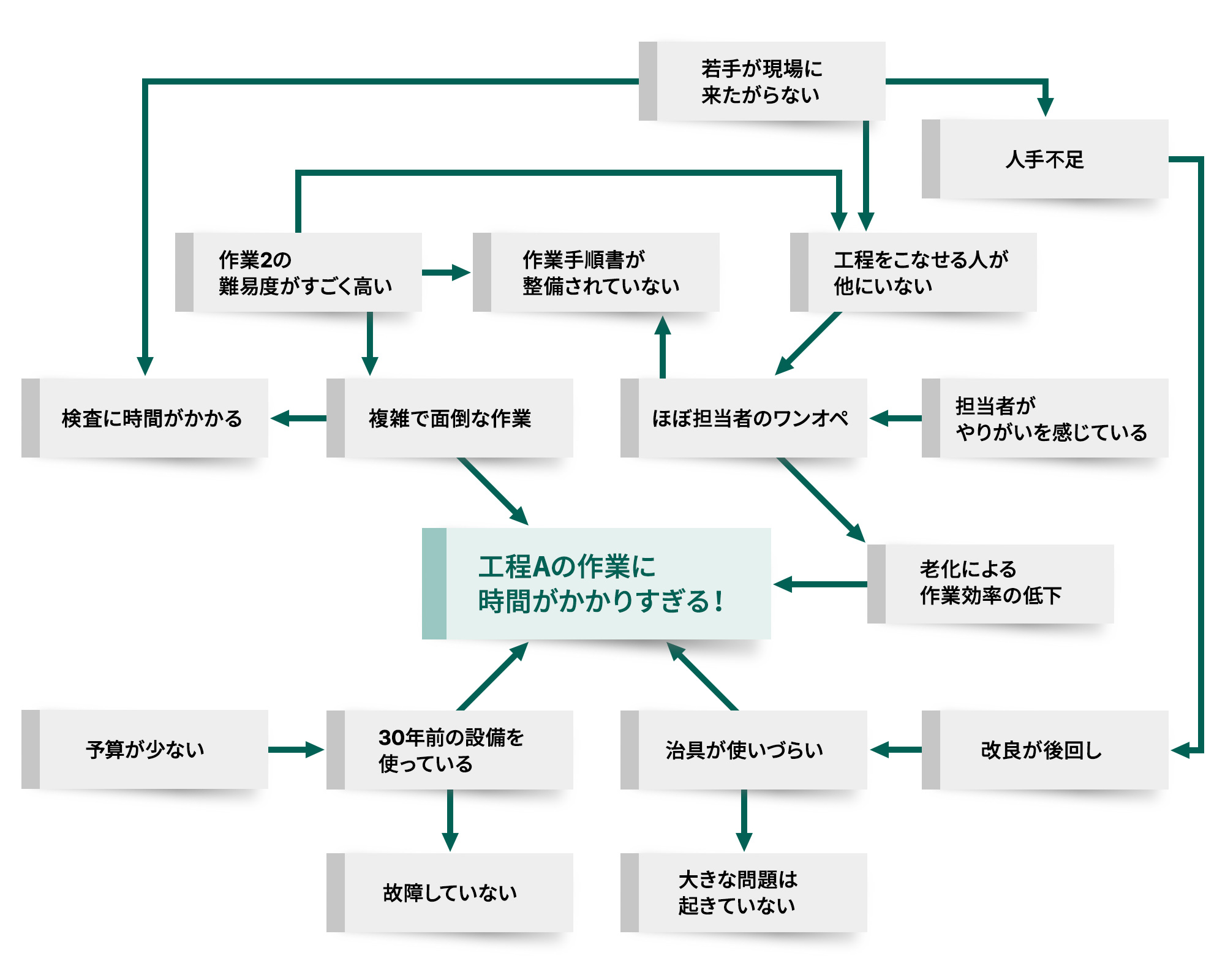
実はBさん、社内規定の定年退職の年を過ぎているのですが、「C部品が作れなくなってしまう」ということで、退職を引き留められているそうです。C部品が作れなくなると、困るお客さまがたくさんいます。
Bさんと話すと、「特に趣味もないし、仕事をしている方が良いんだ。お客さんも喜んでくれるでしょう」と笑っていました。Dさんは、ロボットを導入することで「Bさんの生きがいを奪ってしまうことにならないか」と悩みます。
主要因の特定
連関図の全体像が仕上がったところで、現場メンバーと議論しながら、メインテーマに大きな影響を及ぼしている「主要因」を特定します。ディスカッションを通じて要因ごとに点数で重み付けを行い、点数が多い1~3つを主要因とみなす手法がよく行われます。
今回は、皆で話し合った上、「作業2の難易度がすごく高い」「若手が現場に来たがらない」「担当者の老化による作業効率の低下」を主要因としました(図6)。
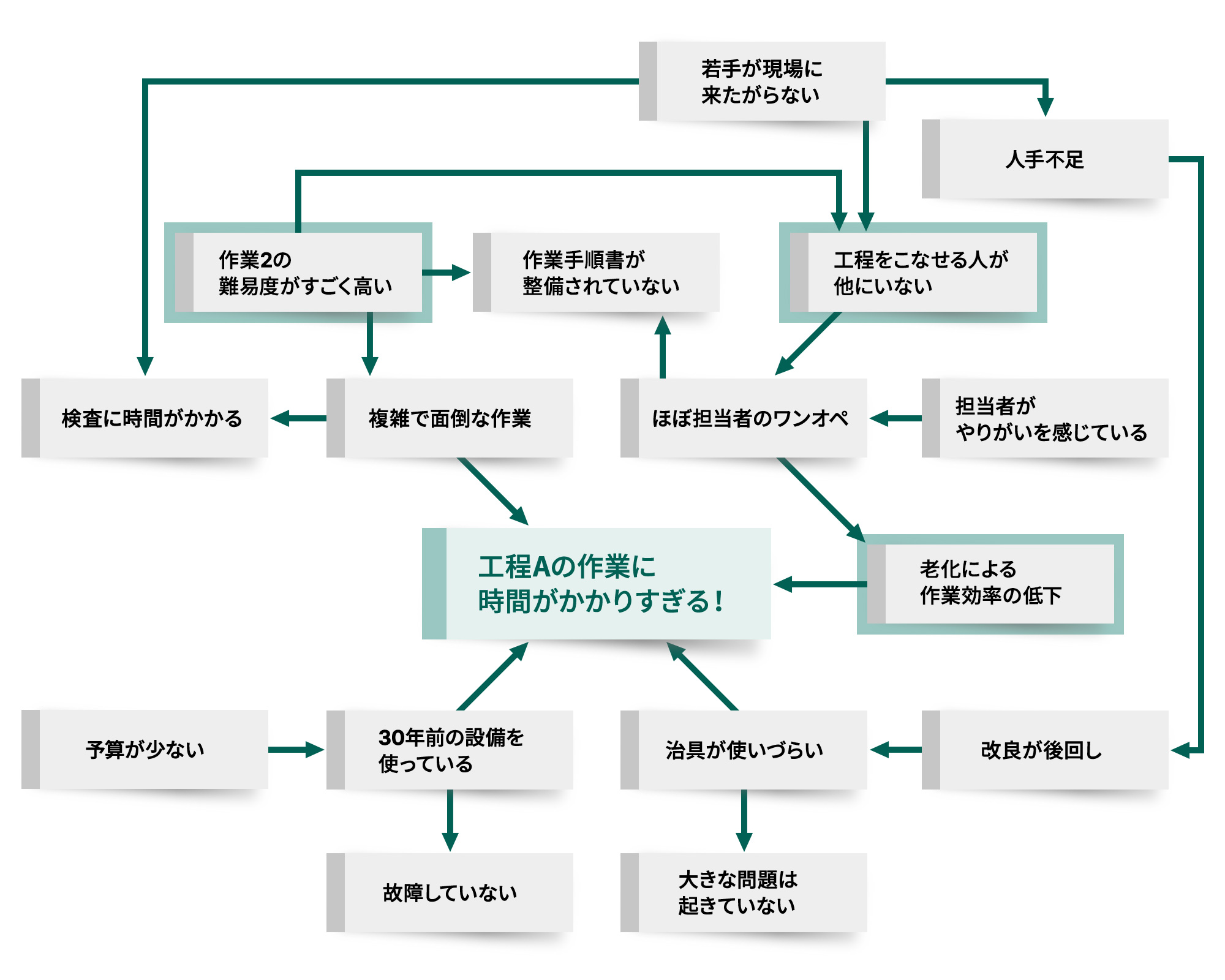
作業の遅れについては、Bさんがワンオペであること自体が問題というわけではないようです。「Bさんの作業の作業、以前はもっと早かった」という声が。Bさんも、その自覚はあったようです。Bさんの体力や気力次第で工程の効率が左右される状況には、大きな問題があります。
「僕は、もう引退すべきかしら……」としょんぼりするBさん。しかしC部品のチームの皆は、「これからも一緒に働きましょう!」と元気づけました。
その後、プロトリュード社では、SIerからの提案で、「作業2」のBさんによる一部の手作業を残して協働ロボットを導入して作業の効率化を図りました。さらにカメラセンシングによる検査工程を導入。工程Aの作業遅れの問題は解消でき、納期もこれまでより早めることができました。
Bさんの技術力や、今回導入した最新鋭の設備のことを聞いた社内の若手が、自ら希望して異動してきてくれました。現在は、カメラセンシングを使ったBさんの技術継承に取り組んでいます。
連関図法を活用して現場の改善に取り組む
問題発生の根をしっかりと断つためには、表面的に見えるトラブルだけに着目するのではなく、潜在的に隠れている要因まであぶり出して精査すべきです。「なぜなぜ問答」をしながら複雑で多岐にわたる要因を、論理立てて分かりやすく可視化できる連関図は、そういった場面で活躍します。
参考文献
「新QC七つ道具の使い方がよ~くわかる本」(今里 健一郎・著/秀和システム・刊)
「JSQC選書26 新QC七つ道具 混沌解明・未来洞察・重点問題の設定と解決」(猪瀬正守・著/日本規格協会・刊)
執筆者プロフィール
facet代表 ライター、編集者。
一般社団法人 日本デジタルライターズ協会 会員。
町工場でのトレースや設計補助、メーカーでの設計製造現場での実務を経験した後、アイティメディア株式会社に入社。「MONOist」の立上げから参画し、月間100万PV以上の業界最大手サイトに成長させるべく尽力した。MONOistの編集記者として約12年間、技術解説記事の企画や執筆の他、広告企画および制作、イベント企画など、幅広く携わる。
2019年には3D設計コンサル企業の株式会社プロノハーツにジョインし、広報・マーケティング担当として従事する傍らで、製造業に特化したライティング事業を展開する。
2020年5月に個人事業として独立。
■主な執筆歴
- アイティメディア「MONOist」「TechFactory」「キーマンズネット」
- 日経BP「日経ものづくり」「日経クロステック」
- 金森産業「PlaBase」
- オートデスク「Redshift」
■書籍
- 一般社団法人セーフティグローバル推進機構
- 『実践!ウェルビーイング世界最強メソッド「ビジョン・ゼロ」』(日経BP)
- 「カーボンニュートラル 注目技術50」(日経BP、ムック)
- 「SDV革命 次世代自動車のロードマップ」(日経BP)
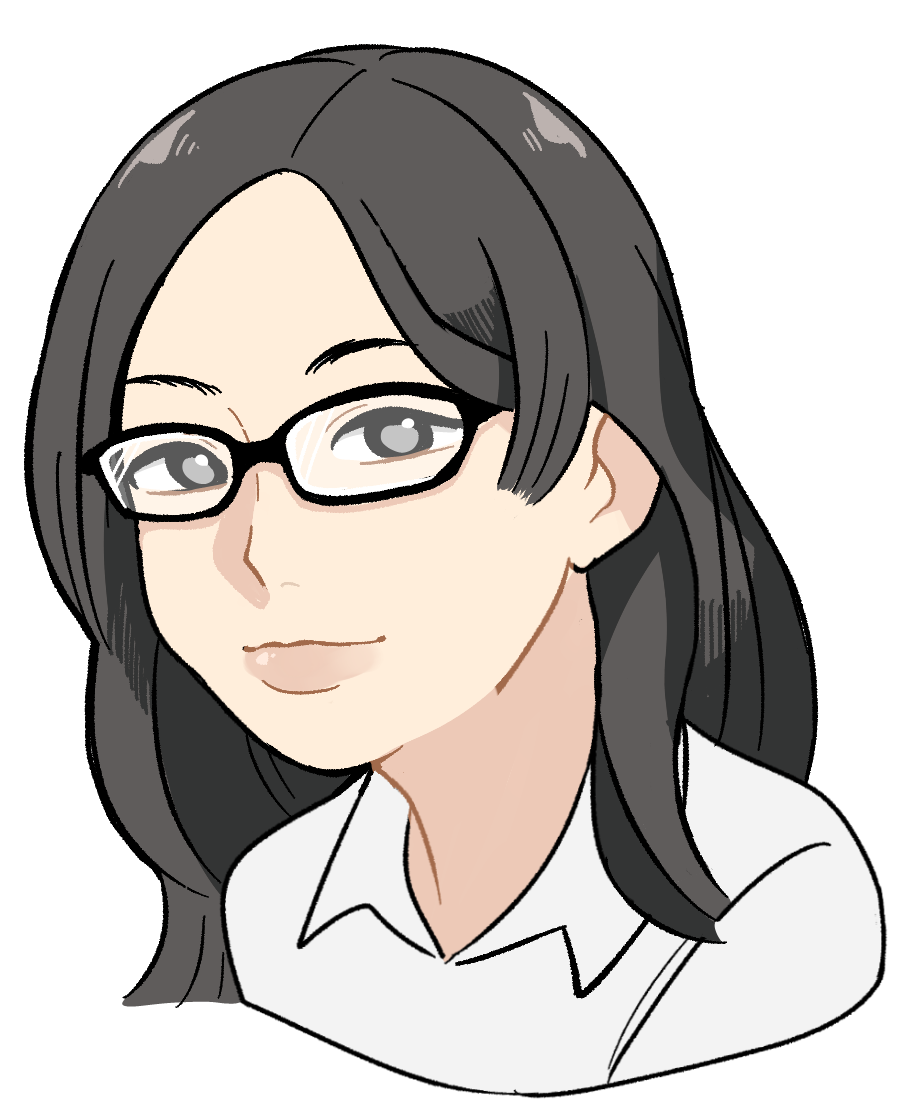