目次
前回からひきつづき、トヨタ生産方式(TPS) 7つのムダへのアプローチを通じてKAIZEN for DXを語っていきます。今回は4つ目の「加工そのもののムダ」についてお話しします。「加工」というと非常に範囲が広いのですが、今回は筆者の頭に真っ先に浮かぶ金属加工を例に解説します。
記事一覧:【連載】関伸一の「ものづくりDX研究所」
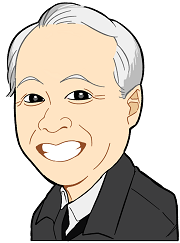
加工のムダとは?
工具による切削加工、金型によるプレス加工、レーザーやウォータージェットによる切断加工などなど、金属加工にもさまざまな種類があります。例えば切削加工はエンドミルやドリル、バイトなどの硬い刃物で金属材料を削る方法です。削れば当然切粉などの廃棄物が出ることになります。
筆者の尊敬する本田宗一郎氏が切削加工をしている技術者の背後から、「君は製品を作っているのか? それとも切粉を作っているのか? どっちだ?」と言ったというエピソードは有名ですが、「できるだけ削る部分が少ないムダのない設計をせよ」という指導だったのでしょう。
長野の板金企業・タカノによる金属3Dプリンターによるムダ取り
「新しい概念で金属加工そのもののムダを排除する」という視点では、やはり金属3Dプリンターを取り上げなくてはなりません。金属を少しずつ積み上げてものを作って行くこの工法は「積層加工」や「AM:Additive Manufacturing」(付加製造技術)と呼ばれ、従来の切削加工や鋳造加工では不可能な形状が実現できます。
図1の左にある写真は、株式会社タカノが、金属3Dプリンター( 「TruPrint1000」(独トルンプ社製)で製作)で造形したものです。タカノは、筆者がここ数年現場改善支援に携わっている長野県松本市の精密板金企業です。
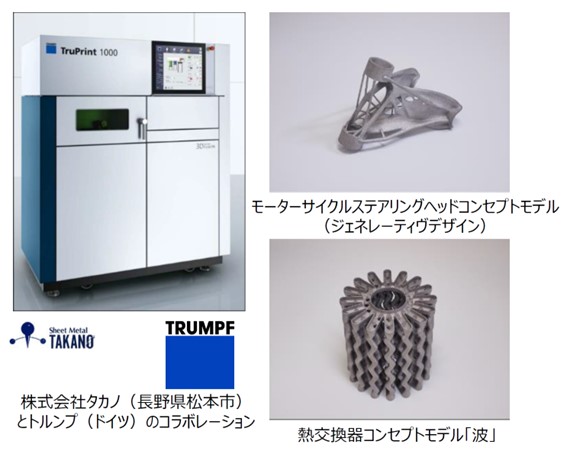
図1:金属3Dプリンターと造形物(出典:株式会社タカノ)
図1右上の写真は「モーターサイクルステアリングヘッドコンセプトモデル」です。キャスター角、フレームとの接合寸法、使用するベアリングなどの主要寸法、そして最低強度などモーターサイクルを設計する上で重要なパラメータを決めた上で、3D CADに「この条件に合致し、かつできるだけ軽いものを作れ」と指示すれば、数千、数万通りの形状を自動生成し、瞬時に強度解析や重量計算を行いCAD自身がその形状を決めるというもので、機械学習、AI、シミュレーション技術の合わせ技となります。これは「ジェネレーティブデザイン」と呼ばれる手法です。ジェネレーティブデザインは、3D CADの「Autodesk Fusion」(オートデスク社製)や「Creo」(PTC製)で採用されている技術です。
ジェネレーティブデザインのようなAIによる自動設計機能は、時に「それでは人間が設計する必要がないではないか」「AIに仕事を奪われる」という反応をする方がいらっしゃいます。そもそも3D CADを使ってモデリングをすることは、筆者に言わせれば所詮「オペレーション作業」であって、設計者がやるべきことはそれ以前の構想設計です。先のステアリングヘッドの件であれば、そのモーターサイクルに最適な操縦性をもたらすパラメータをどうするかです。それはいわば「設計しない設計」といえますが、決して「AIに設計を任せる」という意味ではなく、「モデリングという作業をしない設計」ということなのです。
さて図1右下の写真は、「熱交換器コンセプトモデル”波”」、液体や気体の通路がジグザグになっています。この形状は3Dプリンター以外では作れません。
3Dプリンターでしか作れずに、今までにない高性能な部品の設計はエンジニアのアナログ感性が頼りです。デジタル技術は間違いなく人間のアナログ感性を活性化し、その結果DXが実現すると筆者は信じています。
豊田章男氏が惚れた国本工業のムダ取り技術
今回もう1つ紹介したいのが加工方法を変えることによるムダの排除です。図2をご覧ください。
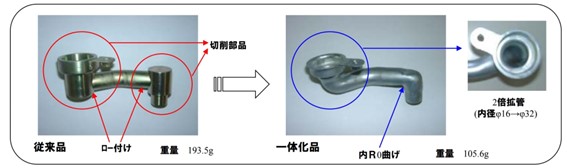
図2:工法変換例1(出典:国本工業株式会社)
従来品は切削部品2点、パイプと板金部品それぞれ1点をロー付けしていたものを、材料の丸パイプをプレス加工して一体化することで、重量、コストともに半減した例です。この劇的コストダウンを実現したのは浜松市の国本工業株式会社です。さらに、この技術を見た、当時(2007年)のトヨタで調達担当副社長を務めていた豊田章男氏が、従業員30人という小規模な企業であった国本工業を、トヨタのティア1として採用しました。
図3ではアルミ鋳物部品をやはり丸パイプのプレス加工で代替し、コスト半減を実現しています。
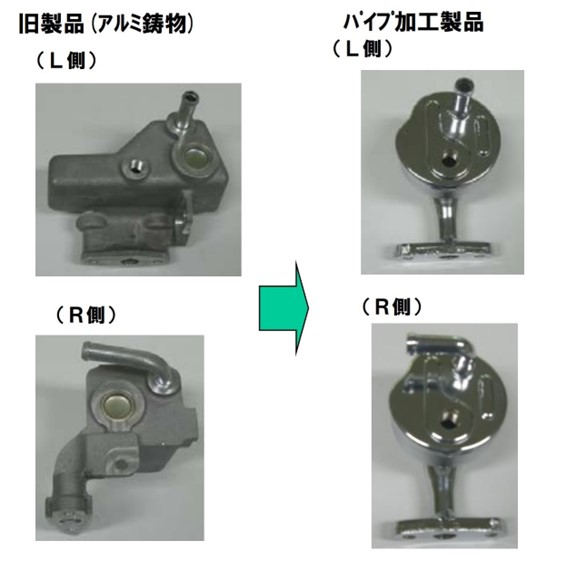
図3:工法変換例2(出典:国本工業株式会社)
もちろん金型設計には3D CADを用いていますが、アナログ感性とデジタル技術を融合させないとこのようなものづくりはできないのです。同社はこの技術で徐々にトヨタおよび関連企業からの受注を増やし、現在は従業員が約90人になっています。トヨタのティア1としてはまだまだ小規模なのですが、パイプのプレス加工という独自の固有技術で躍進する珠玉の企業と言えます。
このような工法変換によるモノづくり改革(筆者は、30%の効果までは「改善レベル」、50%以上の効果は「改革レベル」と定義しています)は、通常の購買活動では実現しません。設計者が鋳物で設計したものを、鋳物メーカーだけに見積もり依頼していてはダメです。板金メーカーや樹脂メーカーにもその図面を渡し(無論、3D図面が好ましい)、サプライヤーならではの固有技術を引き出すのが購買部門の一番の付加価値なのです。
同じ業種での相見積や交渉での値引き合戦など昭和の世界から脱しましょう! 浜松の小さなものづくり企業、国本工業を見出した豊田章男氏のアクションこそ、真の購買マンがやるべきことなのです。
謙虚でイーブンな姿勢が支えるトヨタの強さ
仲間と作り上げた一人完結セル生産が、ものづくり界でそれなりに知名度が上がって、筆者はトヨタ、特に購買部門と積極的に情報交換の機会を持つようになりました。トヨタでの非常に興味深いイベントに、「県別展示会」があります。購買部門主催で、例えば「今月は静岡県の企業技術展示会」という形で単一の県の数十社が製品やパネル展示を行い、開発・設計部門のエンジニアが大勢見に来るというイベントです。筆者も以前度々招待を受け、タイミングが合えば訪れていました。
トヨタのエンジニアはそこで独自の固有技術を持つ企業を見出し、その企業と共同開発を進めるのです。彼らは発注先のサプライヤー企業に対して、決して高飛車な態度を取ったり、上から目線で話したりしないことに筆者は感銘しています。県別展示会のような活動や、サプライヤーに対する姿勢が、トヨタのものづくりの強さを支えているのではないでしょうか。まさにTPS7つのムダの「加工そのもののムダ」、にトヨタ自身が取り組んでいるという好例といえましょう。
記事一覧:【連載】関伸一の「ものづくりDX研究所」
執筆者プロフィール
関ものづくり研究所代表。株式会社Fiot代表取締役。株式会社エコム社外取締役、株式会社桜井製作所社外取締役、国立静岡大学大学院客員教授。
ローランド ディー. ジーにて製造部長として勤務していた時代には、完全一人完結セル生産「デジタル屋台生産システム」を開発。その成果が新聞・雑誌やテレビ番組などで報道されて話題に。ミスミグループ本社では、製造子会社の駿河精機 本社工場長、生産改革室長、環境・品質推進室長を兼務し、業務改善を推進した。
自身の専門である機械工学および統計学を基盤として、品質向上を切り口に現場の改善を中心とした業務に携わる。ISO9001/14001マネジメントシステムにも精通し、経営に寄与するマネジメントシステムの構築に精力的に取り組み、その延長線上として労働安全衛生を含むリスクマネジメントシステムの構築にもかかわる。
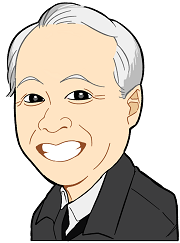