目次
製造業での品質管理を中心としたいろいろな業務の問題解決で使える「製造業新QC/QC7つ道具」について基本から解説します。いまさら聞けない人や、誰かに教えないといけない人も、ぜひご活用ください。
(執筆:小林由美 / facetライター、編集者)
記事一覧:【連載】「新QC&QC7つ道具」基本のキ
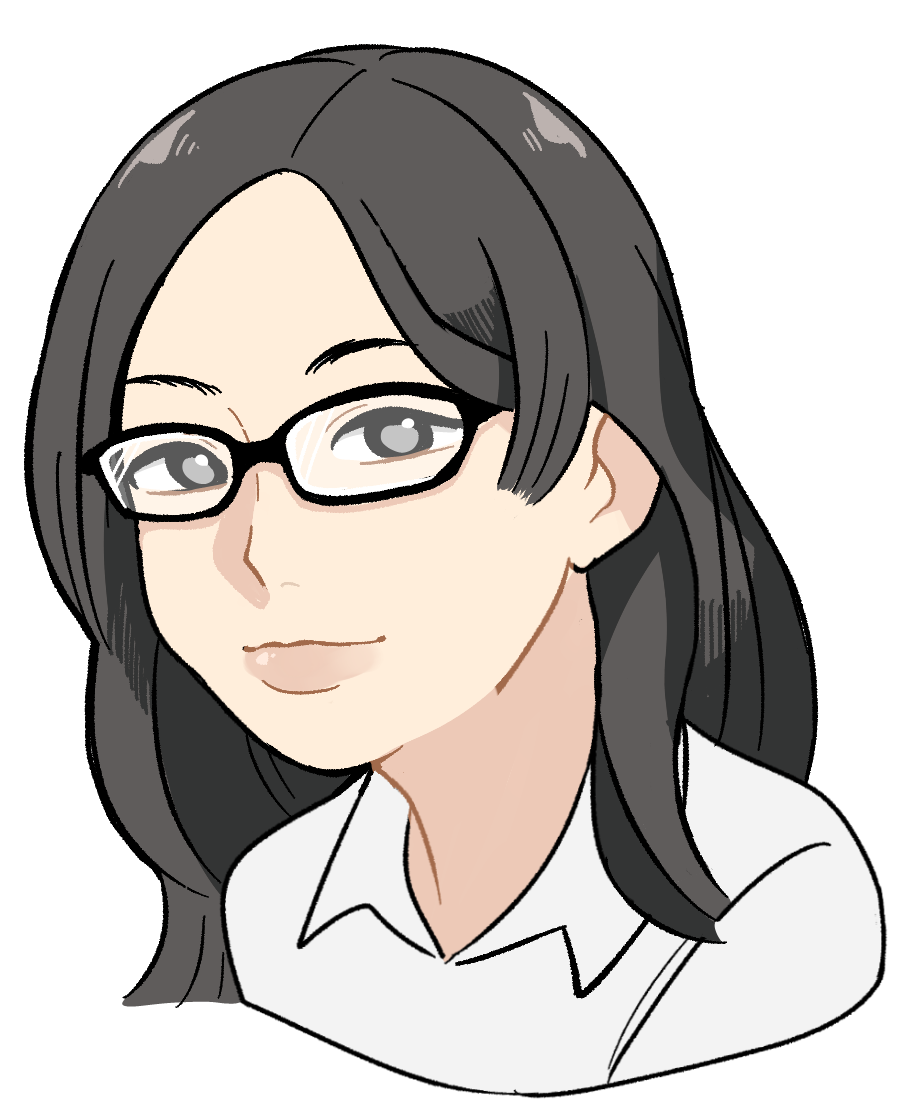
問題に対する複雑な原因をもれなく効率よく調べる「特性要因図」
世の中、「●●という結果の原因は、〇〇だ」とシンプルにはいかないことが多いというのは、誰でも容易に想像が付きます。特に設計製造の世界では、ある問題に対する原因は非常に多岐にわたることがあり、しかも複雑に絡み合っていたりします。また、そのような複雑な要因を調べる際に、その人の思考の隔たりや思い込みが強く影響してしまうこともあります。
そのため、情報をうまく整理しながら、極力見落としがないよう慎重に要因を検討しなければなりません。とはいえ、時間には限りがありますし、悠長にダラダラと考え続けるわけにもいきません。特性要因図をうまく使用することで、自分の思考や参加メンバーの議論が発散しないよう交通整理をしながら、効率よく原因究明を進められるようになります。
特性要因図とは、ある結果と要素の因果関係を視覚的にまとめた図のことです。図がまるで魚の骨に見えることから、英語圏では「Fishbone chart(フィッシュボーン・チャート)」と呼ばれます。日本語でも「魚の骨図」と言うことがあります(図1)。
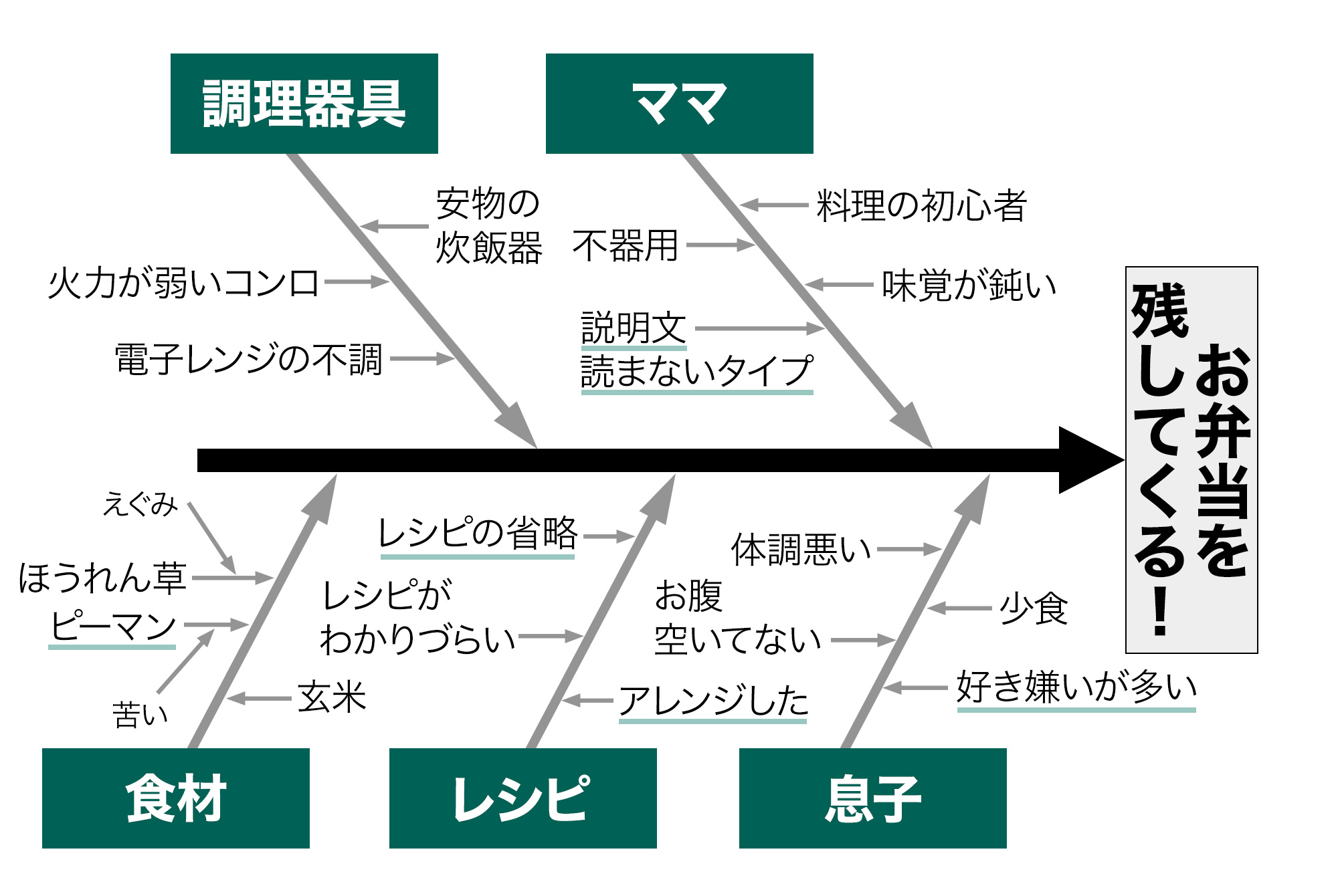
特性要因図を見ると、矢印がたくさんあることに気が付くと思います。左から右に向かう形になります。一番右には「特性」(結果)を示す大きな箱があり、その周囲に「要因」(原因)の小さな箱があります。中心には、特性の箱に向かって伸びる大きな矢印の主骨があり、要因の箱から生える矢印である大骨が主骨に向かってぶら下がっています。大骨はさらに中骨、小骨と枝分かれし、要因もそこに紐づいて枝分かれしていきます。このように要因を細かく分類して可視化しながら、漏れがないように洗い出していきます。
こぼれ話:
特性要因図の矢印がなぜ左から右なのかは、明確にルールとして決められているわけではないようです。単に日本語の横書き記述が左から右へ読むものでそれが自然だからであると考えられます。
特性要因図と4M
品質管理業務において、「QC7つ道具」として特性要因図を描く場合は、解決したい問題に関する「特性」に対する「要因」に「4M」を当てはめて考えます。4Mは「Man(人)」「Machine(機械)」「Method(方法)」「Material(材料)」の頭文字です。
4Mに「Measurement(検査・測定)」を加えた「5M」、さらにそこへ「Environment(環境)を加えた「5M1E」、「Management(マネジメント)」を加えた「6M」もあります。さらに徹底的に要因を抽出したい場合、要因が広範囲にわたる場合などは、5M1Eや6Mを使います。
もちろん4Mや5M1Eに基づいて要因を設定しない場合もあります。例えば製品設計や加工業務など向けに描く場合は、一部を変えたり、実業務に関連する言い方や要因にしたりします。一方、製造業や品質管理ではない場合でも、4Mによる要因整理が応用できます。
品質管理における特性要因図の描き方例
実際に、品質管理での特性要因図の例を見てみましょう。今回は、「不良率増加」を解決すべき特性として定めて、4Mで考えていきます。右端の「特性」には「不良率増加」と描き、そこに向かって主骨となる矢印を1本引きます(図2)。
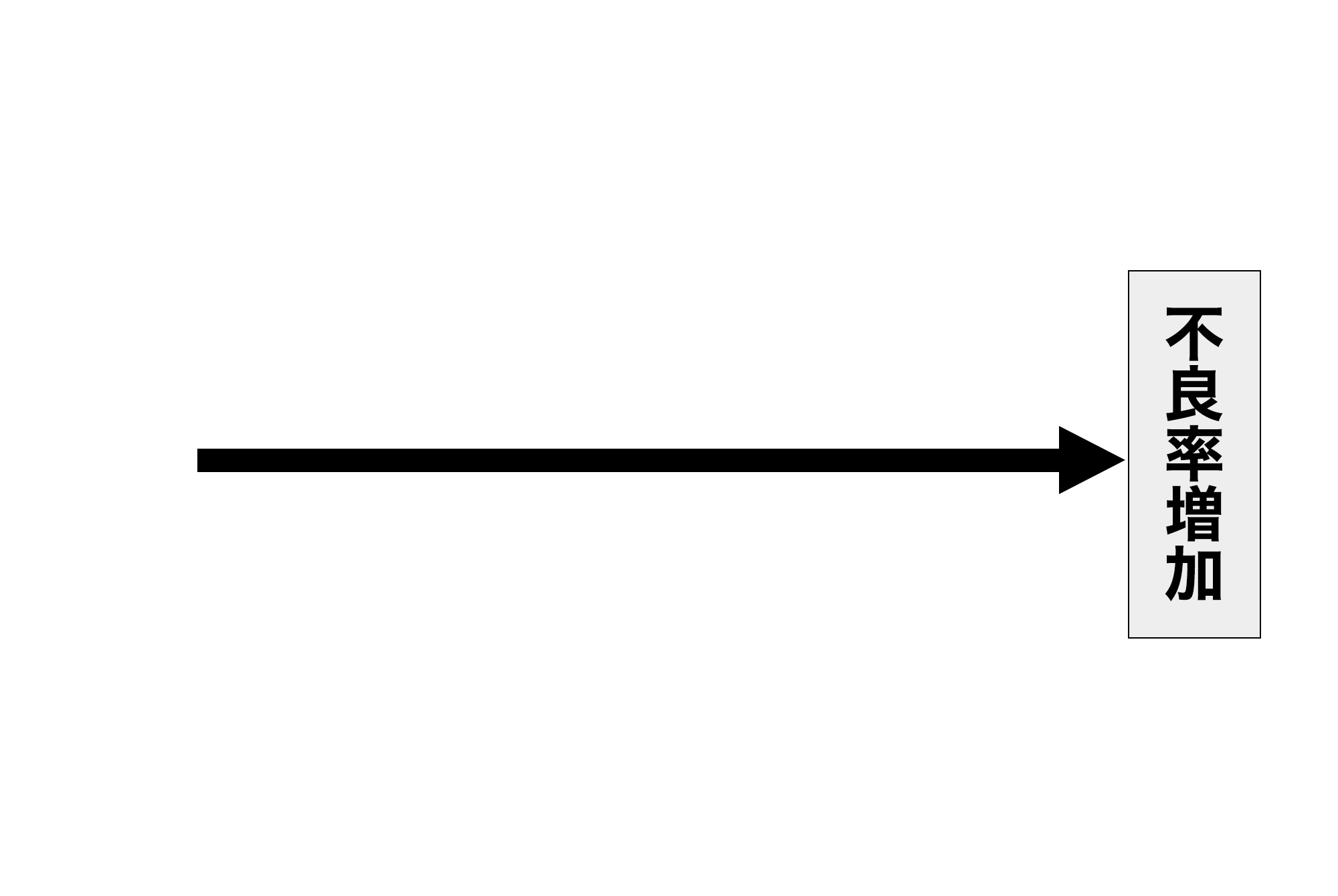
特性の記述はできる限り具体的である方が望ましく、可能であれば「不良率が10%増加した」など定量的に定める方がより良いです。ここでは解説をシンプルにするため、「不良率増加」としています。
さらに特性に対する要因として、「人」「機械」「方法」「材料」の4つの箱を描きます。4つの箱から大骨となる矢印(灰色)を主骨に向かって伸ばします(図3)。
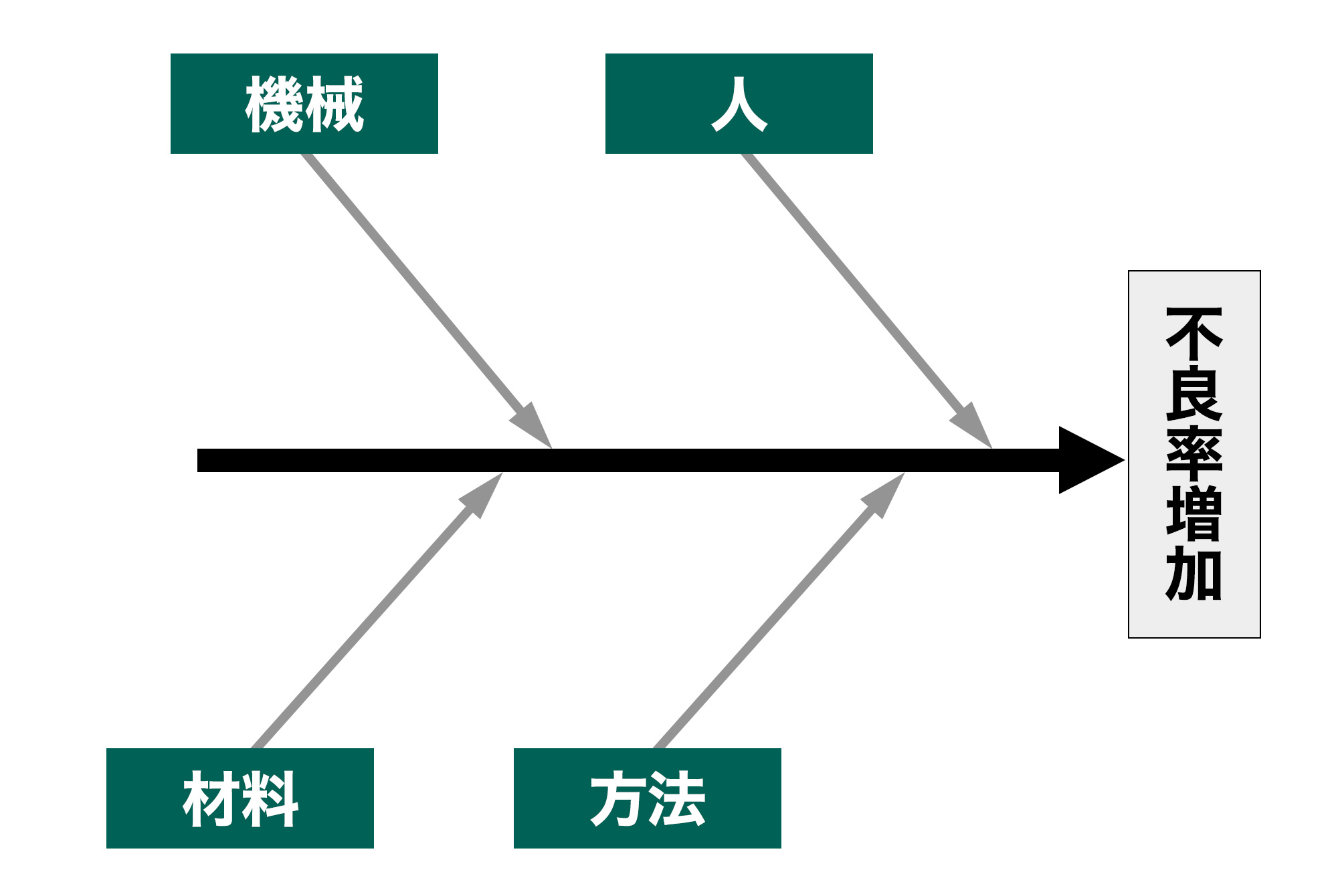
例では4Mが描かれている大骨にくる要因の数は「必ずX個まで」といったルールもないのですが、せいぜい6つくらいまでの場合が多いです。
さてこれ以降は、「人」「機械」「方法」「材料」に対して、「不良率増加」につながる要因を挙げていきます。例えば「機械」では、「監視精度が低い」といった要因が挙げられます。「人」なら「スキル不足」「人手不足」「育成制度が充実していない」、「材料」であれば「メーカーの変更」、「方法」は「設定値があいまい」「マニュアルが更新されていない」などが考えられます。
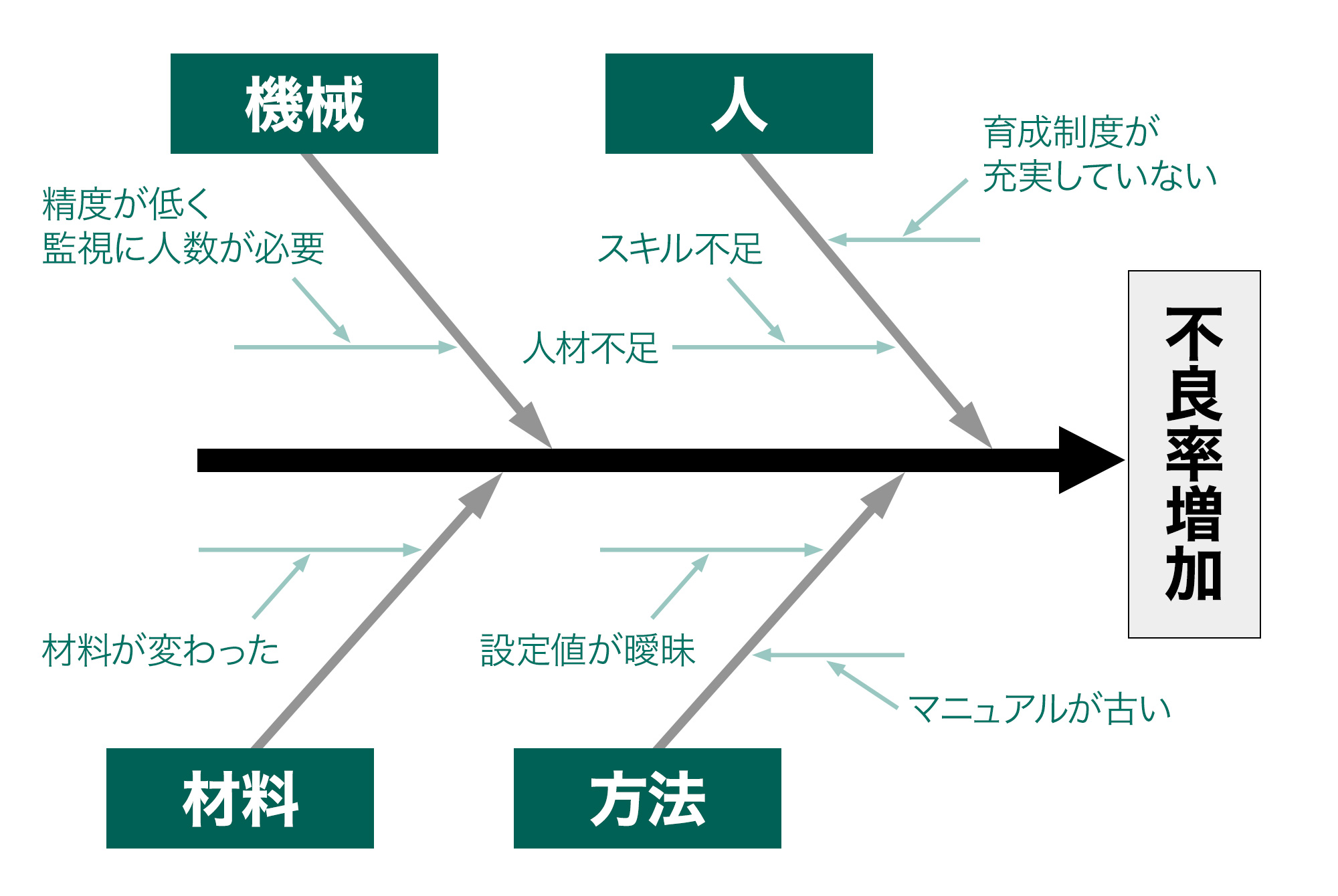
大骨で要因を挙げたり、中骨や小骨で掘り下げたりする際には、できるかぎり主観を排除し、事実に基づいて客観的になるように考えます。現場の作業担当や設備設計者など、さまざまな関係者の意見を聞きながら多角面から議論し、抜け漏れがないようにします。
中骨や小骨となる要因まで挙げ終わった後、特性に対して特に影響があると考えられる重要な要因を絞り込みます。図5のように、真因と考えられるものにしるしを付けていきます。
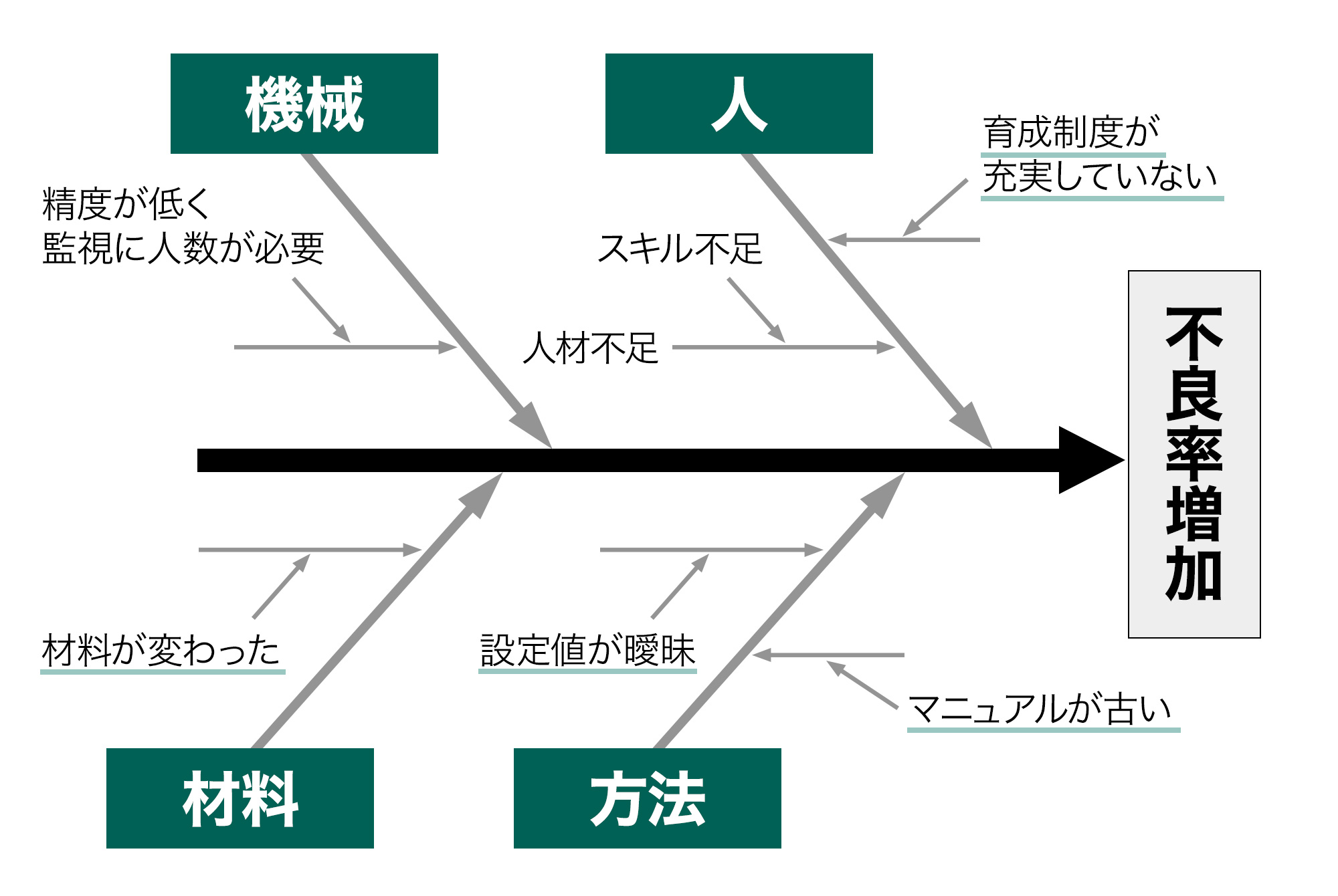
「育成制度が充実していない」「材料が変わった」「設定値があいまい」「マニュアルが古い」という要因から考えられる原因としては、「作業担当者の作業に関する知見が不足していること」「現場での情報共有が十分ではないこと」などが挙げられます。
特性要因図を作って終わりに非ず!
品質管理の現場においては、特性要因図が描き終わり原因を特定したら、「いろいろな詳しい人から話を聞いたんだし、これが原因で間違いない!」と終わりではありません。現場で確認しなければ、「原因」ではなく、「それが原因だという“思い込み”」でしかなくなります。
特性要因図ではっきりとした仮説を踏まえて、「実際に本当にそうなのか」と現場や、現場の過去データに基づいて検証します。ここでは現状のマニュアルを使って作業をしてみる、材料を基に戻して作業をするなどして、実際に製品に不良が出るかどうかを確認します。
こうした検証を経た後に本当の原因、つまり「真因」が確定したら、いよいよ問題への対策に移れることになります。
参考文献
「QCストーリーとQC七つ道具」(内田修、𠮷富公彦・著/日本能率協会マネジメントセンター・刊)
執筆者プロフィール
facet代表 ライター、編集者。
一般社団法人 日本デジタルライターズ協会 会員。
町工場でのトレースや設計補助、メーカーでの設計製造現場での実務を経験した後、アイティメディア株式会社に入社。「MONOist」の立上げから参画し、月間100万PV以上の業界最大手サイトに成長させるべく尽力した。MONOistの編集記者として約12年間、技術解説記事の企画や執筆の他、広告企画および制作、イベント企画など、幅広く携わる。
2019年には3D設計コンサル企業の株式会社プロノハーツにジョインし、広報・マーケティング担当として従事する傍らで、製造業に特化したライティング事業を展開する。
2020年5月に個人事業として独立。
■主な執筆歴
- アイティメディア「MONOist」「TechFactory」「キーマンズネット」
- 日経BP「日経ものづくり」「日経クロステック」
- 金森産業「PlaBase」
- オートデスク「Redshift」
■書籍
- 一般社団法人セーフティグローバル推進機構
- 『実践!ウェルビーイング世界最強メソッド「ビジョン・ゼロ」』(日経BP)
- 「カーボンニュートラル 注目技術50」(日経BP、ムック)
- 「SDV革命 次世代自動車のロードマップ」(日経BP)
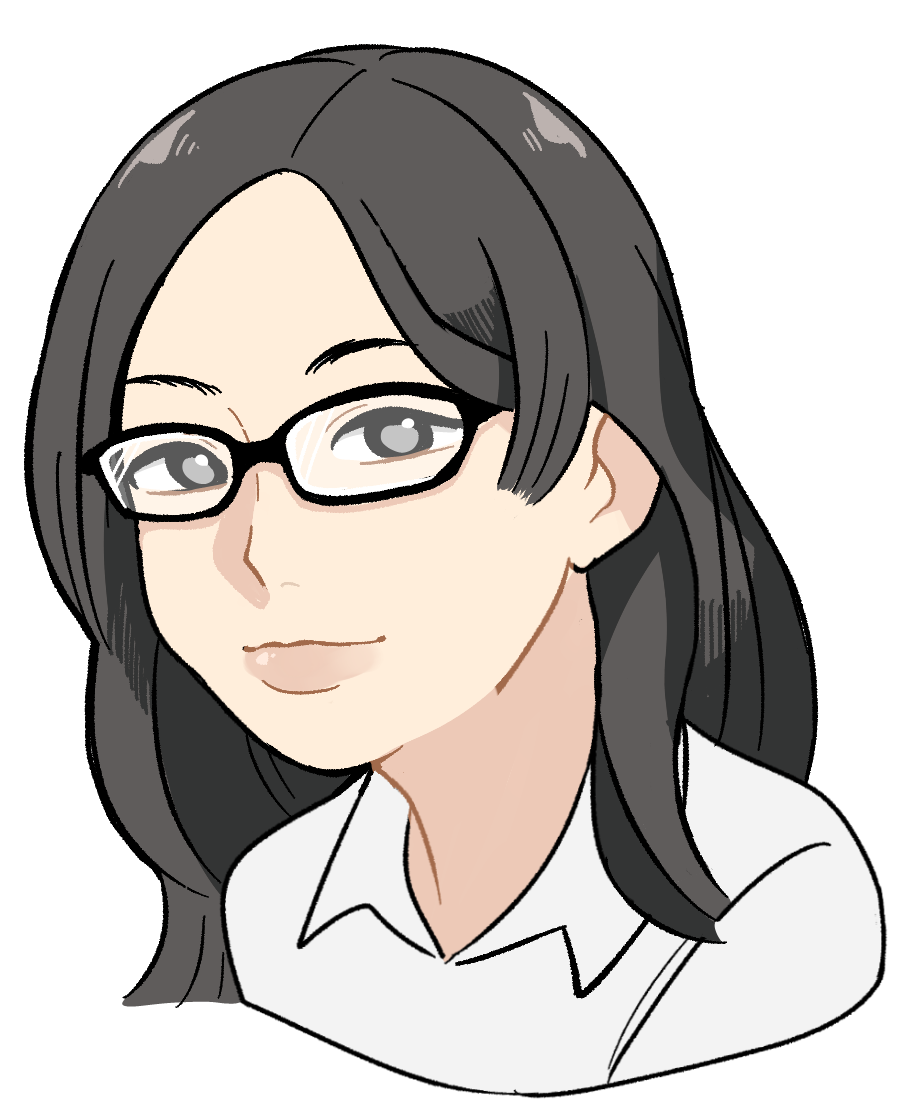