目次
関連リンク:「設備保全」に関する記事一覧
関連リンク:予知保全とは?IoT/AIを用いた進め方やメリット、予防保全との違い
設備の予防保全とは
予防保全とは、「設備の不具合が発生する前に対処を行う」ことを目的に、事前に定めた計画に乗っ取って行う保全活動を呼びます。設備トラブルは日々の稼働による設備や部品の消耗や、状態の悪化が要因となることが少なくありません。このことを踏まえると、計画的な保全活動がトラブルを予防し、生産計画を維持する鍵となります。
予防保全計画を定める4つの方法と具体例
予防保全における計画の立て方は大きく4つの種類に分けられます。それぞれ、どのような考え方で保全活動を行っていくのかを見ていきましょう。
TBM(時間基準保全)
TBM(Time Based Maintenance)とは、時間を基準とした予防保全のことを指し、定期的なメンテナンスを行うことから定期保全とも呼ばれています。設備の故障や、部品の消耗の有無に関わらず、一定周期でメンテナンスを実施するのが特徴です。
しかし、TBMは故障していない設備や部品に対しても一律にメンテナンスを行うため、場合によってはまだ使える部品の交換といった「過剰な保全」によりコストが嵩む場合があります。そのため、トラブルを防止しつつも無駄なコストが発生しないよう、基準となる時間を適切に設定しなければなりません。
CBM(状態基準保全)
CBM(Condition Based Maintenance)は設備の状態を保全活動実施の基準とする手法で、たとえば「部品がここまで摩耗した時」や「設備が何回稼働した時」といったタイミングで部品交換やメンテナンスを実施します。
TBMと比較するとより設備の実態に沿ってメンテナンスを行う手法のため、保全コストを削減できるメリットがあります。一方で基準を適切に設定し、設備の状態を正しく把握するには高度な知識が必要であるとともに、稼働ログの取得やセンサーによる設備状態の把握など人の感覚に頼らず状態を把握する手段を併用する必要があります。
RBM(リスク基準保全)
RBM(Risk Based Maintenance)は、故障した場合のリスクを評価し、結果にもとづいてメンテナンスを計画する、あるいは保全作業の優先度を設定する手法です。「設備のトラブルを防ぐ」というよりも、「トラブルが起きた場合の影響度」を判断基準とする点がTBMやCBMと異なります。
トラブル防止を第一に考える他の手法に比べて、RBMはコストパフォーマンスや合理性を重視している点が特徴的です。RBMを実施する際は、設備が故障した場合に会社へ与える影響を適切に把握し、適切なリスク評価を行う必要があります。
RCM(信頼性中心保全)
RCM(Reliability Centered Maintenance)とは、設備に故障が生じる発生パターンや原因、頻発箇所を調査し、それぞれの設備に対して最適な保全方法を適用する手法です。故障リスクと保全のためのコストを、高いレベルで両立できる一方で綿密なプランニングが必要となり、採用する際の手間や難易度は高いと言えるでしょう。
RCMは適用する設備の機器ごとや、場合によっては部品単位での保全手順や保全計画を立案します。そのため、設備機器の仕様や構造、トラブルの発生傾向などの把握は必須となり、データの収集と分析が物を言う保全方法です。
予防保全のメリット・デメリット
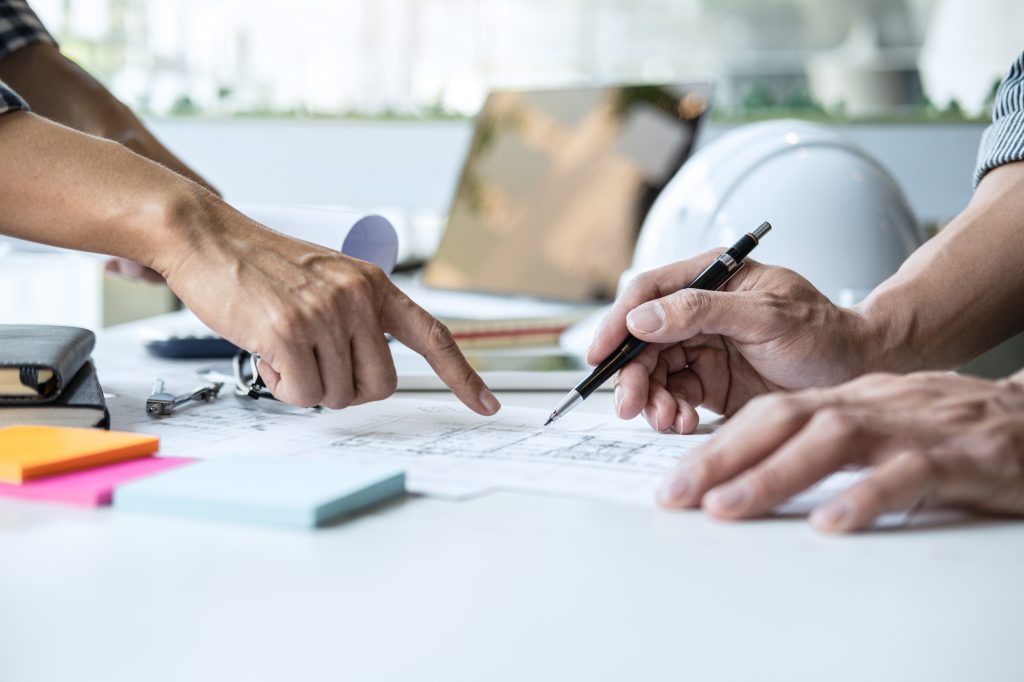
設備トラブルを未然に防ぐ予防保全の考え方には、良い点と問題点の両方が存在します。以下にどのようなメリットとデメリットがあるのかを見ていきましょう。
メリット
設備トラブルの回避やパフォーマンスの向上
予防保全が「予防」と呼ばれるように、定期的なメンテナンスの実施により設備トラブルを回避できる点は最大のメリットです。このことは同時に、設備が良好な状態に維持されることで、高いパフォーマンスが期待できることも意味します。たとえば、設備故障に至らずとも部品の劣化に伴い不良率が悪化する設備があった場合、予防保全が設備トラブルだけでなく不良品の発生も防止し、会社の信頼性向上にもつながる活動となります。
保全活動のスケジュールとコストを算出しやすい
予防保全では一定に近い周期でメンテナンスを行うため、保全活動スケジュールやコスト、リソースの算出が容易である点もメリットです。メンテナンスの実施があらかじめ分っていれば、社内の稼働計画の調整や顧客へのアナウンスなども余裕を持って行うことができ、機会損失の発生も最小限となるでしょう。現場の業務においても予定外の保全活動による無用な混乱を避けられます。
生産管理や在庫管理が容易
生産計画にメンテナンスを折り込めるので、材料や完成品の在庫管理はもちろん、メンテナンスに要する部品の調達スケジュールも容易に管理できます。機器によっては交換部品の調達に時間を要する場合もありますが、このような部品が突発的に必要となると、生産計画の大きな支障となります。材料が滞留することにより在庫管理のトラブルへ発展する可能性もありますので、これらモノづくりに伴う一連のプロセスと物品の管理がスムーズに実施できることは大きなメリットです。
デメリット・課題点
設備の過剰保全によるコストの増加
特にTBMにおいては、設備の摩耗が小さくとも一定期間でメンテナンスを行うことから、「まだ使える部品を交換してしまう」ことが起こります。もちろん使えなかった分は無駄となりますし、その交換に費やす人的コストもまた無視できない損失と言えるでしょう。
突発的な設備故障に対応できない
突発的なトラブルやヒューマンエラー等の外部要因による設備故障、何らかの要因で設備の劣化が著しい場合には、たとえ予防保全であっても対応しきれない可能性があります。また、突発的な故障に対応したことにより、事前に組み立てたスケジュール自体が崩れてしまうかもしれません。そのため、予防保全を導入する際は、予測しきれない故障が発生した場合には、どのように対処するべきなのか、あらかじめ決めておくことが大切でしょう。
基準や計画の設定が難しい
設備の状態を基準に考えるCBMにおいては、「どこまで劣化が進んだらメンテナンスを行う」という基準の設定が難しく、これらの基準を見誤るとトラブルを防止できないどころか、不良品が増加するなどのリスクがあります。
適切なリスク評価が求められるRBMや、綿密なプランニングが必要となるRCMも同様に、計画は容易ではありません。トラブル防止の可能性を高めようとすればメンテナンスのコストが増加し、コストを削減しようとすればトラブルのリスクが高まる中で、最適なバランスを保つ必要がある点が予防保全の難しさです。
予防保全と反対の考え「事後保全」との違い
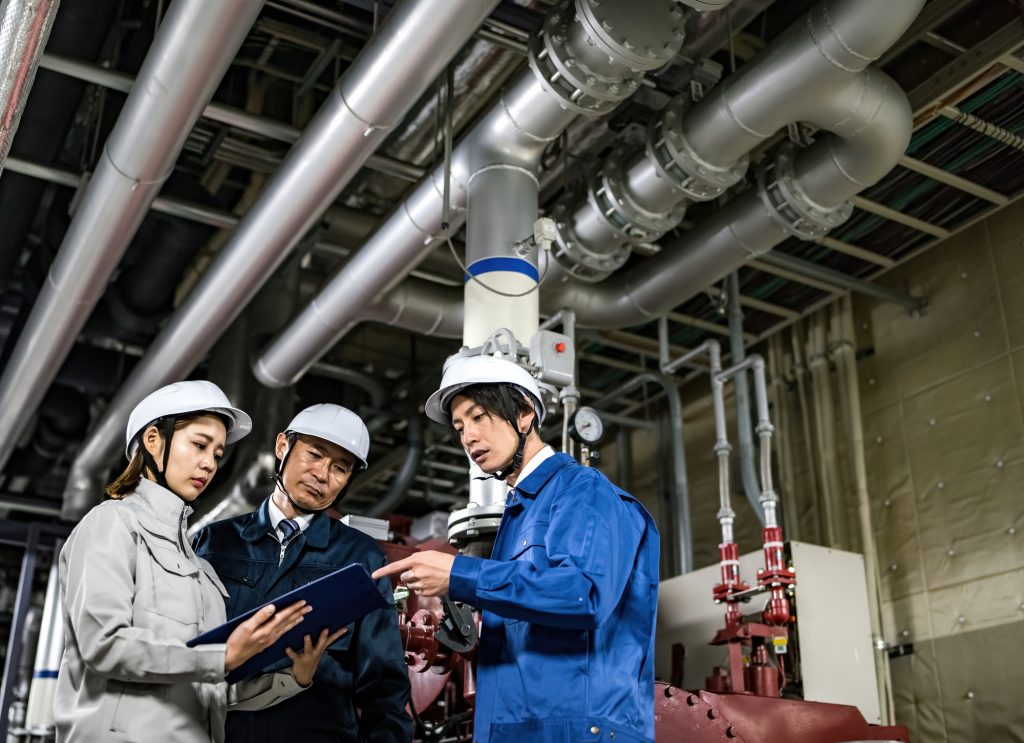
事後保全とは、端的にいえば「トラブルが起こってから行う保全活動」のことを指し、BDMもしくはBM(Breakdown Maintenance)と呼ばれています。一見すると「トラブルを予防できていない」とマイナスな印象を抱くかもしれませんが、日々の活動における消耗が少なかったり、トラブルが起きた際の影響が小さい場合には、保全活動にかかるコストやリソースの削減をする事後保全が適切である場合も少なくありません。
予防保全は、トラブルとそれにともなうダウンタイム発生のリスク削減を目的としていますが、事後保全ではトラブルとダウンタイムの発生は許容する一方で、保全活動に対するコスト削減と、発生してしまったトラブルの早期回復が主なテーマとなります。
予防保全を発展させた「予知保全」との違い
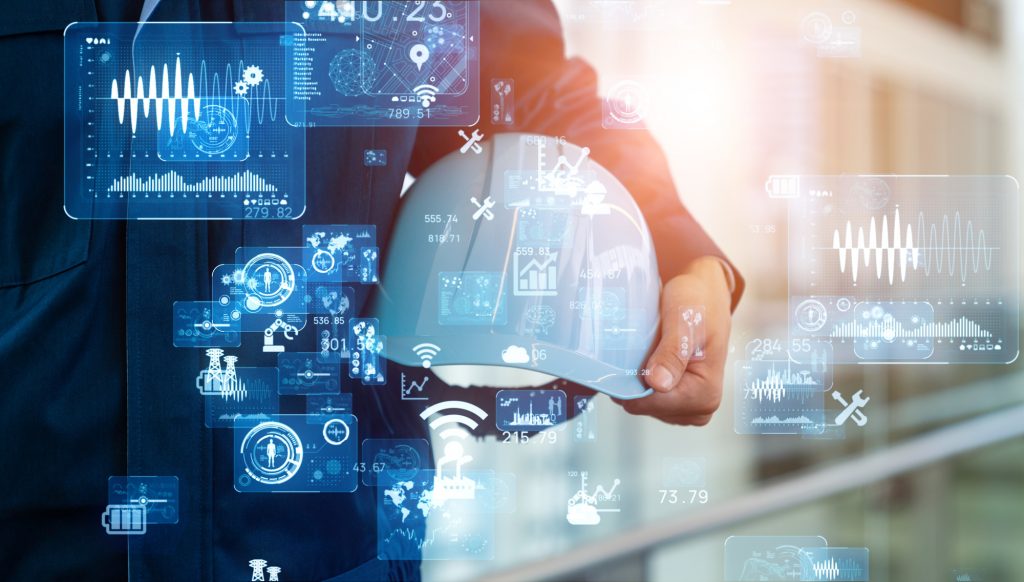
予知保全とは、設備の稼働状況から設備トラブルの発生を事前に予知し、対応を行う保全活動です。トラブルを未然に防ぐという意味では予防保全の一種とも捉えられますが、予防保全は事前に一定の基準を定めるのに対し、予知保全は設備の稼働データや故障時のデータなどから、リアルタイムに「保全活動のタイミング」を予知する点が最大の違いです。
予防保全では時間や消耗度などを基準とし保全活動を行うため、コストやリソースに無駄が生じる反面、設備の状況を十分に把握できていなくとも一定のトラブル防止効果が期待できます。予知保全は設備の状態からトラブルの直前にメンテナンスを実施するため、コストやリソースの無駄が極めて少ないうえ、突発的な故障に対応できる可能性も高まるものの、設備稼働データの収集が必須となります。
データが不十分な場合やデータの精度が低いと予防保全は正しく機能しないため、IoTやAIの導入により自社の製造ラインにおけるデータの収集や管理体制が整うにつれて、予防保全から予知保全へと移行する流れが一般的です。
IoT/AIで進む予防保全から予知保全への移行
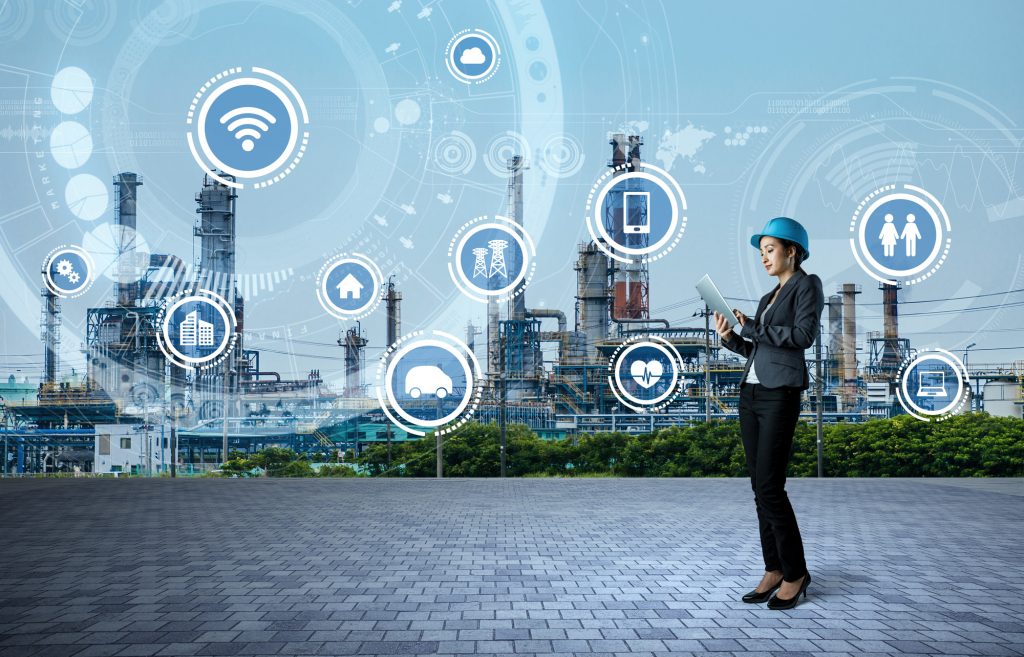
予防保全は、設備トラブル回避の効果が期待できるものの、コストやリソースが無駄になってしまうことは避けられません。トラブル発生時の影響が小さい場合は事後保全とすることも一手ですが、予防保全の強みである「トラブル回避」のメリットを活かしながらも、大きなデメリットである「コストとリソースの無駄」を解消する方法として予知保全が注目されつつあります。
IoTによる設備稼働状況のデータ化とAIによるビッグデータ分析、および異常なデータの検出は予知保全への移行を後押しする技術革新です。これらは、保全活動だけでなく、製造プロセス自体の最適化やDXの基盤ともなる技術ですので、まずは自社の保全活動を見直し、これらの技術の活用を検討してみてはいかがでしょうか。
関連リンク:「設備保全」に関する記事一覧
関連リンク:予知保全とは?IoT/AIを用いた進め方やメリット、予防保全との違い