目次
製造業のDX(デジタルトランスフォーメーション)を考える際に、ビッグデータの重要性を欠かすことはできません。ビッグデータとは文字通り、人間が把握できないほど膨大なデータ群をさす言葉ですが、多くの先端技術とビッグデータは切っても切れない関係にあります。たとえばIoTは一連の製造プロセスにおける見えない情報をビッグデータ化するのが目的の1つですし、AIは収集したビッグデータを分析し、判断を行うのが役割です。
本記事ではこのような視点から、製造業でビッグデータ活用に成功している企業12社の事例を紹介します。
製造業におけるビッグデータの主な活用法
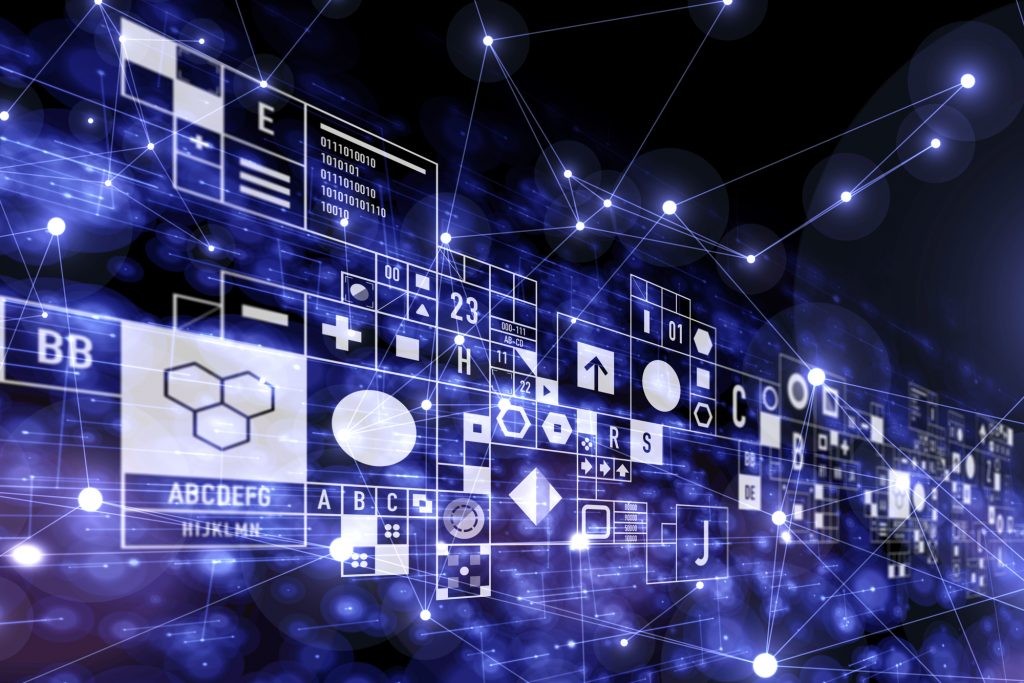
製造業において収集されたビッグデータはデータ分析やAIなどを通して有用な情報へと変換され、さまざまな形で活用されています。代表的な活用法が以下の4つです。
需要予測と仕入れ/在庫の適正化
需要予測においてはビッグデータ、すなわち市場の動向、消費者行動、季節性などの多種多様なデータの分析により、将来の需要を高い精度で予測可能です。需要が予測できれば、生産量や仕入れ量を最適化でき、過剰在庫や品切れのリスクを軽減できます。
これにより販売の機会損失を防止できるのに加え、余分な保管コストの削減や需要変動に対する迅速な対応、経営資源の流動化といったさまざまなメリットが期待できるでしょう。
製造プロセスの最適化
ビッグデータを用いた製造プロセスの最適化では、生産ラインの各段階で生成されるデータを分析し、生産性が低い部分を特定します。機械の稼働状況、原材料の使用量、作業員の効率などの情報をリアルタイムで収集・分析することで、改善余地のある工程を見つけ出し、設備投資や人員配置の変更といった対策を検討していきます。
品質管理の強化
品質管理では、製品の欠陥や不具合を早期に特定するためにビッグデータが用いられます。特に品質管理の中核を担う検査工程で注目を集めているのがAIを用いた検査自動化で、過去に製造した大量の製品画像・データからAIが良品/不良品を判断し、肉眼では見分けられない微細なキズや汚れまで高い精度で判別することが可能です。
設備機械の保守
設備機械の保守においては、ビッグデータが故障予測や予防保守に重要な役割を果たします。機械からの運用データを分析し、故障の兆候を早期に捉えられれば、突発的な故障による生産停止リスクは大幅に軽減できるでしょう。また、計画的なメンテナンスは機械の寿命を延ばすことにも貢献し、長期的なコスト削減に繋がります。
ビッグデータ活用を進めている企業12社の事例
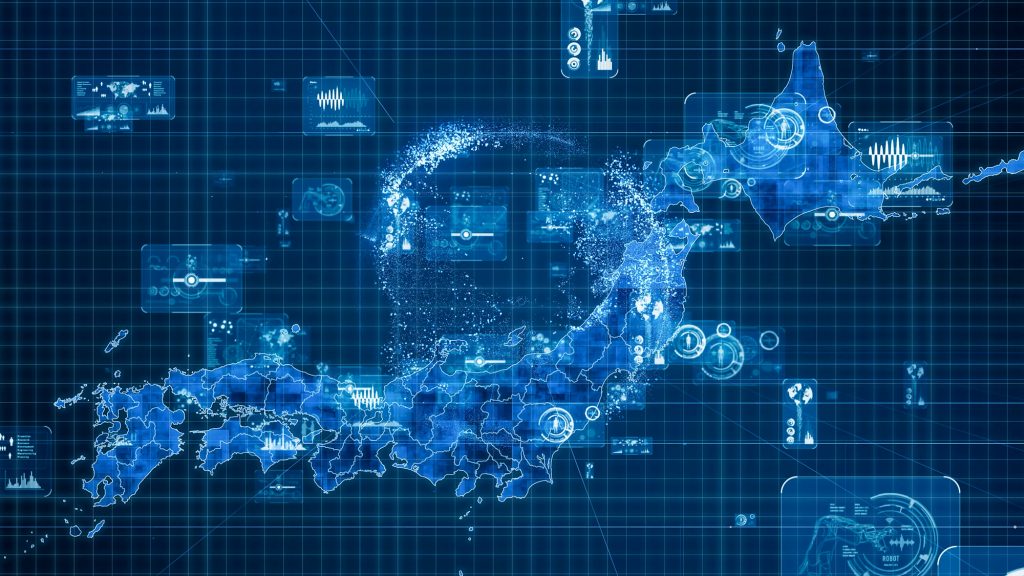
それでは前述した4つの活用法それぞれについて、活用を進めている企業を紹介しましょう。ビッグデータの活用は大企業から中小企業まで徐々に進んでおり、業務の効率化や生産性の向上に大きな効果をもたらしています。
需要予測、仕入れ/在庫適正化の事例
需要予測や在庫管理における活用は、その性質上時期により需要が
①サッポロビール株式会社
サッポロビール株式会社では、2023年7月1日よりAI需要予測システムを本格運用しています。同AIは商品発売の約16週間前から需要予測を開始し、受注状況や販売状況のデータを反映しつつ、出荷量を予測する仕組みです。結果として人だけの需要予測に対し、同AIと人が協働することで約20%、精度を改善することに成功しました。
検証開始当初は人による需要予測に劣っていたこのAIですが、商品情報や過去の販売実績、類似品の販売実績などのデータにより学習が進み、徐々に精度が向上しています。
参考:AI需要予測システムの本格運用開始 | ニュースリリース | サッポロビール
②株式会社LIXIL
株式会社LIXILは2023年4月27日のリリースにおいて、サプライチェーン全体の最適化に向けたAI需要予測の試験運用開始を発表しました。グローバルに事業を展開する同社ではサプライチェーンにおけるリスクマネジメントも重要な課題となっており、在庫管理や業務運営の効率化を目的としてAI需要予測を導入した格好となります。
その結果SKUで230万を超える製品群に対して、AI需要予測により製品それぞれの特徴を捉えた高解像かつ高精度な予測算出が可能となりました。今後は製品だけでなく副資材等も含め、需要予測の対象範囲を拡大する見込みです。
参考:LIXIL、AIを活用した需要予測を導入し、試験運用開始|Newsroom|LIXIL
③株式会社ホリゾン
滋賀県高島市で製本機器の製造を主力事業とする株式会社ホリゾンでは、出荷した機械のアフターパーツ需要に対して、AI需要予測を導入しました。
同社では多品種少量受注を中心としていることから、アフターパーツの需要予測も難しく、従来は発注や在庫の管理を従業員の経験に頼っていました。そこで過去数年間の受注実績をAIに学習させることで、75%の部品について需要予測の精度改善に成功。結果として在庫削減と欠品の最小化を実現しています。
参考:AI導入ガイドブック 製造業へのAI需要予測の導入 p.9-12
製造プロセス最適化の事例
①三菱電機株式会社
三菱電機株式会社ではFA機器の連携により工場内に埋もれているビッグデータの活用を進めました。生産現場とITシステムの連携や、ロボット・センサー機器の活用、高速通信技術などさまざまな先端技術の活用により、工場内のあらゆるデータをシステムにて統合管理しています。
②ダイキン工業株式会社
ダイキン工業株式会社では工場のIoT化により全ての設備をネットワークで連携し、ビッグデータ収集の基盤を構築しました。収集したデータはリアルタイムに共有、見える化され、生産管理や品質管理に活用されています。
具体的には、センサーによる製造現場データの発掘、クラウドやデータベースによるデータの収集と統合、AIを含む各種分析ツールによるデータの見える化と分析、そして分析結果を元にした価値提供という4つのステップのサイクルにより製造プロセスの最適化を実現しています。
③東洋電装株式会社
広島県広島市で制御盤の製造を営む東洋電装株式会社では、小ロット品の生産性向上を目的とした工場のDXを進めました。製造工程を細分化することで自動化できる作業を明確にし、そこにロボットをはじめとしたデジタル技術を導入することで製造効率の向上を図っています。
ビッグデータ活用の施策は、工場内に設置したカメラによるデータ収集です。作業者の動きから進捗や作業時間を見える化することで、想定より時間が掛かっている作業を分析し、人員配置や工程の変更による作業時間の短縮とコストの削減を進めています。
参考:デジタルガバナンス・コード実践の手引き 1.0 DX 取組事例集 p.20-22
品質管理強化の事例
①キユーピー株式会社
キユーピー株式会社は2019年1月から惣菜に使うカット野菜の原料検査装置にAIを用いた画像解析システムを導入しました。食品を扱うことから、変色や変形など無限に近い不良パターンがあるなか、膨大な「良品のデータ」を学習することで不良品の抽出に成功しています。
ボタン1つで操作できる、簡単に分解し洗浄できるシンプルな構造、スペースを必要としないコンパクトさなど、現場の作業環境に合った利便性で、同社の原料に対するこだわりをデジタル面へと反映しています。
参考: AIを活用した原料検査装置をグループに展開 | ニュースリリース | キユーピー
②株式会社丸秀
東京都大田区多摩川で輸送用機器や乗用車の部品製造を手掛ける株式会社丸秀では、品質管理における外観検査にAIカメラ検査システムを導入し、作業者を2人→1人へと削減しました。まずは市販のシステムを導入したものの、複数の向上への展開とさらなるコスト削減を見据えて自社開発システムへの切り替えを行っています。
同社ではITインフラの整備や設備稼働状態の見える化も進めており、複数の工場に設置している100台以上の工場設備の稼働状況をデータ化し、生産工程のムダや故障の予兆などを分析するなど、工場のデジタル化、スマートファクトリー化を進めています。
参考: デジタル活用・DX事例集 vol.35 株式会社丸秀 ~EVシフトによる危機感をDX・AI活用で乗り越え、スマートファクトリー化を実現~ |東京商工会議所
③株式会社ヒロテック
広島県広島市で自動車部品などの生産を行う株式会社ヒロテックでは、24時間365日無人稼働できるスマートファクトリー化を目指し、DXを進めています。その中でも自動車用マフラーの検査工程では、溶接外観、刻印、寸法計測など様々なチェックをロボットにより自動化し、ヒューマンエラーの防止と従業員の負担軽減を実現しました。
この過程で蓄積した検査データを生産結果の把握や分析につなげている点も特徴です。製造番号ごとの検査結果だけでなく、時系列に蓄積した検査データを活用することで、加工結果の細かな傾向分析を行っています。
参考:第1部第1章第2節 人手不足が進む中での生産性向上の実現に向け、「現場力」を再構築する「経営力」の重要性:2018年版ものづくり白書(METI/経済産業省)
設備機械保守の事例
①日本製鉄株式会社
日本製鉄株式会社では、従来は点検員によって行っていた設備稼働状況のモニタリングにAIを導入し、以上の早期発見や事故リスク軽減へとつなげています。
同社ではかねてより異常検知の自動化を図っていましたが、異常データの件数自体が少ないこともあり、AIモデルの構築が難しいという課題を抱えていました。そこで通常時の設備稼働データを基準として異常なデータの挙動を抽出するインバリアント分析を用いて、この課題を解決しています。
②コマツ産機株式会社
産業機械製造の大手コマツ産機株式会社では、自社製品の付加価値としてAIを活用した予知保全システムを開発し、ユーザーの損失防止と満足度の向上に取り組んでいます。従来より導入していた自社製品の稼働管理システムを拡張し、設備稼働データから部品の寿命を予知する仕組みです。
この仕組みのポイントは、センサー等の後付けにより稼働データを蓄積するのではなく、組み込まれたシステムからデータを取得する点にあります。これによりセンサー故障などの問題や、データ連携の手間を無くすなどのメリットを生み出しています。
参考:産業機械大手・コマツ産機 専門知識がなくても“異常予知AI”を構築できた理由 – ITmedia NEWS
③太陽石油株式会社
東京都千代田区に本社を置き、石油製品・石油副産品を製造する太陽石油株式会社では、石油精製プラントの温度や圧力等を監視するシステムを導入しました。
導入当初は精度が低く、有効なアラームは30%程度に止まっていましたが、そこから緊急停止すべき閾値や爆発につながりかねない限界閾値等を加味してチューニングを行うことで、約10ヶ月の期間で有効アラームの割合を30%→60%へと改善しています。
参考:経済産業省 スマート保安先行事例集~安全性と収益性の両立に向けて~ p.21-22
ビッグデータはあらゆる業務改善の基盤
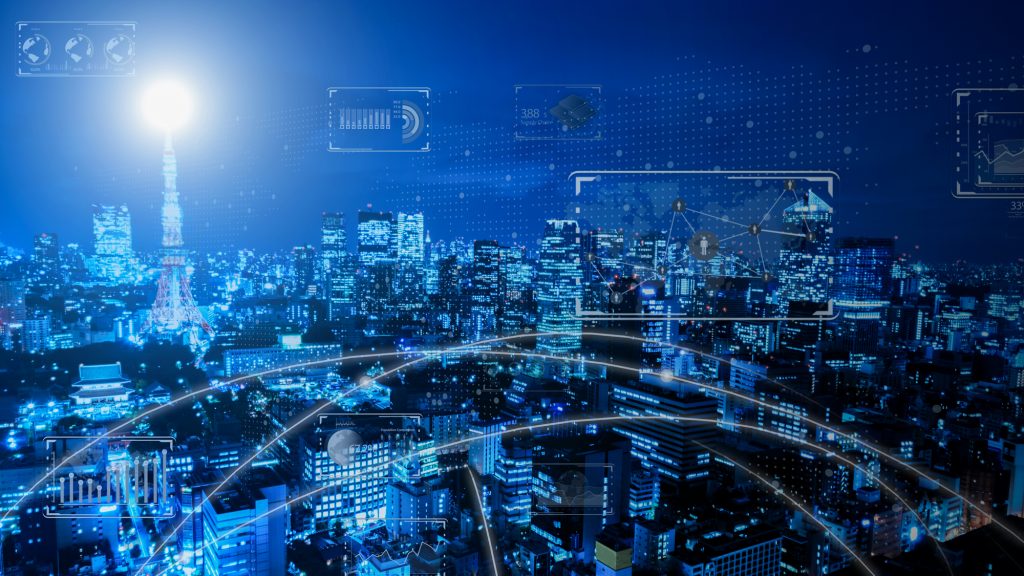
ビッグデータはすなわち製造拠点に眠るあらゆる情報であり、全ての業務改善活動の根拠となり得るものです。その情報をどれだけ収集、処理し分析できるかは、デジタル技術の活用にかかっています。
とはいえ、自社における活用のイメージを明確にすることは容易ではありません。数々の企業の導入事例から自社においてどのようにビッグデータを活用できるのか、そのためにどのような仕組みが必要なのかを検討していくのが1番の近道でしょう。
もちろんこのような事例を支援する立場であるDXコンサルティング会社やシステムベンダーでは、一般的に公開されていない事例についても熟知しています。このようなパートナーと共に、自社と近い企業の事例を踏まえつつプロジェクトを進めることもおすすめできる方法です。